A few years ago, US-based Nortek Air Solutions CleanSpace took a look at the offerings in the cleanroom sector and saw a gap in the market that they could fill. Time passed, and then at the very end of 2023, the company launched its Flex-Trak Ceiling Grid.
Zareer Cursetjee, the Director of Engineering for Research and Development at Nortek, was one of the key voices on this development project. Cursetjee has a long history with the design and build of cleanrooms, having worked in the sector for more than 25 years.
The controlled environment engineering expert joined a company called CleanPak back in 1995. Now if this name sounds familiar, it is because CleanPak has been a brand within Nortek, since 2006.
In many instances, I’m working with direct customer feedback and am not only part of finding the solution but ensuring a successful implementation on site and beyond
It is this acquisition of Cleanpak that began Cursetjee’s almost decade-long connection with Nortek, which would culminate in him being a Director today.
The launch of the company’s new ceiling grid product is right in Cursetjee’s wheelhouse from his time at CleanPak. “[At CleanPak] I helped develop cleanroom-specific products on both the air handling and ceiling grid side,” he says. “We launched several products tailored at moving the needle on fan/motor reliability and rapid buildouts of ceiling systems.”
This launch is bridging the gap between stick-built and modular solutions, and as the whole industry is embracing modular in more ways than ever, these solutions can be key to successful integration.
A successful launch: more than meets the eye
Nowadays, the Cursetjee’s job mostly falls into two main functions. The first is leading a team that customises cleanroom solutions for clients’ needs. “A number of our clients have very specific needs, and we try to react quickly to find solutions in our product space to meet them, while continuing to innovate the industry,” he explains.
The second is new product development. This is Cursetjee’s favourite part of his job. “I appreciate that I have the opportunity to develop solutions that meet the challenges and needs that our customers have,” he says. "In many instances, I’m working with direct customer feedback and am not only part of finding the solution but ensuring a successful implementation on site and beyond.”
Nortek’s new Flex-Trak Ceiling Grid is its most recent launch, but it was not developed overnight and was, in fact, years in the making, and Cursetjee has been a guiding force the entire time.
“This is a product solution that we have been exploring for a couple of years and as we heard the challenges that matter most to the industry, we saw an opportunity to offer something unique in the industry,” he says.
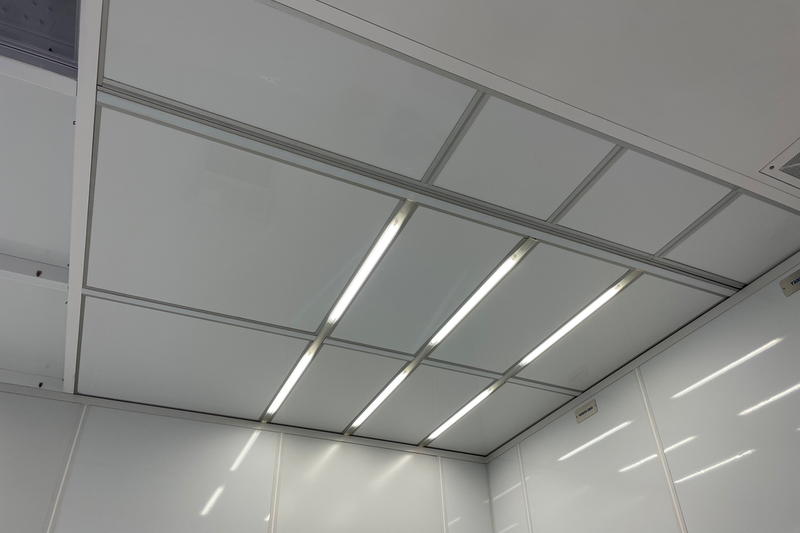
Modular Flush Ceiling with Integrated Lighting
The Director talks about the rapid growth and demand for cleanrooms that he has seen in recent years, exacerbated by a pandemic, and how that has influenced the exact driving forces behind cleanroom design.
“We are seeing more remodels of existing buildings to transition them into cleanrooms, creating a need for flexible solutions to work around existing structures,” he explains.
“This is the foundation for building Flex-Trak, bringing the flexibility to work around existing components while also being able to provide a modular solution.”
Product development for the Flex-Trak took into account lots of feedback from the field from customers and constructors on stick-built cleanrooms, which pointed out some very specific challenges with this type of build.
While addressing this feedback, Cursetjee was also keen to offer a vendor who could provide any grid solution, from modular pre-built at the factory to onsite assembly grids.
"As a result, some key areas of focus became more efficient assembly methods and labour savings all within a robust structural design,” he recalls.
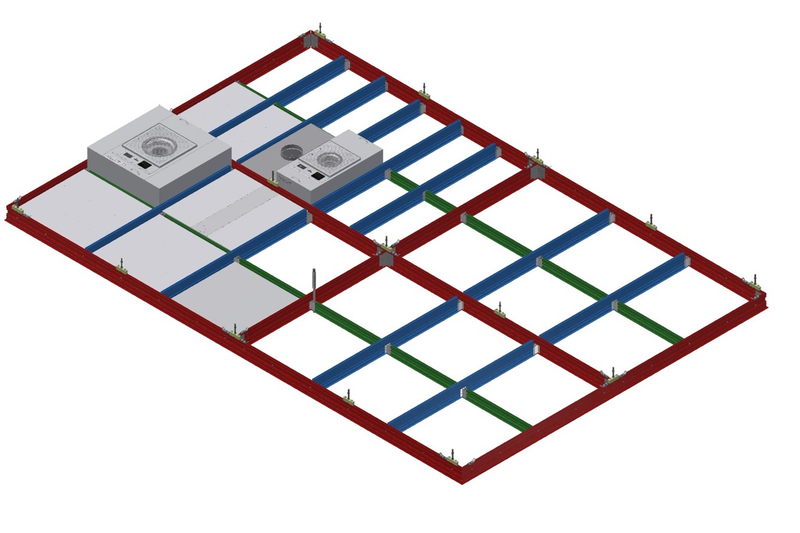
Flex-Trak Hybrid
A ceiling grid solution for 2023
Cursetjee reinforces that labour savings are even more important, as “many areas of the US suffer from labour shortage, especially in construction”.
So with efficient assembly and robust design at the forefront, the Flex-Trak stick-built solution was designed to require fewer hangers to install compared to competitor products, providing a quicker, less labour-intensive installation.
To do this, the company engineered the hangers with wider spacing, allowing servicers to move around more easily for any needed maintenance.
This minimised design is a really interesting innovation, and Cursetjee explains that the reduced hangers and seismic bracing above the ceiling also provide more clear space for accessing HVAC and lighting components in the ceiling.
The Flex-Trak system comes in a few “flavours” of true stick-built, Cursetjee jokes. He lays out there are a few options depending on the required solution.
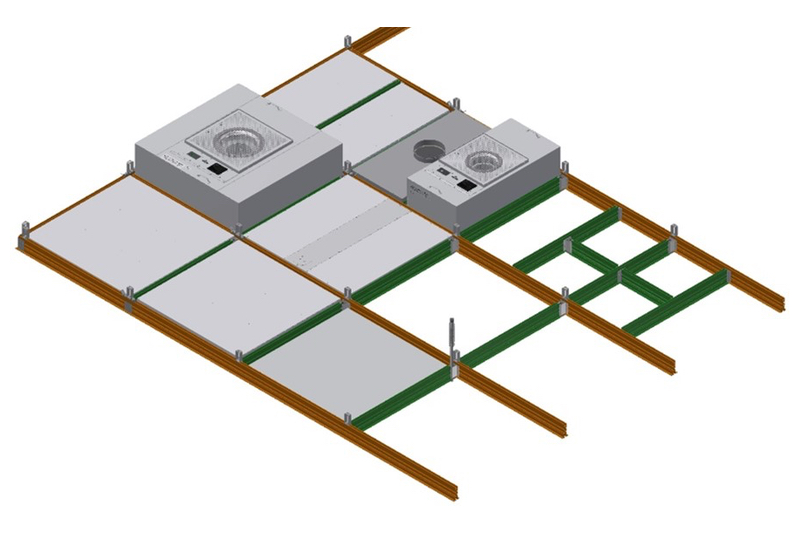
Flex-Trak image
One where all parts are bulk packaged for assembly in the field in the air, a hybrid flatpack option where the parts are bulk packaged for field assembly on the ground as modules that can be lifted into place, or a hybrid modular option where the modules come pre-assembled from the factory.
“The profiles for each of these grids have common features and methods of attaching cross-sticks, ports and hanging above and below the grids,” he explains. “All the grid sticks that make up the hybrid modular grid are bolted together, thus allowing for easy retrofit of the ceiling system at a future date.”
A walkable ceiling is key for maintenance and Cursetjee explains that the Flex-Trak system is designed to have robust cross-stick connections to transfer vertical and seismic loads across a field of members without needing double hangers.
“The stick-built version is a linear and cross system where you can hang on a 4 x 4 foot or a 4 x 6 hanging array depending on the load requirements. The hybrid grids hang on an 8 x 6 foot hanging array which needs 1/3 the number of hangers compared to a 4 x 4 foot hanging system. These features minimise the number of hangers required.”
Who cares?
Looking at all these changes, Nortek has addressed both application and execution in their new design. But what are the consumers saying thus far?
Cursetjee says he has seen a lot of enthusiasm from his clients for the new solution. However, the demand for specific solutions can be highly sector dependent.
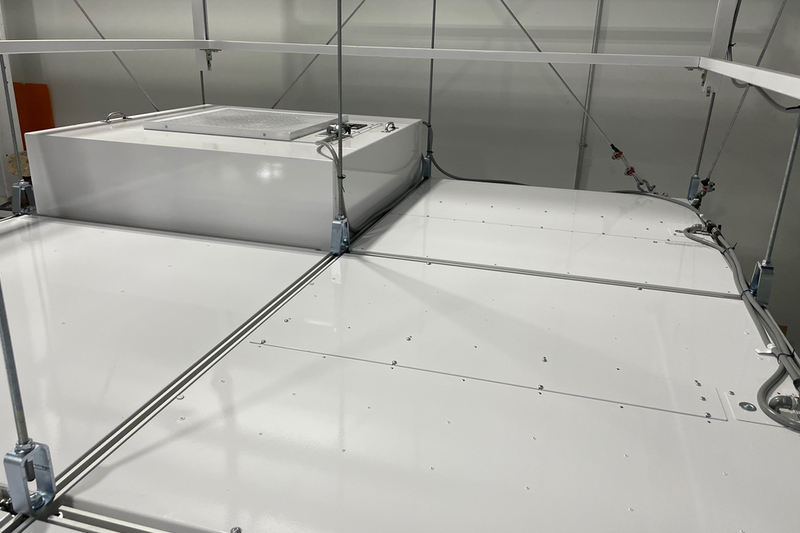
T Grid Stick-Built Assy Walkable Topside with 4x4
“For the semiconductor sector, the biggest factors are availability of skilled labour and timelines,” he says. “Based on these two factors, we see semiconductor clients leveraging both modular and stick-built to best fit their project and scope.
Compared with the life sciences sector, we see a stronger usage of modular grids because of the cGMP Grade A requirements and the need for 100% filter coverage with maintaining particle filtering integrity with filter changeouts.”
At the end of the day, creating a new product takes a lot of work, and this work must have solid motivations to give it the momentum to reach the finish line. The Director is only too familiar with this.
“From clients to consulting engineers, there are several people who have pushed for innovation in the industry and invited me to collaborate on solutions,” Cursetjee looks back fondly.
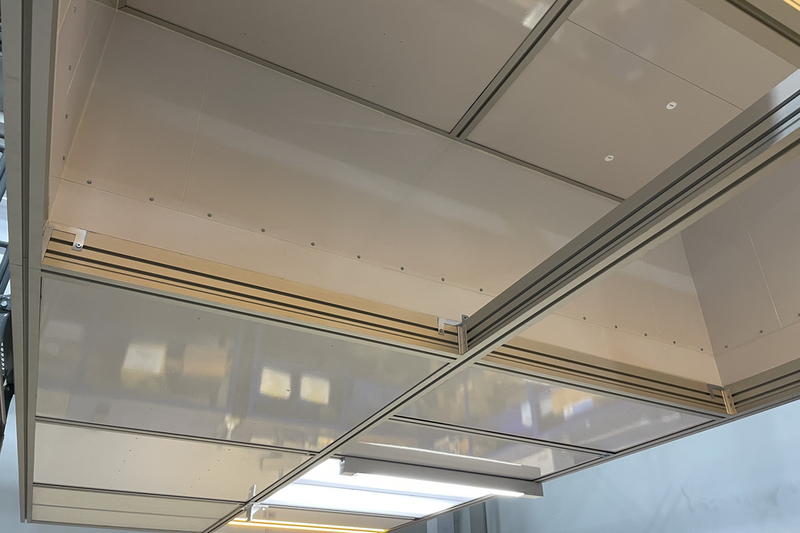
T Grid Stick-Built Assy with Amber_LED_Track Lighting examples
"It’s those opportunities to think outside of the box and identify a new solution that in many ways has shaped my career.”
Are these trends here to stay?
Look at the trends that pushed the Flex-Trak into existence, it is Cursetjee’s opinion that the demand for rapid installation is here to stay, and he has also seen no significant decrease in the labour shortages country-wide.
So this is where their focus as a company remains, on prefabricated solutions for minimised field labour while allowing for flexibility in the grid design for future retrofits.
For the future, a trend that Cursetjee is excited to see play out is the opportunities around smart controls of lighting and air movement. “The products in the market today aren’t cost effective or may not achieve the fullest potential,” he enthuses.
Many areas of the US suffer from labour shortage, especially in construction
“[I expect] we will continue to see centralised control stations, automation, and more settings that allow cleanrooms to be run with more efficiency].”
Innovations in cleanroom construction are a small cog in a machine that pushes a whole host of sectors forward. “We interact with all engineering disciplines in our daily activities and the ability and desire to learn and grow professionally requires you to understand how to interact with all disciplines—structural, mechanical, electrical and architectural,” the cleanroom veteran says, emphasising the importance of innovation to face the challenges of the industry.
So whether it is for ceilings or lighting, efficiency and reduced labour needs will push not only the cleanroom sector forward, but all that rely on it. The longtime cleanroom expert says he is excited to wait and see what other innovations may crop up.