The transfer of personnel and materials in and out of cleanrooms are a common concern in the design and operation of the facility. Transfer implies there is a transition from one cleanliness level to another one, as there are separate rooms that require the transfer.
Transferring of personnel, large materials nor continuous process feeds are covered in this article. The topic that is addressed is the transfer of materials via pass-through boxes (PTBs).
PTBs are generally known and used in cleanrooms. They play a role in several functions: First, they allow materials to be transferred, second they provide a barrier between the two adjacent clean rooms, and third they protect the cleaner cleanroom against ingress of less clean air during the transition. Commonly a PTB consists of a space within two interlocked doors, so only one door can be opened at a time.
Applications
PTBs can be seen in many applications. The use of them and the required dimensions and volume largely depend on the scale of the operation the cleanroom is used for. The use can generally be categorised in terms of inbound or outbound.
Inbound transfers typically include: Contained supplies (process materials, media, process utensils, environmental monitoring (EM) materials, cleaning materials and agents). Outbound transfers typically include: (half) products, product samples, EM samples, used instruments, product and utensils packaging waste, cleaning waste.
PTBs can also be identified by the cleanliness level the entrance is from to the cleanliness level it is transferring to. This is shown in Table 1. Notably, this table only refers to the airborne particle concentrations. Comparable relations can be made based on the EU-GMP grades. This is shown in Table 2.
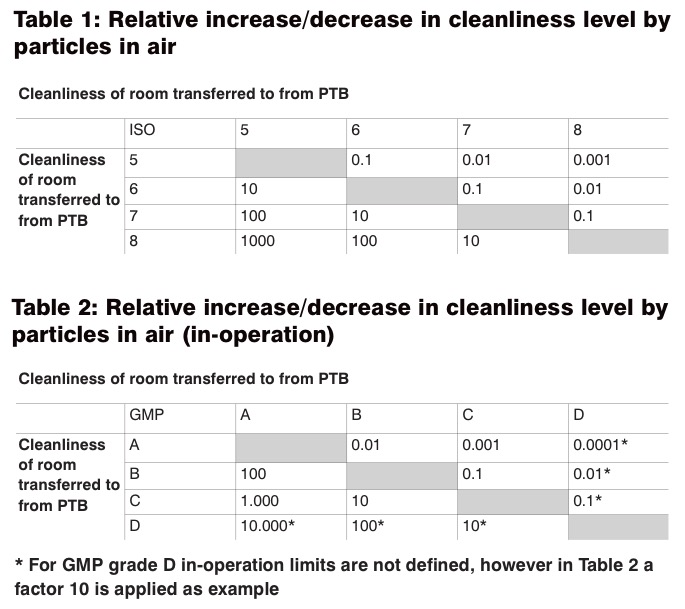
For an inbound pass-through situation, other aspects need to be considered as well. These can include the surface contamination of the materials to be transferred, as well as contaminants other than particulates like biocontamination. Normally there is a transition activity during the transfer to aid this. That action can be: wiping, unwrapping or uncovering one protecting layer. For many years, complete sterilisation by a pass-through autoclave has been used, and now methods like illumination using UV and surface decontamination by VHP are also being used. However, these special cleaning, disinfection and sterilisation steps are not considered in this article.
Types of ventilation in PTBs
PTBs can be found either actively ventilated, passively ventilated or not ventilated. The ventilation principle can be either balanced flow (supply and extract), positive flow by air blown into the PTB, negative flow: the air is extracted from the PTB. The latter can be applicable when containment aspects need to be taken care of (Sink).
One widespread common type of PTB ventilation is based upon passive ventilation
All types with active ventilation require supply and/or extract air volume control as well as a form of pressure control. As the internal volume of a PTB is limited, the pressure control aspects need adequate design.
One widespread common type of PTB ventilation is based upon passive ventilation: overflow via the PTB from the room with the higher pressure towards the room with the lower pressure. This can be either by the limited leakage path of the PTB or by a defined overflow design (Figure 1).
Annex 1 proposed draft
In the latest proposed draft of the EU GMP Annex 1, the place of PTBs, referred to as Pass-through hatches, are included in view of the overall 'contamination control strategy' [CCS]. This CCS considers all steps concerning personnel, material and equipment movement and operation under the general term of Airlocks:
- "Airlocks should be designed and used to provide physical separation and to minimize microbial and particulate contamination of the different areas, and should be present for material and personnel moving between different grades".
- Airlocks should be flushed effectively with filtered air to ensure that the grade of the cleanroom is maintained.
- The final stage of the airlock should, in the "at rest" state, be of the same cleanliness grade (viable and non-viable) as the cleanroom into which it leads.
For PTBs specifically, the draft Annex 1 contains two statements:
- "Pass-through hatches should be designed to protect the higher grade environment, for example by effective flushing with an active filtered air supply."
- "The movement of material or equipment from lower grade or unclassified area to higher grade clean areas should be subject to cleaning and disinfection commensurate with the risk and in line with the CCS."
Statement 5 is typical for the kind of materials and equipment to be transferred as described above. Statement 2, 3 and 4 require more careful analysis.
First of all, there is the requirement for protection of the higher grade environment (1 and 4). This can be referenced to the table 1 and 2 analysis. Transferring from ISO Class 8 to Class 7 requires a cleanliness step of 10 times better. In EU-GMP-Annex-1 terms, this would be from Grade C to B (operational). The method suggested as an example is flushing by active filtered air. It can be observed that the protection applies to both inbound as well as outbound PTBs.
PTB classification
The direction of movement of the material or equipment makes the difference.
When moving outbound (from a higher grade to a lower grade or not classified area) there is a decrease in cleanliness. When considering (half) products, they need to be protected by a suitable container or wrapping. When considering waste materials there is no important product cleanliness consideration unless it is waste that requires containment. Outbound PTBs only require to protect the higher grade environment.
Required dimensions and volume largely depend on the scale of the operation
When moving inbound (from a lower grade to a higher grade e.g. EU-GMP grade D to grade B) what would be required for an intermediate PTB?
For rooms operating as a personnel airlock or material airlocks, a common solution is to have a D/C Airlock followed by a C/B Airlock.
When considering a PTB as an airlock, statement 3 becomes of great importance: There needs to be a transition when transferring from D to C to B. An EU-GMP grade C PTB could interpose between a grade D and grade B cleanroom. The PTB has an ISO Class 7 classification at rest and the cleanroom ISO Class 7 in operation. However, the microbial limits for the CFU are 10 times lower for the grade B cleanroom. Here a further analysis provides guidance: the main source of CFUs is human operation, while PTBs, by dimension and function, only have human operation when transferring materials in and out. Thus controlling the transfer operation in airflow within the required microbial limits of the higher grade environment will suit the situation.
For example, contained supplies are unwrapped in the PTB and afterwards transferred to a grade B cleanroom. From the CCS point of view, a grade B environment in the PTB is desirable for the unwrapped materials. Assuming the PTB is passively ventilated by overflow air from the grade B cleanroom, a grade B classification in the PTB will be present as well.
In addition to the non-viable particles and microbial contamination, the surface contamination needs to be considered to protect the unwrapped supplies. The unwrapped supplies will enter the grade B environment, the overflowing air will only flow out of the B environment.
To read more about the equipment's use in ATMPs and performance testing, read more in part 2 of this review.