A Quick Who’s Who.
Let’s chat about GAMP.
It’s actually not as complicated as it might sound at first. Think of GAMP as your friendly neighborhood guide to making sure medicines are top-notch and safe for everyone. GAMP stands for Good Automated Manufacturing Practice. It’s like a rulebook created by a group of pharmaceutical experts who want to make sure that when we use computers and machines to make medicines, everything goes smoothly and safely.
The Heart of GAMP
At its core, GAMP believes in a simple but powerful idea: you can’t just check if a medicine is good at the end. Instead, you need to make sure every step of making that medicine is spot-on. It’s like baking a cake – you can’t just taste it at the end and hope it’s good. You need to use the right ingredients, mix them properly, and bake at the right temperature.
What does GAMP cover?
GAMP looks at everything that goes into making medicines:
- The ingredients (raw materials)
- The kitchen (facility)
- The tools (equipment)
- The chefs (staff) – making sure they’re well-trained, follow good hygiene practices, and follow the recipes
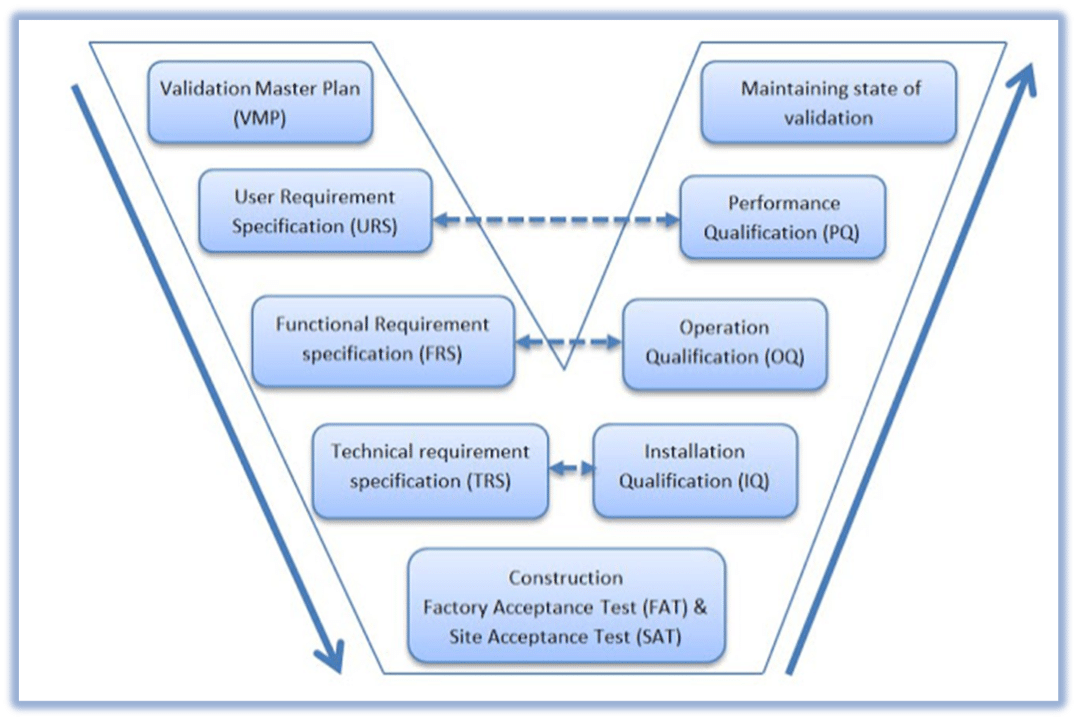
GAMP uses something called the “V” model when it comes to setting up and checking computer systems for making medicines. It’s the roadmap that helps make sure everything is working correctly from start to finish.
Remember, GAMP isn’t about making things complicated. It’s all about making sure the medicines we take are safe, do what they’re supposed to do, and have repeatable efficacy from the manufacturing process. It’s like having a really thorough friend who always double-checks everything – and when it comes to our health, that’s exactly what we want!
On a side note, we just launched a new eBook on Real-Time Monitor Systems. There’s an entire section on the GAMP V model. You should sign up and download a copy if you haven’t read it yet.
So, What About the Big Three: GMP, GAMP5, and 21CFR11?
Think of these as the three musketeers of pharmaceutical quality control. They’re always working together to make sure the medicines we take are safe and effective.
- GMP (Good Manufacturing Practice): The basic rulebook for making quality sterile products.
- GAMP5 (Good Automated Manufacturing Practice, version 5): The tech-savvy cousin, focusing on computer systems in pharma. This latest version of GAMP emphasizes risk management.
- 21CFR11: The strict record-keeper, ensuring all electronic records, data, and signatures are trustworthy, original, and have data integrity built into them. (ALCOA+ is a great guide to follow.)
These guidelines are like living documents (GAMP5 is followed as a living set of documents) – they’re always evolving to keep up with new technologies and challenges in the pharma world.
The Star of the Show: Environmental Monitoring System (EMS)
An EMS is like the superhero of pharmaceutical manufacturing. It’s constantly on guard, making sure the environment where medicines are made is squeaky clean and just right. It’s the key to meeting all those fancy requirements we talked about earlier.
The EMS Journey: From Idea to Reality
Creating an EMS isn’t just about buying some equipment and calling it a day. It’s a whole journey:
- Planning: Dreaming up the perfect system
- Design: Drawing the blueprints
- Procurement: Shopping for the best tools
- Implementation: Putting it all together
- Validation: Making sure it works as planned
- Performance: Keeping it running smoothly
- Maintenance: Regular check-ups and tune-ups
Each step is super important and needs careful attention. It’s like building a house – you want a solid foundation before you start decorating!
The Secret Sauce: Risk Assessment and User Requirements
Here’s a pro tip: start with a really good plan. Do a risk assessment (think of it as a “what could go wrong?” brainstorm and how to mitigate those issues) and use that to create your User Requirements Specification (URS). This is like your wish list for the perfect EMS. Getting this right from the start can save you a ton of headaches later on.
Here’s a recent webinar that our Applications Director, Jason Kelly, did on using a risk assessment to build a system focusing on data integrity.
Testing, Testing, 1-2-3
Once you’ve built your EMS, you need to put it through its paces. A thorough testing and validation process is crucial. It’s like taking your car for a test drive before a long road trip – you want to make sure everything’s working perfectly.
Choosing Your Partner
Picking the right vendor for your EMS is super important. You want someone who’s been around the block a few times (did you know we’ve been in this business for over four decades?) and knows all the ins and outs of pharma manufacturing. It’s like choosing a good mechanic – you want someone you can trust (in this case, with your EMS).
Remember, a vendor audit is a must. It’s like checking references before hiring someone – you want to make sure they’re as good as they say they are.
In the end, following these guidelines and choosing the right partners will help ensure your EMS is top-notch, keeping your pharmaceutical manufacturing process safe, efficient, and compliant with all those important regulations. It’s a big job, but somebody’s got to do it – and do it well!
If you’d like to learn more, we’ve got tech papers and more about this very topic.