Stepping outside the box from a rigid "stick-built-vs-modular" mindset not only opens a world of possibilities for tailoring cleanrooms to a client's unique needs and objectives, but it also makes the panorama of design and product choices a bit more complex. That’s where the experts come in.
Professional guidance can help owners and architects simplify early decision-making by identifying multiple "hybrid" options and virtually trying them on for size. This sets the stage for project success, right from design development and construction all the way through to operation and maintenance.
Every design decision has multiple consequences that impact and are affected by many variables
While both traditional stick-built and modular construction have their respective advantages, PCI’s clients are increasingly opting for a hybrid approach that seamlessly integrates the best of both worlds.
Starting the conversation from a broader perspective multiplies design and construction decisions – there are various paths to a successful outcome – increasing the importance of understanding the practical, operational implications of design and product choices.
Balancing act
Every design decision has multiple consequences that impact and are affected by many variables. Understanding how these individual decisions can impact your long-term operations is critical.
The best-fit solutions arise from the intersection of your project/organisational expertise and the expertise in high-performance cleanroom projects – from their individual components (products) to overall project design, construction, and commissioning. We encourage our clients to base decisions on data, not dated assumptions or marketing-speak.
When it comes to cleanroom design, the question of how to go hybrid has at least as many answers as there are clients and projects
Streamlining your design-decision tree in the face of evolving technology and product/component diversification begins with understanding the feasibility of your basic project assumptions in the context of budgetary considerations, time value, and variable, and location, both the physical project site and your position in the competitive marketplace/landscape. (For example, knowing that you are working with a 13-foot floor-to-floor height might immediately remove a walkable ceiling from consideration.)
An expert, independent project partner like PCI ensures a more efficient, effective decision-making process informed by analysing the cascading impacts of multiple, interdependent variables including:
Costs
- Upfront vs long-term investments and commitments
- Funding sources and constraints
- Cost Analyses and Cost Estimating
- Fixed costs (materials, products, systems) vs variable costs (labor)
- Value Engineering Opportunities (Real-time Pricing)
- Tax implications for capital expenditures (varies state by state)
Time Value and Variables
- Schedules/coordination of trades and deliveries
- Product/material lead times
- Downtime logistics
- Production readiness
Location
- Labor costs
- Proximity to skilled, high-tech workforce
- Site-specific constraints or complications (e.g., limited plenum space)
- Strategic adjacencies (e.g., for suppliers)
- Competitive landscape and local/regional market expectations
Going hybrid
When it comes to cleanroom design, the question of how to go hybrid has at least as many answers as there are clients and projects. Understanding the advantages of modular and stick-built construction and assessing these in the context of your unique requirements – cost, time, location, purpose – can narrow your best-fit options to a handful of design scenarios that variously integrate both types of elements, so that you can be confident in your ultimate design decisions.
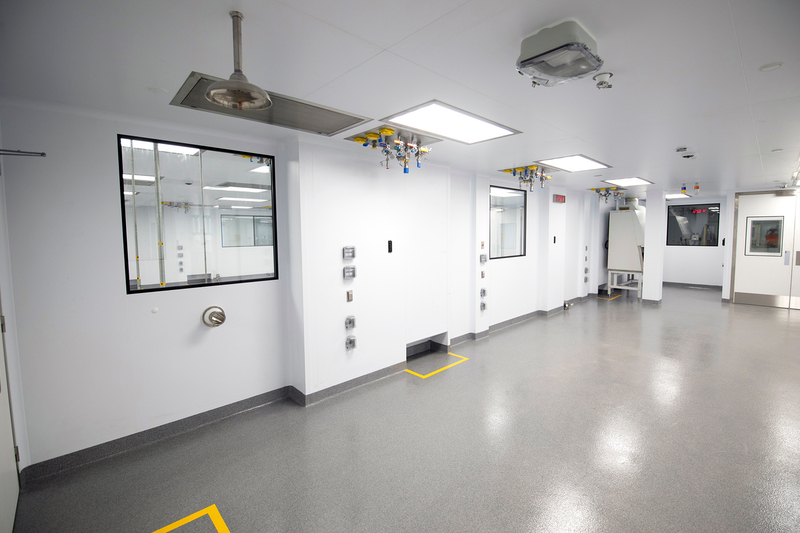
PCI hybrid cleanroom
Advantages of modular
Cleanliness and control are the key pluses of integrating modular components. These products are manufactured of materials that offer no potential for fungus growth and in controlled settings that minimise contamination risks.
Because they are built and inspected offsite, onsite construction requires fewer touches and inspections (e.g., wall panels include UL-rated raceways for electrical), decreasing the potential for contamination, while reducing onsite labor costs and coordination of trades, which consequently reduces liability and insurance costs. Products are FM Global approved.
Because uPVC finishes are more durable, chances are you will need to replace the technology in your cleanroom before your walls wear out
The uPVC finishes of modular components hold up to the most rigorous cleaning protocols and do not deteriorate over time the way epoxy paint over gypsum board does, making it easier and more cost-effective to maintain a pristine, controlled environment.
Because uPVC finishes are more durable, chances are you will need to replace the technology in your cleanroom before your walls wear out. And if you need to expand or alter your space, you can add utilities or a pass-through cabinet with less disruption and dust, avoiding lengthy shutdowns for post-construction clean-up.
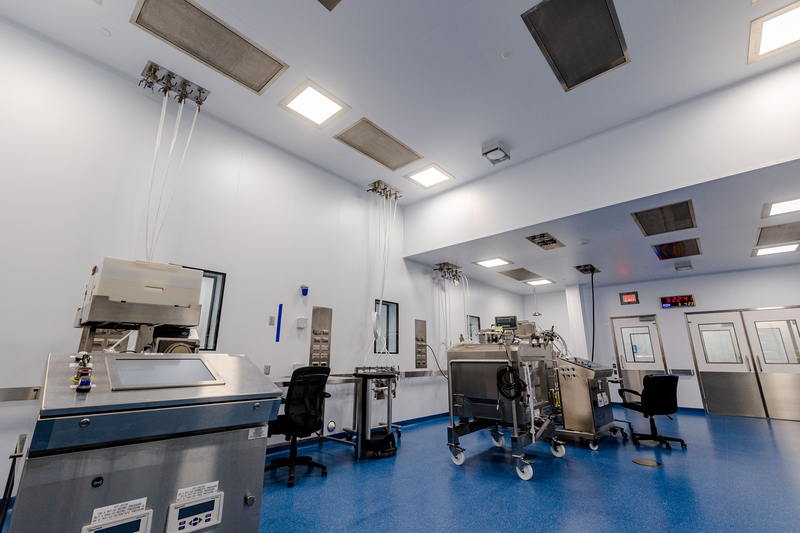
PCI modular cleanroom
Case 1: Pivot Point
A major pharmaceutical firm has elected to replace an existing stick-built traditional facility with new modular construction.
The investment in higher front-end costs makes sense given their long-term time horizon. For the client, realising the long-term operational benefits of modular uPVC finishes was a gamechanger: they had assumed it was normal (i.e., necessary) to constantly be doing maintenance on and replacing epoxy-coated gypsum walls.
As they streamline and update all their facilities and protocols, pivoting to modular will be highly cost-effective and yield substantial advantages.
Advantages of stick-built
The greatest benefits of traditional construction methods derive from flexibility and affordability. Stick- built construction offers increased flexibility for change orders, mechanical utility rough-ins and layouts, routing electrical through metal framing, and addressing unforeseen field conditions, such as existing (structural) columns and drains.
Since not all industries and end purposes require the same ISO classifications, in scenarios where cleanliness is not as critical, stick-built cost-effectively delivers a CNC- grade environment. If you are conducting proof-of-concept studies and anticipate only one-to-two years before scaling up to a larger facility, stick built makes economic sense.
Why invest in more expensive modular components when you are still evolving your processes and protocols? Likewise, if you need a cleanroom in one month, the faster lead time for stick-building materials makes it your go-to option. Stick-built construction has a lower front-end cost depending on local labor rates and materials costs.
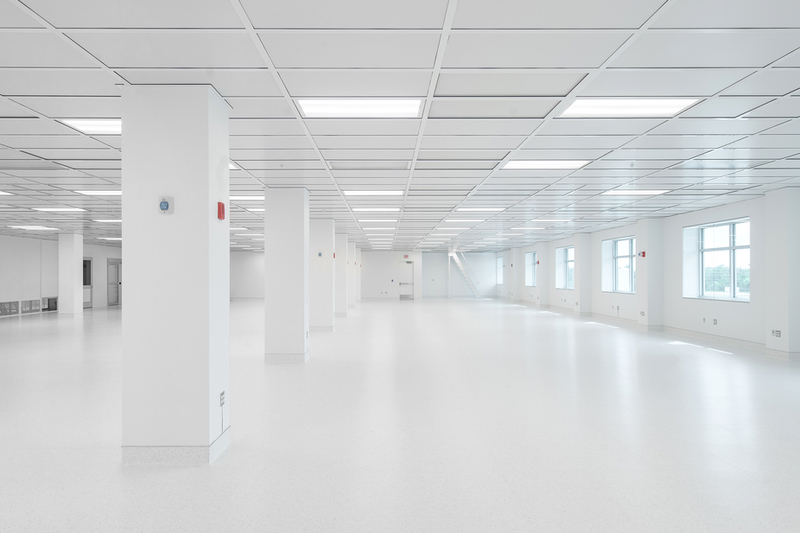
PCI stick-built cleanroom
Case 2: Turn and Burn
Driven by the need to modify a CNC-grade (unclassified) cleanroom during a scheduled three-month shutdown, a leading pharmaceutical company in the Mid-Atlantic lacked the time necessary for pre- ordering modular components. In this case, traditional stick-built construction, utilising a cleanroom grid with epoxy-coated walls, was the best-fit solution to ensure production readiness of a controlled but not classified environment.
Hybrid solutions
Hybrid design and construction maximises the opportunities for tailoring cleanroom projects of all scales to the mission, vision, and circumstances of owners and stakeholders. New-build projects are favoring this kit-of-parts approach that seamlessly combines the best of both worlds.
The visual appeal and visible design consistency of modular, high-tech surfaces over stick-built framing is ideal for developers looking to contract space out for manufacturers who want a leading-edge look. As technology and products advance, hybrid approaches continue to evolve as well.
Hybrid construction often meant drywall with modular liner panels over it; today, it is also commonly considered drywall with a 2-3mm thick cladding system – increased durability at a cost-effective price point.
Case 3: Advancing the Mission
A national research institute chose a hybrid approach – modular walkable ceiling with stick-built, epoxy-painted drywall partition below – to manage costs and maximise flexibility. Relatively low labor costs in the mid-Atlantic market made stick-built construction budget friendly.*
The flexibility of metal framing (with a cavity for routing MEPs) was also advantageous for this design/build project, where the owner did not provide final equipment layouts to the architect during the design phase.
*An important caveat: epoxy paint requires application by highly skilled laborers (improper installation risks defects), and epoxy paint does not hold up to cleaning protocols as well as do uPVC finishes. The cost of maintaining epoxy-painted wall systems could eventually outweigh the upfront savings.
Case 4: Living Lab
Durability of finishes and pressurisation requirements made hybrid design the best option for a vivarium. The project utilises a wire-hung (non-walkable) ceiling with a combination of drywall and quarter-inch panel for greater sealing and durability.
Case 5: Multi-variable Cost Analysis
A hybrid cleanroom design is delivering a cost-effective solution for a small hospital compounding pharmacy project in New England. The project utilises a walkable ceiling with 2-inch panels on existing stick-built walls.
Comparing the costs of modular vs traditional, stick-built construction is complicated by the variability of local labor costs. In the Boston/Cambridge area, high hourly rates make the percentage difference between the two approaches moot, but in regions outside the Northeast, stick builds are less expensive because labor costs are lower (while materials costs are fixed).
Cost comparison
Impact of local labour rates on overall project costs
Mid-Atlantic United States
Northeast United States
*Baseline = Modular Cleanroom System (excluding MEP) with walkable ceiling panels, 2” modular wall panels, cleanroom doors, HEPA terminals, light fixtures, misc. devices.
Multiple paths to high performance
The best design approach is not an absolute but the one that works best for your situation, requirements, and goals. Plotting your own project path – the best-fit combination of features and products – is easier and most cost-effective when you have an experienced partner.
The earlier you add an expert to your team, the greater the value added for your cleanroom project.
A hybrid approach maximises opportunities for customising cleanroom design but also complicates the landscape of design and product choices. Information overload is real, and no one can be an expert in everything.
The best design approach is not an absolute but the one that works best for your situation, requirements, and goals
Independent expertise can help you streamline your project to ensure success from design development and construction through long-term operation. Having the right people asking the right questions when every day counts is a critical investment in successful outcomes.
As a top national specialty contractor, PCI understands the complex landscape and rigorous requirements of leading-edge R&D and manufacturing industries.
Our comprehensive Design Assist Process aligns your project requirements and goals with PCI expertise to empower your decision-making for an efficient, effective process.
We bring deep familiarity with all available products but are not tied to any one manufacturer or product line
If you already have a designer on board, adding PCI as a consultant can still add value to your Owner/Architect/Contractor team.
We bring deep familiarity with all available products but are not tied to any one manufacturer or product line, and we can leverage our longstanding working relationships with providers and suppliers to benefit your project.
About the author: Jason Teets is an Operations Manager at PCI. With extensive experience in cleanroom construction, Jason brings expertise and innovation to every project, ensuring optimal performance and safety.
Top image: Artificial intelligence-generated custom image depicting hybrid, modular, and stick-built cleanrooms side by side, showing their distinct construction methods