Start-up company EnXray Limited has developed a proprietary and patented method to deliver ionising radiation for sterilisation that is "on-site & on-demand" for low-volume/high-value products. The technology is based around the ability to generate and deliver low energy X-rays (LEXR, for short). Currently fundraising on Crowdcube, EnXray expects its offering to have a significant impact on how new advanced therapeutic medical products are developed.
Edward Cappabianca, EnXray founder and director, believes future generations of EnXray’s LEXR technology may also provide a valuable means of ensuring that larger manufacturers of medical devices are able to secure the continuity of their manufacturing processes.
Sterilisation is a mission-critical factor in the life sciences and healthcare sectors globally, and yet "often overlooked, or only considered as an afterthought," Cappabianca says. He explains: "This is not that surprising, when one thinks about a new company or a first-time inventor seeking to develop a novel product they hope will save lives; because sterilisation occurs at the end of the manufacturing process, many may consider it part of the product development process in a linear fashion, only once other factors have been considered, designed and locked-down."
For Cappabianca, senior managers in large companies can take the process of terminal sterilisation for granted, because it typically runs very smoothly; one outgoing shipment to be sterilised is effectively matched by a returning shipment from the service provider. "Systems like this work well until there is a problem, which can rapidly escalate, disrupting the supply chain," he says.
Outsourcing services
Sterilisation services outsourcing has grown steadily in lockstep with the life sciences industry. The dynamics behind its growth are multi-faceted and today there are a limited number of large, integrated service providers, many of which operate on a global or super-regional scale.
For EnXray, there is a meaningful segment of the global industry that would benefit from being able to sterilise with ionising radiation using a method that is "on-site & on-demand"
Ionising radiation is one of the two main methods of terminal sterilisation for medical products, with the other being ethylene oxide. In the category of radiation sterilisation, the major method is gamma radiation, while other sources include electron-beam, beta radiation and high energy X-ray (HEXR). These methods are operated on a large-scale centralised processing model. The lead-times can be days or weeks, particularly for smaller companies that do not have the same buying power as larger manufacturing companies. For EnXray, there is a meaningful segment of the global industry that would benefit from being able to sterilise with ionising radiation using a method that is "on-site & on-demand".
"It is not economically viable to simply scale-down a gamma irradiation facility to deal with smaller batches and the dwell-time required for gamma sterilisation does not change materially with the volume of material being processed. The shielding requirements and the hazardous waste disposal issues alone would make onsite gamma sterilisation challenging at best," Cappabianca explains. He points out that as beta rays are also derived from radioactive material, the product handling and safety issues are broadly similar to those of gamma, although the shielding requirements are lower.
The initial set-up costs for electron beam or high energy X-ray sterilisation facilities are also significant, so these methods, Cappabianca says, typically require high throughput volumes to justify their costs.
A new approach
LEXR represent a relatively narrow range of the electromagnetic spectrum from 5-20 kiloelectron volts (keV), higher energy than electron beam, but lower than high energy X-rays (see figure 1).
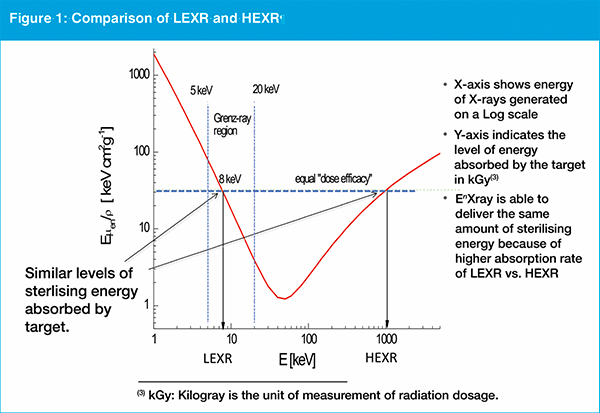
The EnXray founder says LEXRs are more easily shielded compared with other forms of ionising radiation, and therefore could be more safely deployed in a typical manufacturing site. Commensurately, he says, the level of absorption is greater therefore the dose rate to achieve sterilisation on small volumes of products is higher. "LEXR is able to deliver a typical sterilising dosage of radiation to individual products quicker than existing methods, particularly when the time associated with transportation logistics is included," argues Cappabianca.
Most new ideas in the development of novel medical devices, or new advanced therapeutic medical products come from research labs, small companies, or the R&D departments of large organisations. Even when new ideas come from an established company the size of Johnson & Johnson, products are initially made in very small quantities for prototype testing. "The sterilisation of these small batches can pose a problem for large companies, which can look like a start-up company to a typical sterilisation service provider. These small-batch sterilisations would benefit from systems more suited to their requirements," says Cappabianca.
As ISO 11137 governs sterilisation of medical products when using ionising radiation, the use of LEXR is expected to be relatively straightforward. The kilogray dosage delivered has been proven to be equivalent whether the source is gamma, electron-beam or high energy X-ray (see figure 2). "Assuming that kilograys of LEXR have the same level of sterilising efficacy as other established sources of ionising radiation, it should be straightforward for companies to apply ISO 11137 to validate this method alongside other forms of ionising radiation," Cappabianca explains. He says the validation process is expected to be simpler because the way small items can be orientated is more limited compared to the way numerous boxes of products may be packed and loaded onto a pallet.
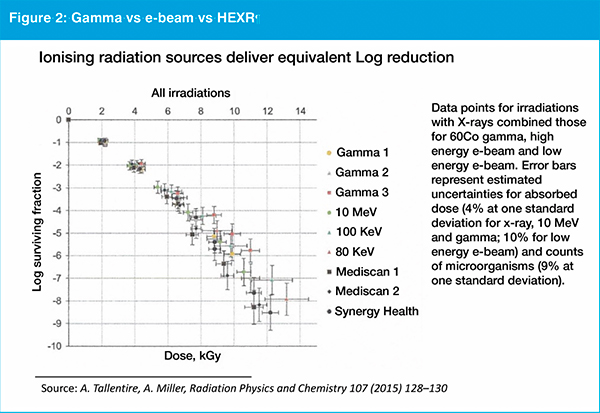
Regulatory update
Another important factor facing the industry today is the introduction of regulations regarding unique device identification (UDI). Since 2013, the US Food and Drug Administration (FDA) has been rolling out regulations for Class I, II and III medical devices to ensure traceability. Similar regulations are being implemented throughout Europe under the EU Medical Device Regulation (MDR) 2017/745 and the In Vitro Diagnostic Medical Device Regulation (IVDR 2017/746). In this context, ExRay belives the ability to sterilise high value medical products in a manner that allows for individual traceability would be more in keeping with the objectives of these regulations.
Significant benefit
EnXray's Cappabianca understands that companies are willing to build redundancy into their supply chain systems by seeking to establish a second service provider for sterilisation. This, he says, is a sensible approach for companies with a large enough production volume to justify having two suppliers but for high-value small volume manufacturers this could be a costly exercise, as service providers would not be willing to hold excess sterilisation processing capacity without some form of payment. If a service provider is the source of the problem, then there would be many different companies all seeking to access a secondary service provider at the same time, severely reducing any available capacity. “Having access to an affordable back-up system that is always and exclusively available is appealing," says Cappabianca.
The ability to sterilise individual medical products efficiently seems to offer a significant benefit to the industry, both in terms of improving the ability to develop and commercialise new products, and providing a suitable method for business continuity and disaster recovery.