Adaptive Use Helps Meet Critical Need
Industries ranging from pharmaceuticals and biotech to nanotechnology are responding to critical market demands by adapting existing structures for use as leading-edge research, development, and manufacturing facilities. While the stringent requirements and complex systems of cleanrooms require exacting design and construction, it is practical and, in some cases, advantageous to construct cleanrooms within existing building stock, such as warehouses, office buildings, spec-built shells, and even older structures.
In areas like New England, where industry-university/healthcare partnerships have transformed the economy, dense urban development can mean fewer opportunities for greenfield construction, and it can be faster (and more cost effective) to repurpose appropriate structures than to build new. In fact, most of my firm’s recent cleanroom projects are in buildings not designed initially to support cleanrooms. Our design expertise, deep experience, and longstanding relationships with partners and suppliers enable us to rapidly deliver custom solutions to rigorous requirements.
The Right Stuff
While every project has needs and goals specific to the client and industry, the top three considerations when selecting a building for a cleanroom conversion come down to location, size, and structural capacity.
Strategic Adjacencies
Proximity – to existing facilities, R&D partners, and/or a skilled, high-tech workforce – makes the location the #1 factor for client/owners. Siting facilities near universities, medical centres, and research/economic development zones allows you to maximise synergies, so your cleanroom can be up and running to meet your ambitious schedule. Locations near airports, ports, and along major thoroughfares – like I-90, I-93, and I-95 – provide easy access for employees, suppliers, and shippers Heavily trafficked corridors outside major urban areas like Boston are punctuated with buildings for sale or lease.
Vertical Fit
Size matters – in multiple dimensions. The right building will measure up not only in gross square footage, but also have a (relatively) open floor plan with few columns, and ample floor-to-floor height.
About 20+ feet floor to floor is optimal. Most cGMP manufacturing cleanrooms need at least 10- to 16- foot ceilings, and the systems infrastructure housed above and/or below ideally requires at least as much height as the cleanroom itself. That said, however, state-of-the-art cleanrooms can be constructed in constrained spaces, as we’ll discuss below.
Load Capacity
Building roofs designed to bear only snow loads lack the structural capacity to support a cleanroom’s walkable ceilings and associated systems (ductwork, lights, HEPA filters, etc.), but there are multiple design strategies for reinforcing structures with additional steel. In fact, a majority of walkable-ceiling-
capacity cleanrooms are not self-supporting, and roughly half of our warehouse conversions involve adding structural steel. Typical approaches include adding wide-flange beams at the roof; inserting a steel mezzanine; constructing a self-supporting steel box within the building; or forgoing the walkable ceiling and routing systems to other accessible areas outside the cleanroom envelope.
Case 1: High-bay Warehouse
78,000 NSF cGMP cleanrooms
A client recently purchased a newly constructed building by a shipping company to be purposed as a trucking terminal. This high-bay warehouse provided minimal supporting steel typically required for a cGMP manufacturing facility. The solution was a strategy that utilises a supplemental steel grid system to support a Life Science cleanroom with a walkable ceiling. Because we were involved from day one in the design process, we were able to advise on proven system solutions and engage the GMP panel manufacturer early to expedite product submittals and release long-lead items sooner for this fast-track project. The original 18,000 NSF project was designed with the potential for a 60,000 NSF expansion that was added in the second phase of work.
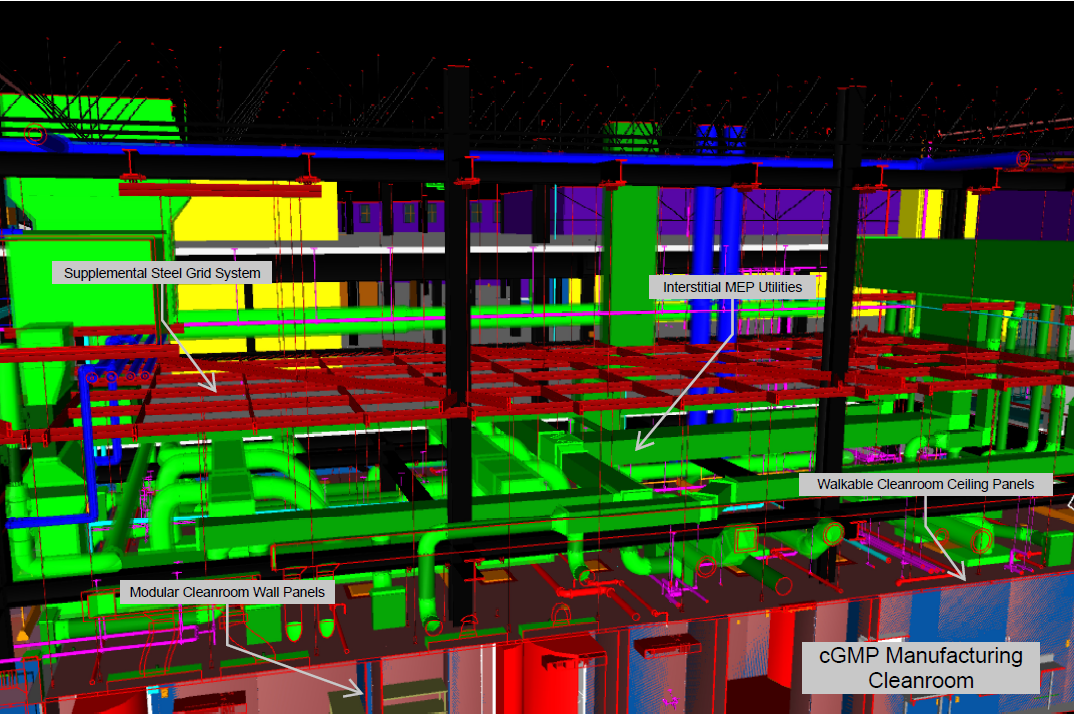
Case 1: BIM model showing approach to insert cleanroom into existing warehouse.
Case 2: Minimal Plenum Space
16,000 NSF cGMP cleanrooms
A conversion was made to a typical office building to house a gene therapy facility. The building selected for this new cGMP manufacturing facility only included 14-feet clear height with two-foot-deep bar joists. Given minimal plenum space, the design utilised open-web steel joists (OWSJs) to span panel points, and the cleanrooms have non-walkable ceilings but give the same appearance as one would find in a modular cleanroom facility. The non-walkable ceiling system can give the same clean features one would expect without the required building interstitial clearances required above ceiling. Because overall space was tight, we worked with our partners and suppliers to phase deliveries, storing materials offsite.
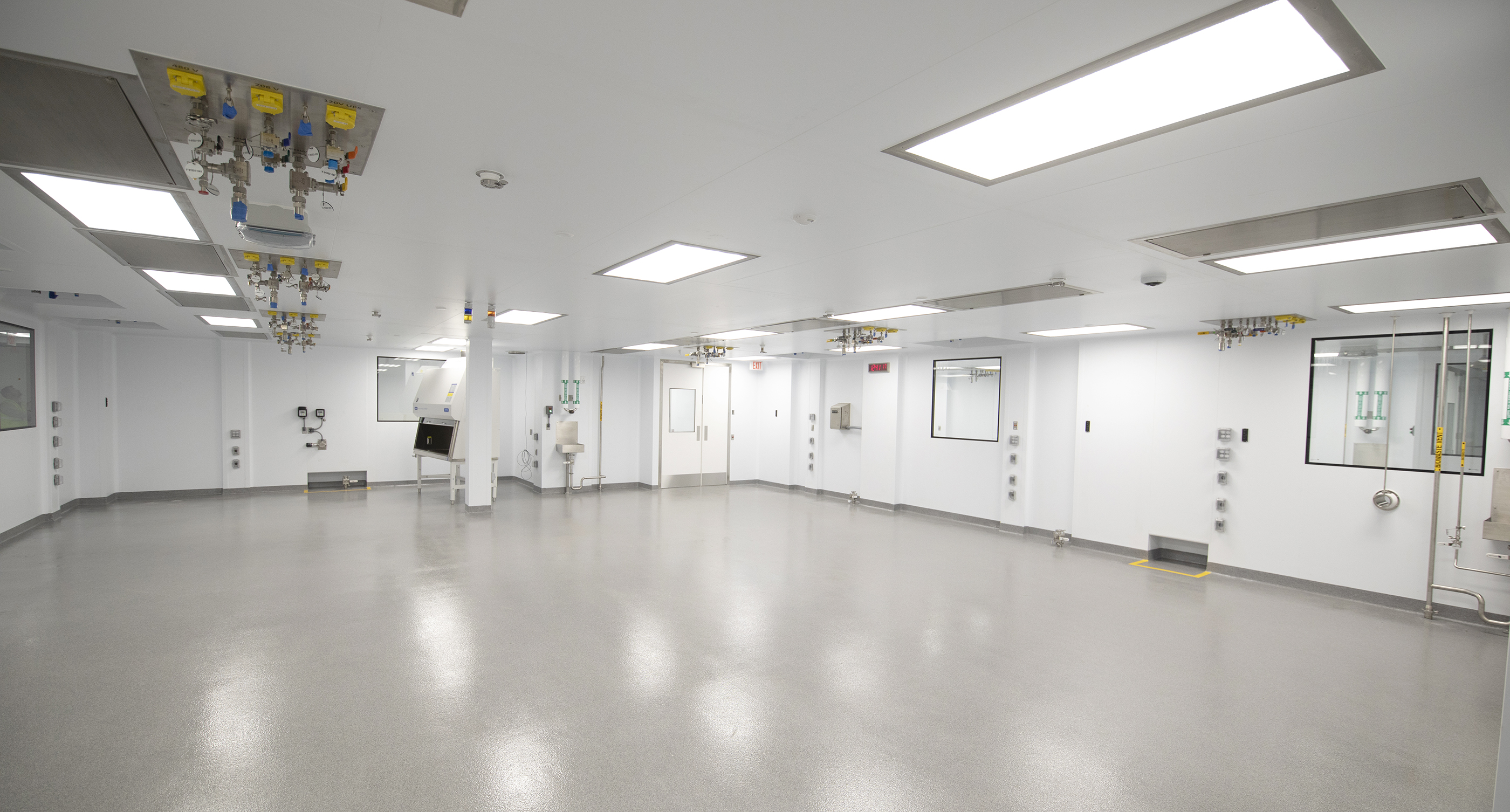
Case 2: Cleanroom inserted into existing tight space building with non-walkable ceiling.
Case 3: Self-supporting
6,000 NSF cGMP cleanroom
In some cases, within a high-bay warehouse facility, adding additional steel to the structure is just simply not an option due to limiting capacities and deflection criteria. To meet this owner’s need for a modular cleanroom facility, a self-supporting walkable ceiling option was a great solution. We assisted in the design as well as furnishing and installing the self-supported modular cleanroom system, doors, wall protection, rapid roll-up doors, and other Division 10 items. During the design phase, when it was determined that the existing steel could not withstand the required loads for a walkable ceiling, our team assisted the architects and owner by directing them to a self-supported modular system that eliminated the need to rely on either existing or supplemental steel. Incorporating the self-support modular system accelerated the overall construction schedule by allowing the MEP trades to complete their work above ceiling before we set foot on the job site.
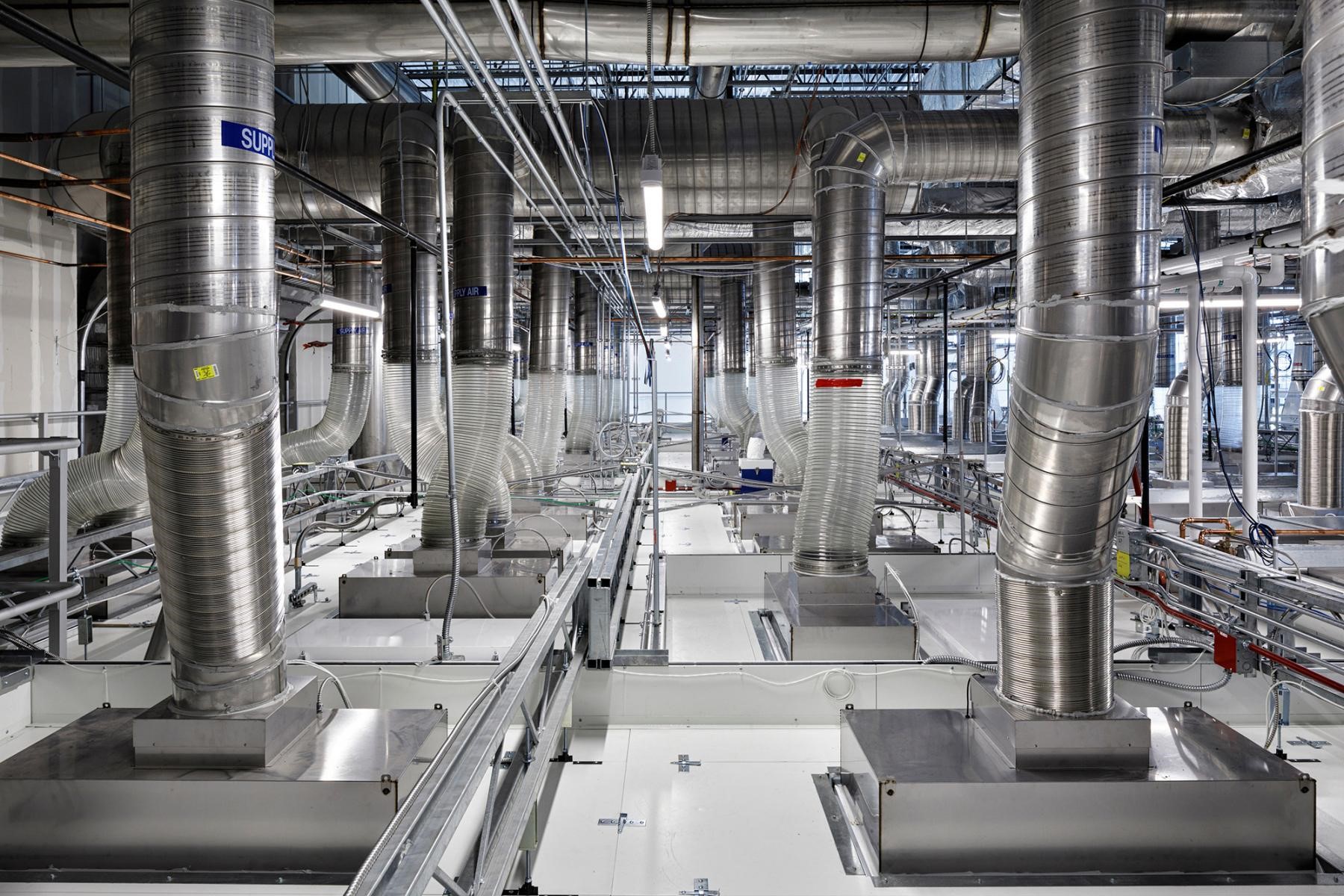
Case 3: Self-supporting modular system for walkable-ceilinged cleanroom
Case 4: Historic Building Stock
700 NSF Cleanroom Lab Space
Research institutes and universities must make the best and highest use of existing buildings in their campus portfolios. For an R-1 research university in the Northeast, we created an ISO-7 cleanroom with a pressure plenum on the fourth level of a historic building. The design utilised a combination of epoxy- coated existing walls and new full-height cleanroom walls. Due to the lack of structural steel above, the ceiling was fully supported by a rod-hung system anchored directly to the concrete slab above. At the client’s request, the new cleanroom walls feature glazing panels that coordinate with existing exterior windows, demonstrating the adaptability of the modular systems. We performed up-front cost engineering for mechanical systems and provided FFUs to save on costs and lead times.
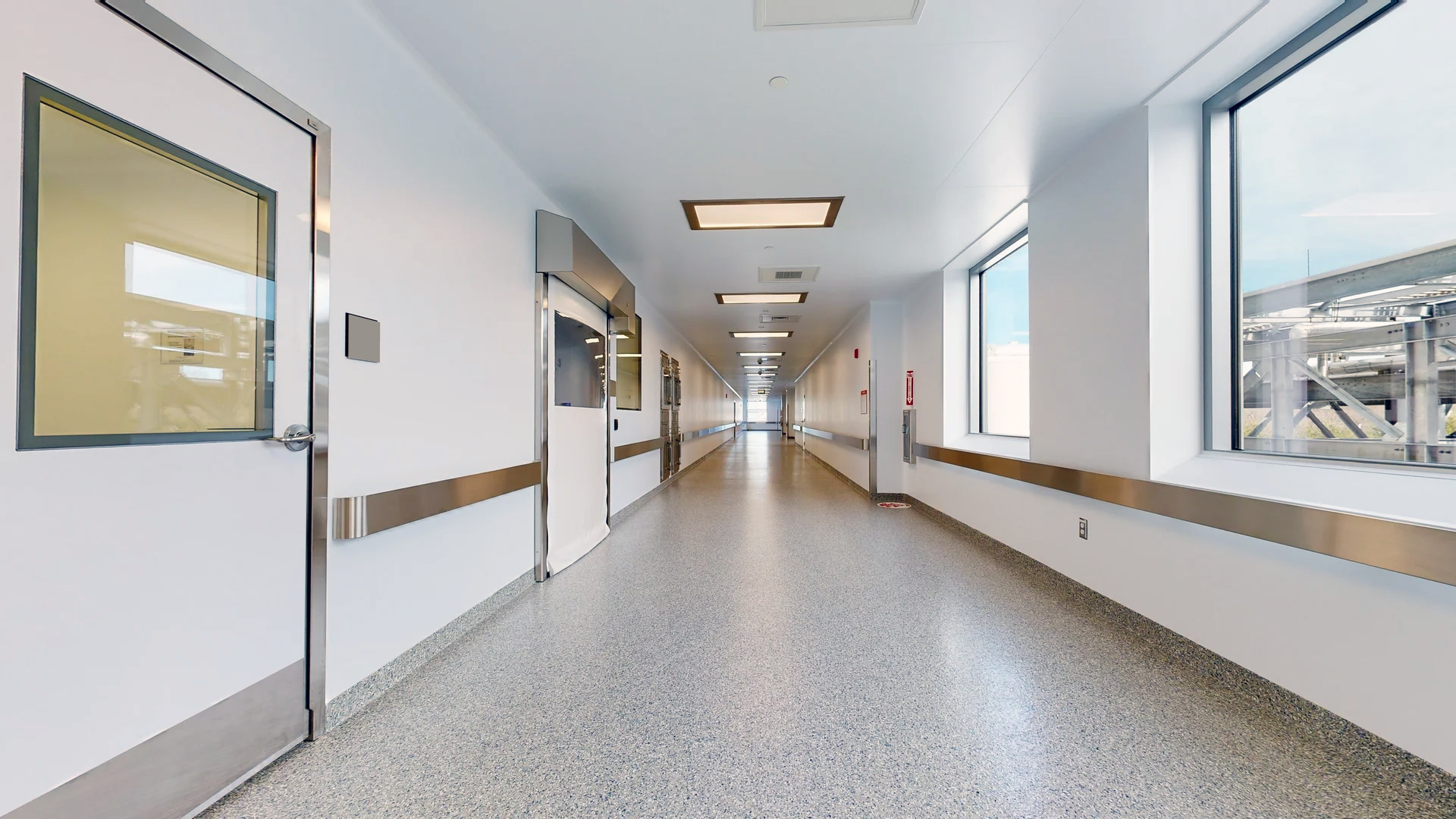
Case 4: Glazing panels that coordinate with existing exterior windows