Drugs for cancer treatment of animals are subject to high quality standards and are manufactured under cleanroom conditions. This was the case with the company PetBioCell, a laboratory producing cancer therapies for dogs, cats and horses. For this purpose, industry service provider WISAG built a new modular cleanroom laboratory within just four weeks.
This module was installed at the Veterinary Clinic of Dr Thomas Grammel in Osterode am Harz, Germany in September.
PetBioCell was founded in 2012 and provides veterinary clinics like that of Thomas Grammel with the possibility of manufacturing cancer drugs. Currently, about 100 cancer patients per year are supplied with autologous vaccines, i.e. individually made for each patient. For the laboratory operator, the new cleanroom solution offers a decisive advantage. ‘To ensure high product quality and professionalism in the manufacture of medicines, a high-quality cleanroom was a prerequisite,’ says Simon Greaves, CEO of PetBioCell and son of the veterinary clinic owner.
‘As a start-up company, it was also important for us to quickly create production capacity while keeping the cost of the cleanroom under control and within budget.’
In total PetBioCell invested €300,000 in the modular solution. In comparison with traditional cleanroom capital costs, there are many areas where using a modular cleanroom of this type can produce savings. For example, the usual fire protection measures necessary in existing buildings can be dispensed with. In addition, the modules are manufactured as standardised units, which not only brings with it a cost advantage, but also enables better planning through the use of standard dimensions for the installation of equipment, materials and the personnel entry systems.
WISAG, one of Germany's largest industrial service providers, was the general contractor responsible for planning and consulting on the entire development of the cleanroom module, including procurement and shipping. The 50m2 large container was assembled in the Dresden production facility of WISAG, then packed in an airtight manner and shipped by truck to Osterode.
Once on site, all the technical components were connected, then all the precision assembly elements completed, such as the sealing of the entire GMP surfaces – ceiling, walls and floor – on site. For the cleanroom specialists this was a particular challenge: ‘Expanding cleanroom capacity with a cleanroom module in the field of veterinary medicine was a new, challenging task for us. The narrow space made the installation of the interior more complicated than usual. Moreover, everything had to be built so that nothing would be affected or damaged during the transport and subsequent reassembly,’ said Fred Kuehne, Project Manager at WISAG in Dresden.
The cleanroom in the module was equipped with high-quality metal walls and a HVAC system that filters out all particles from the laboratory air. It cools, heats and dehumidifies the air and vents it via a filter unit. A pressure cascade must be maintained under all operating conditions, and to produce the required over-pressure for the pressure cascades in the rooms, the air intake is always greater than the air exhausted.
For this, both a complex control system and an independent monitoring system supplied by WISAG were installed. This enables air pressure, temperature, humidity and the number of viable and non viable particles in the air can be continuously monitored. For this purpose, temperature and humidity sensors were installed in the modular cleanroom and particle sensors in the workbenches. Recordings of the individual parameters that must be kept with batch records for at least 10 years can be stored on a computer or data logger with a secure access system.
The fresh air intake system ensures the necessary hygienic outdoor air exchange is maintained as well as air supply for the pressure cascade. In the instances when increased air exchange is required, so-called Filter Fan Units (FFUs) are used in recirculation mode to clean the air above the filter instead of using outdoor air. This solution enables significant cost savings to be made.
In addition, cleanroom class A sterile workbenches were integrated into the cleanroom. This guarantees absolute sterility during the manufacturing process.
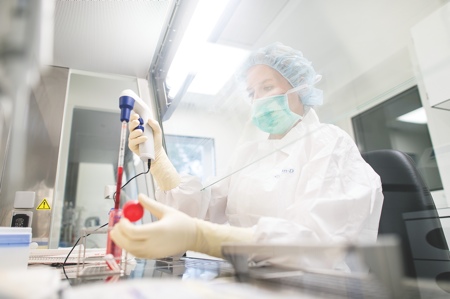
In the cleanroom laboratory animal medicines for about 100 cancer patients are made
To enter the cleanroom, the staff of PetBioCell must adhere to strict hygiene regulations that require them to change clothes, wash, disinfect twice and wear special cleanroom garments in the specially provided personnel entry/change rooms.
Final acceptance by PetBioCell and validation by the Dresden company GemLog were completed at the end of August.
The cleanroom module must meet the highest hygiene and safety requirements to conform to the EU GMP guidelines.
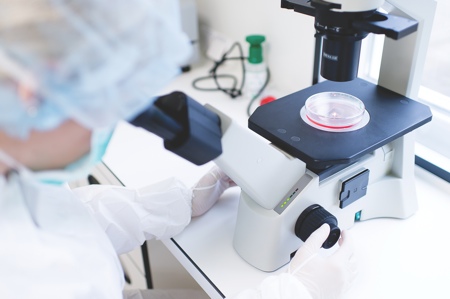
PetBioCell offers the opportunity for drug production through its cleanroom laboratory personnel and veterinary clinics
Looking to the future, the demand for cleanrooms is increasing , especially with the ever more stringent requirements placed on the pharmaceutical and food industries and with the increasing sophistication of technology. As leaders in this field, the German cleanroom sector already employs approximately 15,000 people and accounts for annual turnover of €2.5bn.
For small, medium and start-up companies across all industries, the modular solution offers an important alternative to the traditional cleanroom concept, avoiding high costs and thus minimising economic risks.