When it comes to cleanroom construction, every detail matters. CREST’s role as architectural cleanroom envelope contractor sees the design of ceilings with walk-on capabilities bear pivotal importance on the direct impact of the functionality and safety of such highly controlled environments.
An often overlooked but critical component, CREST delve into why walk-on ceilings are such a significant element of cleanroom envelope design and the meticulous process involved in creating solutions that combine aesthetics and practicality.
What is a walk-on ceiling?
A walk-on ceiling is a fully tested and independently supported structure, with the capability of supporting itself, along with a concentrated load, without using the cleanroom’s walls at any point.
To qualify as such, it must follow ceiling manufacturers’ guidelines on relative loading capabilities in conformance to BS EN 13964 standards. Any cleanroom ceilings that do not stringently follow the mentioned guidelines cannot be warranted to allow for any future walk-on access.
Ensuring that cleanroom walk-on ceilings are fit for purpose in this way remains inherent to CREST’s role as architectural cleanroom envelope contractor for major cleanroom build contracts across the pharmaceutical industry in the UK.
Construction phase design complexities
A ceiling’s walk-on capabilities don’t come into play only when the cleanroom is fully operational. During the construction phase, it is imperative that the ceiling is not overloaded while services are being installed.
It’s CREST’s role to liaise closely during programming to ensure that as many services as possible are installed above the ceiling level and independently supported themselves, limiting the need for potential overloading while operatives conduct the M&E and commissioning phases.
Why walk-on capabilities matter
The sheer volume of mechanical, electrical, and filtration equipment needed for a cleanroom’s operation is incomparable to any other internal structure found in a pharmaceutical manufacturing environment. This, alongside ducting, hatches and lighting, is usually routed above the cleanroom ceiling.
For regular maintenance and inspection work to take place to keep the equipment in good working order, access to this void is a necessity. However, the challenge lies in facilitating this without compromising health and safety standards. This is where walk-on capabilities of cleanroom ceilings come into play.
CREST’s Senior Design Manager, Bob Stevenson, is responsible for the planning and design of walk-on ceilings.
“The design and technical complexity of walk-on ceilings in cleanrooms is often overlooked and undervalued in the early stages of design. During my seven years with CREST, it continues to be my responsibility to ensure that the cleanroom ceiling layout, including suspension placements and the system used, is fit for purpose for clients to authorise walk-on access in line with health and safety guidance and national building regulations”.
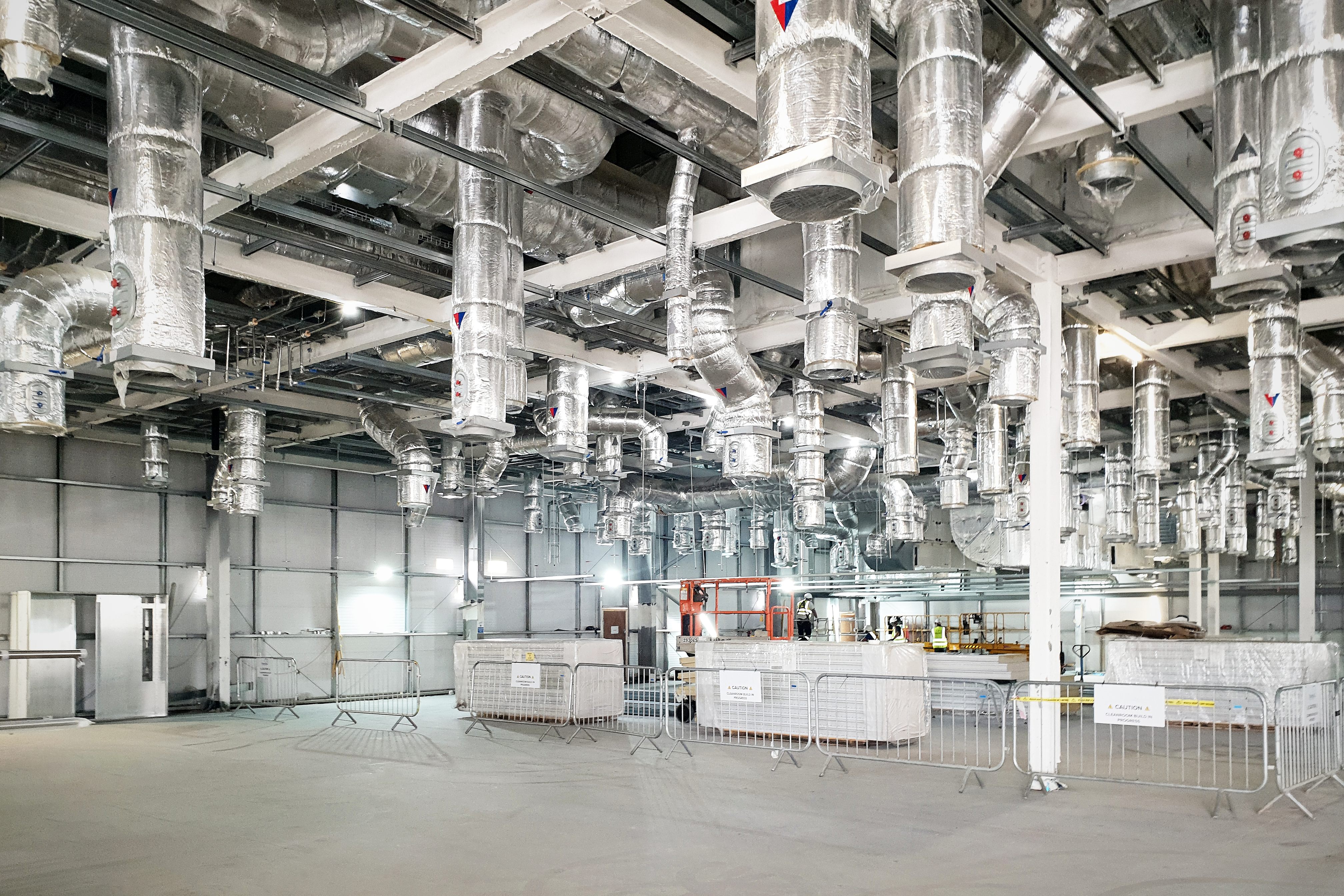
Early integration & 3D design for successful new-build contracts
For all new-build cleanroom contracts, Bob stresses that the successful integration of walk-on ceilings is having an early and in-depth involvement with the appointed design team. Through participation in collaborative design meetings, getting a good understanding of a project’s scope and other contractors’ responsibilities within the turnkey package, the team was put in good stead to eliminate construction issues and delays in the design phase.
Sharing knowledge and working closely with a project’s appointed M&E contractor at the first concept stage allows both parties to mitigate potential clashes of equipment locations within the walk-on ceiling design itself, thus streamlining the transition from design to installation.
“One of the many benefits of designing and coordinating all projects through our 3D modelling programme is that it makes clash detection so much easier.” Bob continues. “This means that potential issues can be rectified proactively throughout the design stage rather than impacting the project at the point of installation and thus generating unnecessary costs and programme delays.”
Monitoring & Upgrading Existing Cleanroom Structures
When looking at existing pharmaceutical cleanrooms, monitoring the ceilings’ walk-on capabilities becomes even more crucial over time.
It remains the cleanroom occupier’s responsibility to ensure that routine inspections of the walk-on ceiling are carried out to look for damage or general wear-and-tear. The amount of monthly traffic on the ceiling in question would determine suitable inspection intervals.
“If a cleanroom facility manager is unsure on whether the room has walk-on capabilities that are fit-for-purpose, my advice would be to seek clarity before authorising any access. It’s best not to make assumptions.” Bob advises.
However, at the point that any changes are made to HVAC or M&E equipment within an existing cleanroom structure, the ceiling’s walk-on capabilities must be reassessed for any resulting impact.
This was a key focus for Bob and the team when working with a pharmaceutical manufacturer and engineering consultancy on the South Coast recently, as upgrades were due to take place to the cleanroom’s HVAC specification.
CREST’s Site Manager, John Barrie, headed up the works, conducting an on-site assessment and managing all eventual remedial actions required before equipment upgrades could safely be implemented. This allowed for the reconfiguration of internal walls below while still maintaining a full walk-on ceiling that enabled works to be undertaken above concurrently.
Structural analysis & planning: load suitability
Gaining an understanding of the amount of load due to be housed on the ceiling is where Bob can start to produce a suitable design layout. Taking account of the building’s existing structure and steel locations is key in identifying suspension points to lay the foundation of the ceiling support.
From here, panel spans can be calculated, and, in line with manufacturers’ guidelines, then be worked out cohesively with the necessary penetrations and openings that form part of the specification, meanwhile ensuring that structural integrity is accommodated to adhere to the walk-on capabilities.
As an independent cleanroom envelope contractor with experience and expertise on side, the team can select the perfect cleanroom ceiling system that will suit the spans and penetrations to provide a walk-on ceiling which has capabilities of 0.9kN to 2.5kN.
Bob acknowledges that it’s a marathon not a sprint when it comes to finalising these details with the parties involved in a project. CREST’s integrated 3D modelling helps speed up the change process as well as delivering incredibly accurate designs; “a design may change multiple times as load variations and penetrations are revised during planning, but it’s always better that this is done then, rather than impacting the programme once on site.”
Functionality vs Aesthetics vs Buildability: getting the balance right
Bob recognises that this is a delicate balancing act that he faces for most pharmaceutical cleanroom projects.
“The walk-on practicalities of the ceiling are, of course, my top priority during the design phase, but I do understand the need for a cleanroom to be aesthetically pleasing from below,” Bob states. “The advantage of 3D modelling is that it gives me the ability to look at the design from all viewpoints and I can make sensible adjustments or suggestions from there.”
While functionality and aesthetics are important, CREST’s unique role as cleanroom envelope contractor means that challenges to buildability need to be put forward at the earliest opportunity. This can often be where additional coordination is necessary for installing suspension drops before or after services are integrated in line with the available access.
“Again, our use of 3D models allows us to identify such matters at design, rather than it impacting the overall construction programme.” Bob summarises.
A careful approach to design & installation wins
Bob and the rest of the team take particular care and attention to the design and installation of cleanroom walk-on ceilings, a critical component of the envelope that must be fit for purpose.
Over the years, the team have learnt the advantages of engaging with all contractors for early cleanroom design collaboration, the value of 3D modelling and a wealth of buildability expertise to improve on-site safety, reduce lead times and installation durations, while achieving the right aesthetic and performance specification.
As an architectural cleanroom envelope contractor, CREST continues to successfully work with many pharmaceutical manufacturers as part of new-build, refurbishment, and extension projects across the UK.