Automated cleaning of food production plant usually requires large amounts of water – a costly resource. But Peter Chavasse, Aeolus Technologies, describes how CIP technology is starting to change.
A among the wider environmental audience there remains a pecking order for interest among the sustainability categories, with carbon reduction currently leading the pack. Capturing less attention is reduction in water consumption, the lifeblood of many processing organisations, and in the view of some an equal if not greater priority for focus than carbon reduction.
Fortunately, significant action has and is being taken by processing companies across many sectors to reduce water consumption, as well as reducing waste and carbon; not just to achieve environmental and sustainability objectives but also because it makes simple logical sense to do so where the opportunity exists.
As something new in terms of Clean in Place (CIP) systems, Whirlwind technology has the potential to provide significant environmental, operational and the ever important financial benefits to processing manufacturers.
An article published in a US journal at the end of last year tracked the progress of Clean in Place development over the past 50-plus years, with the summary being that techniques and approaches had evolved over that period but no huge shift had occurred. Aeolus Technologies would like to think that the Whirlwind technology it supplies is providing that revolutionary step change in approach.
Vortex airflow dynamics
The technology was originally developed several years ago to address the need to clear and recover cosmetic cream from pipework at a processing plant in Africa, where there was an underlying water shortage issue. The Whirlwind concept, which utilises vortex airflow dynamics, has been enhanced and refined over the intervening years with systems now available that provide a full clearing, cleaning and drying cycle.
There are four phases to the full cycle:
Phase 1 – a laminar airflow is introduced into the pipework and gently pushes product through the pipework for recovery
Phase 2 – a vortex airflow is generated and controlled in the pipe to remove as much of the remaining product as possible from the inner surface of the pipe walls
Phase 3 – water is injected into the vortex airflow and the combined action of turbulent airflow and water droplets cleans the inner surface of the pipe
Phase 4 – reverting to vortex air only, the airflow is used to dry the pipe ready for the next production batch.
The technology platform is essentially the same for each system; however, each unit is manufactured bespoke as system components are sized and tailored appropriately to meet individual processing plant configurations and product range variations.
While the full cycle comprises four phases, several installations utilise only the clearing/ recovery phases as this is where and how the companies derive the most benefit from the technology, while others hybridise the Whirlwind technology with their CIP kit, and by doing so achieve optimal benefits.
Benefits from installation of the Whirlwind technology include:
- Less than 10% of water used for cleaning compared with traditional CIP, with the water being cold rather than heated
- Reduced effluent for disposal as a result of increased product recovery during the clearing phases
- Reduced energy consumption as a result of water not being heated and a shorter time of operation.
Further benefits include:
- Operation through various obstructions, as well as not being affected by changes in pipe diameter
- A single unit can operate on multiple processing lines
- Straightforward installation, ease of maintenance and low running costs
Key to achieving optimal benefits is ensuring that the system is set up and able to clear and recover as much product as possible during phases 1 and 2. With various flow meters and sensors monitoring flow rates and pressures of airflow through the pipework, product recovery from phase 1 has been as much as 90%, which in turn reduces phase 2 operational time. Through a combination of phase 1 and 2 upward of 95% of product can be recovered for reuse, with some installations recovering over 99%.
The clearer these phases can get the pipe to be, the shorter and more efficient the cleaning cycle, and the greater the reduction in water usage. The process is controlled by software that interfaces with client plant software for either automatic or single push button operation.
Given the environmental pressures, the technology is even more appropriate now than when first designed. Interest is being shown from around the globe as awareness grows and as the adaptability of the technology (which can be retrofitted as well as included in new build) is understood. Current installations are spread across a number of sectors, including food and beverage, spirits and cosmetics, with units being installed at plants producing pasta sauces, pastes, mayonnaise, soft drinks, wines, whisky and deodorants.
The most recent installation has been at the new Glenmorangie whisky bottling plant in Livingston, Scotland, which became operational in October 2010. Chemical engineering consultancy Allen Associates, which designed the new plant, was aware of the unique operating method of the Whirlwind system and the impressive product recovery rates it could achieve, so this project provided the ideal platform to incorporate the technology.
Installation and testing of the Whirlwind system took place during final stages of the plant build with commissioning taking place alongside plant completion.
The Whirlwind system is used to recover across all of the lines in operation from tanker delivery to the bottling line filler. The engineering manager, Chas McEwan, has readily taken on board the new technology, which is used several times daily in various parts of the plant.
Julia Blair, Glenmorangie project engineer, said: “Delivery commitment and testing timeline were both adhered to by Aeolus, and since commissioning and going into full operation we are very pleased with the performance of the Whirlwind system. Through use of the clearing phases we are able to recover near enough, if not all, of the product from the pipe lengths which, as well as minimising waste, also protects the integrity of our products.”
The payback period for the technology is dependent on a key number of variables, including value of product associated with increased recovery levels, costs associated with reduction in water volumes used, and reduction in effluent disposal, let alone cost benefits associated with reduced changeover times.
For a high value product, such as Glenmorangie’s, an increase in recovery rates and minimising waste can be extremely valuable. In contrast, an installation at a soft drinks manufacturer is estimated to be saving between £50 to £100 per use cycle. With 80 use cycles per week, and more than 16,000 in total since installation, this also adds up to significant financial gain.
Aeolus Technologies took over the design through to supply and installation of the Whirlwind technology towards the end of 2009. The company recently moved into new premises in Mobberley, Cheshire, and has re-installed the test rig unit and dummy processing setup to allow trials for potential customer products to recommence, and to add to the data on the technology performance across a range of products previously collated.
Currently, the schedule includes trials for a dairy producer, cosmetics manufacturer and sauce producer.
The company has the benefit of installations being in successful use at a number of companies, so the operation, benefits achievable, and reliability of technology are proven. The trials on the test rig are very much about proving and assessing the performance of the technology across the product range that the potential customer wishes to trial, and for the customer to see and review the levels of recovery and cleanliness that can be achieved using the carefully controlled vortex airflow.
A combination of microbiological swabbing and visual checking is performed to measure cleanliness. Volume of water injected is monitored, and from volume out vs volume in the pipework, product recovery rates are calculated.
The company also measures the length of time for operation through each phase so that, among other measures, it can assess energy consumption for comparison. Of course, trials are on the one hand to show what can be achieved, but more importantly to show what can be achieved consistently.
A similar procedure for checking and validating that results are repeatedly achieved is applied when Whirlwind units are installed at customer sites. Commissioning is very much about ensuring the unit is tested repeatedly across all pipework on which it will be operational and across the product range for which it will be used. This includes testing and validation of controlling software and interface between Whirlwind unit and plant software.
The momentum of interest in the Whirlwind technology is growing healthily, and it is really exciting to be promoting a technology that is “one in the class”.
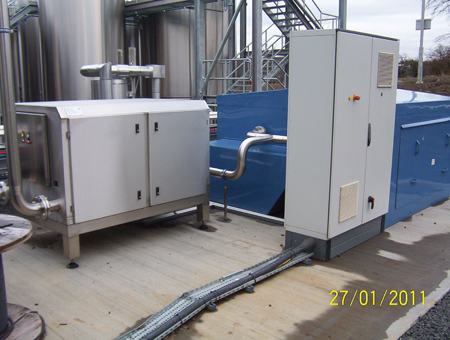
Three sections to the technology – whirlwind unit, blowers and control panel