In part 1 of this review, the use of Pass Through Boxes for the transfer of materials are introduced and the considerations for typical GMP application are explored. In this part, a typical application for a GMP / ATMP cleanroom situation are is discussed.
The design study, proof of concept tests and qualification tests of a ‘continuous flow’ pass-through box in an actual project show it capable of effectively recovering 100:1 within 2 minutes after opening at the less clean side.
Application in autologous ATMP plants
In autologous ATMP plant layouts, many transitions into and out of processing rooms and towards supporting rooms, are necessary. This is caused by the laboratory scale of operations autologous production is characterised by. This means multiple patient materials, many separate items, and culturing fluids for processing, as well as in process control sampling and EM-sampling materials, need to be transferred into the production area. In addition, a substantial flow of the samples to be checked, patients specific products as well as all the waste materials will need to be transferred outbound.
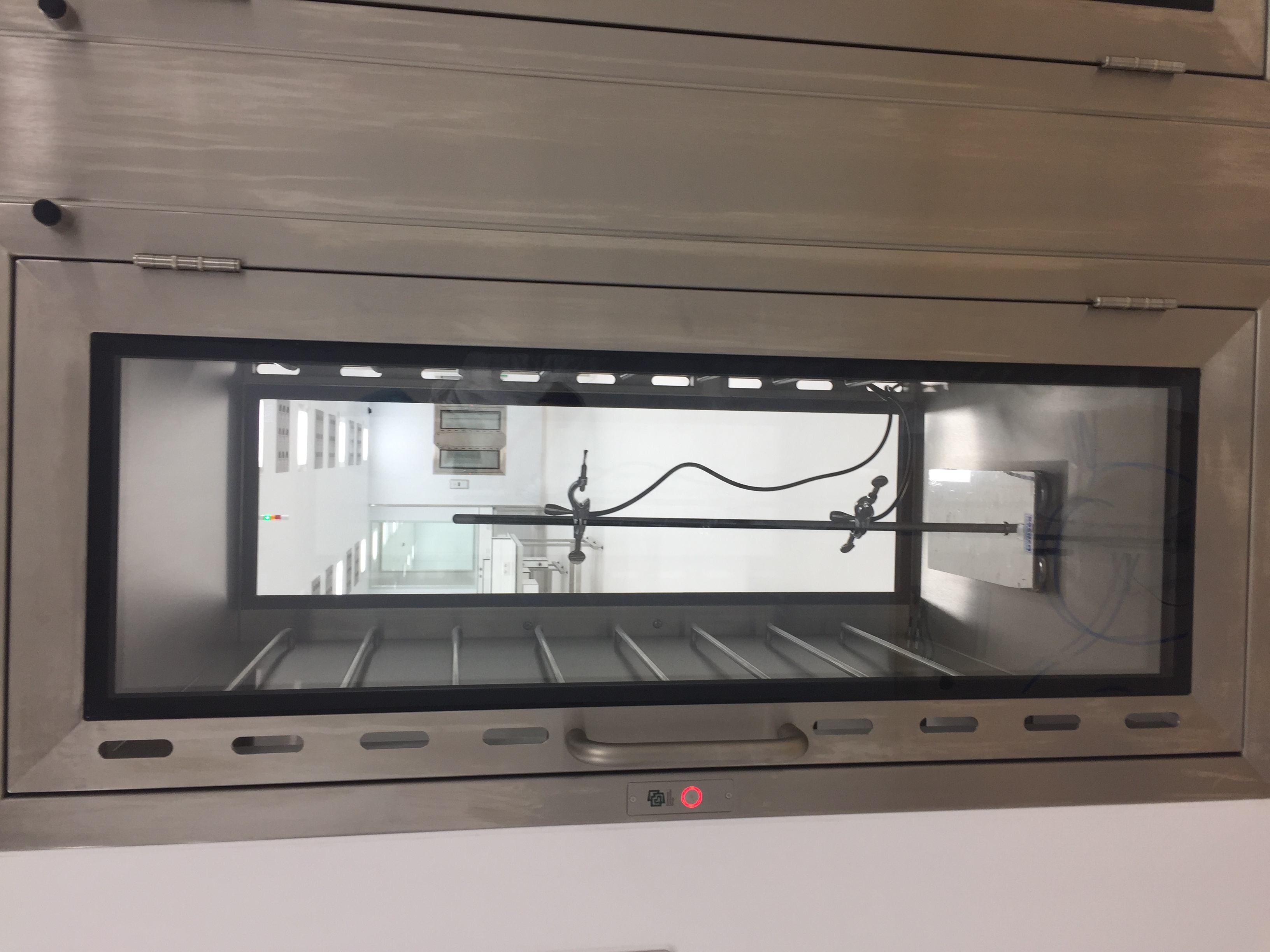
Depending on the production suite, this will require sufficient space to transfer both in and out of the cleanroom. For ease of transportation modular clean baskets can be selected that can be circulated throughout the facility and regularity cleaned/disinfected in the process.
For a facility with multiple production suites and the associated logistics, a large number of PTBs are required, each designed to hold 5 - 7 baskets for transfer. Using active ventilated units with internal fans, HEPA's, controls and monitoring would require significant space, budget, qualification, maintenance and monitoring.
Another approach was therefore evaluated based upon the 'continuous flow' concept that will occur when PTBs are provided with distinct overflow openings only.
This concept is widespread but not well documented. Commonly PTBs can be constructed at specific locations without a door seal, so leakage airflow is provided, given the pressure differential over the PTB. This practice could be further developed given the B-grade (Class 7 operational) production suite and a D+ (ISO Class 8 operational) corridor, based upon the following considerations:
- Air in a Grade B room is actively filtered.
- Environmental conditions in a grade B room are operational qualified and frequently monitored.
- Horizontal flow over the stages of multiple baskets is more effective than vertical flow.
- A controlled pressure difference is maintained from the production suite to the corridor.
- The airflow inside the PTB will be expected to have a recovery rate when doors are closed in range of 2-5 minutes for 100:1 reduction (ISO 14644-3).
- By physical nature, the overflow will increase by √2=1.41 when opening one door with overflow openings increasing the pressure drop over the interlocked closed door by 2x.
- Considering the flow velocity in the openings will be in the range of 3-5 [m/s] at 10-20 [Pa] pressure drop.
Pass-through boxes are the perfect tool to transfer in and out of a cleanroom, but operators must be careful to stay vigilant and not oversimplify the process.
A proof of concept was prepared in plywood to show the effect and determine the airflow at the given overflow design (Figure 1). The test setup consisted of a speed-controlled fan, a flow measurement duct, a connection to a HEPA filtered 'B' section, connected to a mock-up PTB, as well as pressure differential sensors, particle counters and an aerosol generator.
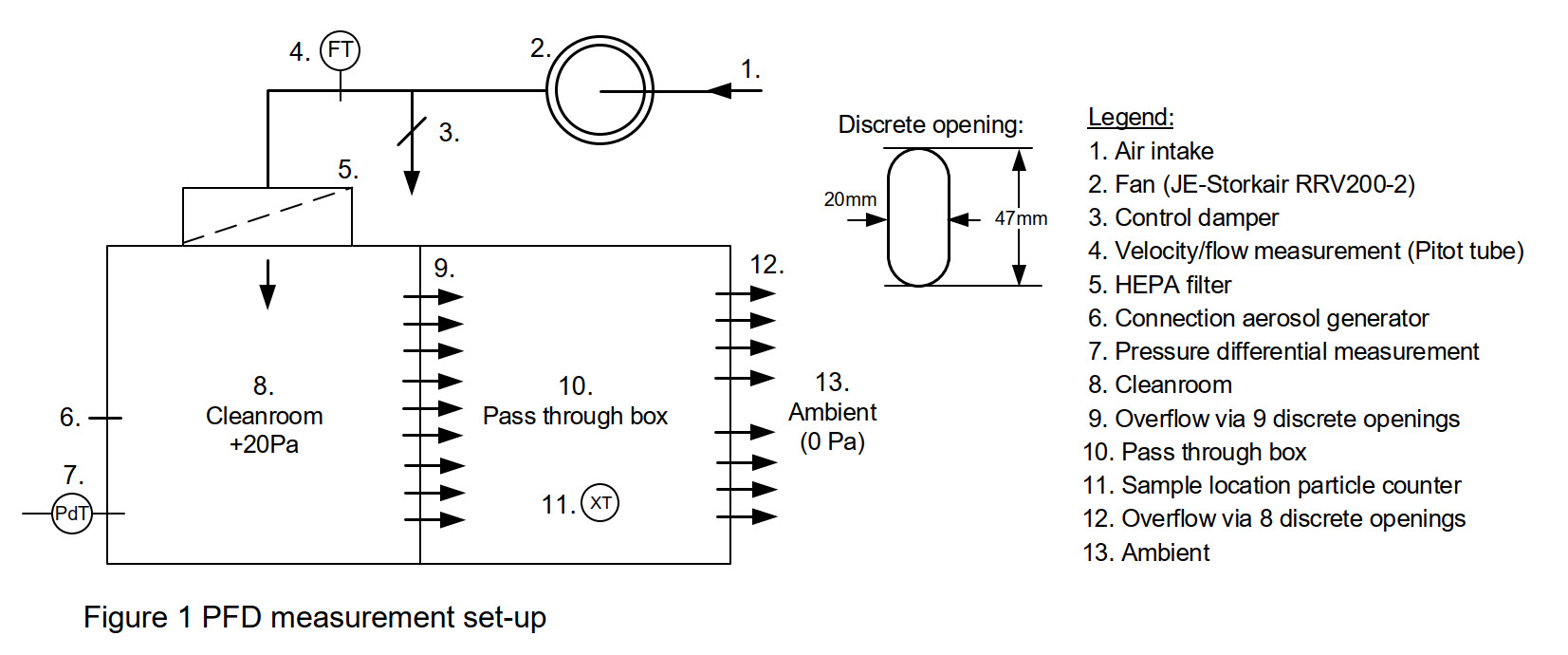
Figure 1: PFD Measurement set-up
All mock-up experiments were performed at a room differential pressure of ΔP=20 ± 2 Pa. At 20Pa the measured continuous flow through the discrete openings of the pass-through box was 115 m3/h. The recovery test was performed by challenging the 'B' compartment to above 100 times the actual concentration. The recovery test clearly showed the 'strength' of the non-unidirectional flow in the pass through box.
The lab scale of autologous production means many transitions
A recovery time of 2 minutes from 100:1 in contamination has been demonstrated where the EU-Annex 1 gives a guidance value of 15-20 minutes between operation to at rest status.
Good mixing ventilation in the pass-through box has been demonstrated by the smoke test. This confirms the expected horizontal flow pattern fitting to the use of staged racks. The designed airflow-pressure cascade is achieved with the size, shape and arrangement of the openings in the doors. After positive evaluation of the 'continuous flow' PTB, the concept and design has been implemented in the project. During the start-up, commissioning and qualification phase a series of tests were performed to verify the concept:
- A smoke visualisation test verified no smoke would move from the inside of the PTB into the B-suite in normal closed conditions.
- The smoke visualisation test also showed that the flow was from the PTB towards the corridor in normal closed conditions.
- The cleanliness inside the PTB was equal to the cleanliness of the B-room from which the 'continuous airflow' was coming.
In an ISO Class 8 operational corridor, a significant number of challenging particles were emitted to simulate the operation. The production room was challenged by personnel inside close to the PTB. The door from the corridor was opened, activities simulated and the door closed.
During the test, the particle concentration in the corridor was measured left and right of the PTB, as well as high and low in the PTB. The concentration in front of the PTB inside of the production suite was also measured. Some results of the test are shown in Figure 2.
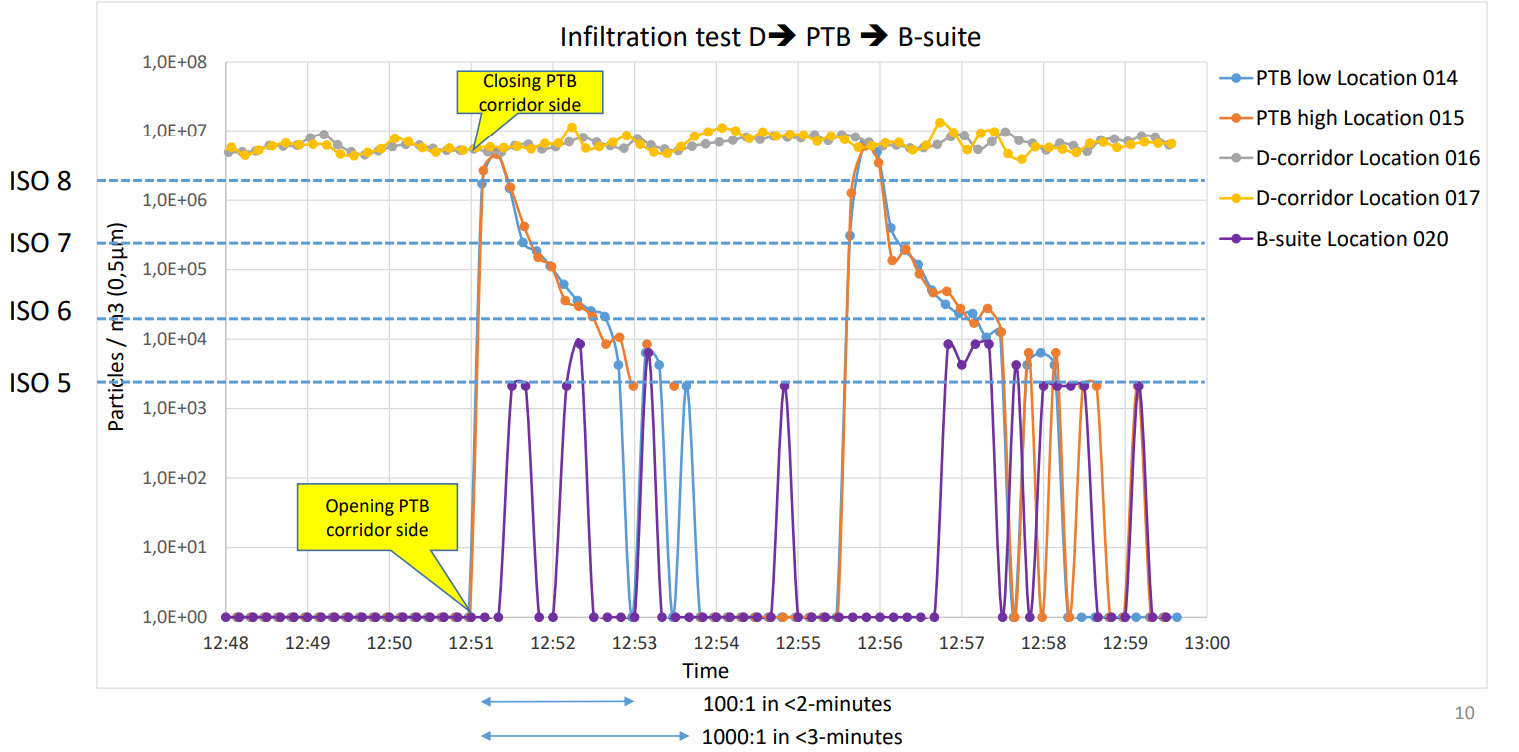
Figure 2: Test result example of infiltration test
Having the corridor well above ISO Class 8 during explicit movement for the test, the particle concentration within the PTB rose to that level, to drop rapidly after closing the door. The concentration in the B-suite was influenced only by the activities of a test person while no infiltration from the PTB was noticed. The peaks in the B-suite reading are the result of the conversion of 0.1 CFM counter data at concentrations. In the infiltration test the recovery time 100:1 showed to be within 2 minutes and for the 1000:1 recovery time within 3 minutes after closing the corridor door.
Evaluation and conclusion
A ‘continues flow’ PTB can perform adequately when properly dimensioned at a controlled pressure difference. When doors are opened and closed the internal air cleanliness can be designed to reduce 100:1 in less than 2 minutes. This is valuable during inbound transfer as the transferred materials can be collected from the cleaner side in short notice without compromising the cleanliness conditions.
This test did not evaluate surface cleanliness of the transferred materials as that is governed by unwrapping, uncovering and/or wiping/cleaning action but as a whole, the 'continuous flow' PTB can perform adequately when properly dimensioned at a controlled pressure difference.