Cleanrooms are critical environments used in various industries such as pharmaceuticals, biotechnology, electronics manufacturing, and aerospace. Maintaining the highest levels of cleanliness and controlling environmental factors like particulate matter, temperature, humidity, and pressure is essential for the success of operations within cleanrooms. However, achieving these stringent requirements relies on the structural support systems that uphold the integrity of the cleanroom environment. Here are some ways cleanroom systems are structurally supported.
Modular wall systems: Modular wall systems are a popular choice for cleanroom construction due to their flexibility and ease of installation. These systems typically consist of prefabricated wall panels made from materials like stainless steel or aluminum. The panels are supported by the floor and ceiling track systems to help create the envelope of the cleanroom. Modular wall systems offer versatility in design and can accommodate various cleanroom classifications and layouts.
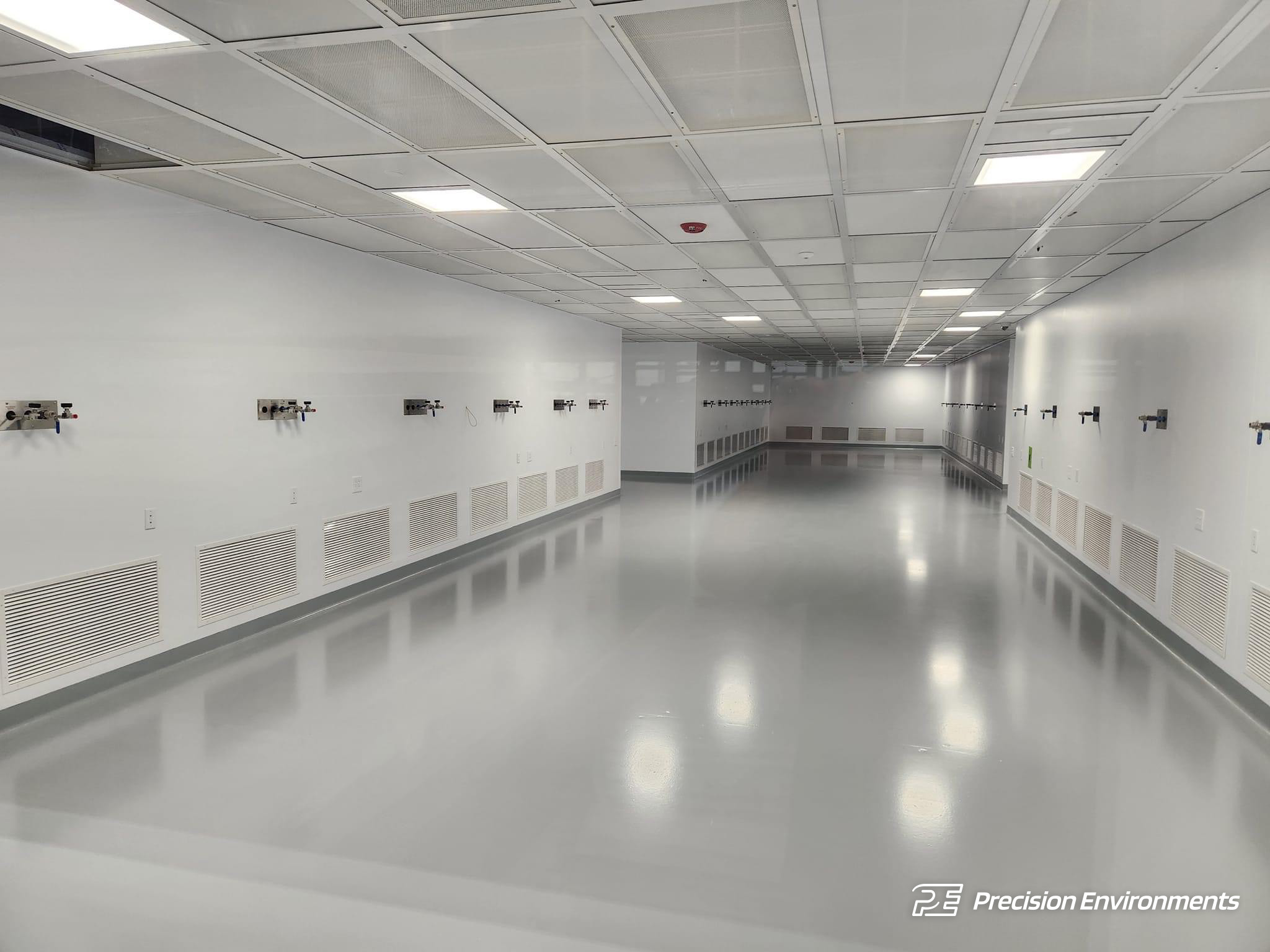
Ceiling systems: Cleanroom ceiling systems are supported by a grid or other framework suspended from the building structure above or an independent steel structure. If your cleanroom calls for supporting the ceiling system from the existing structure above, make sure that the appropriate structural information is available. This information is critical to determine if the building structure can withstand the load of the cleanroom. This ceiling system provides support for ceiling panels, lighting fixtures, air vents, and other utilities required within the cleanroom. A grid design allows for easy access to the plenum space above the cleanroom ceiling for maintenance and servicing of equipment.
Raised flooring: In some cleanroom environments, raised flooring systems are utilized to support equipment, provide access to utilities, and manage airflow. These flooring systems consist of modular panels supported by pedestals or grids, creating a raised platform above the building floor. It is important to plan the location of equipment or other material that may need to have further support under the raised floor due to increased weight. Additional pedestals may need to be incorporated, or specific raised flooring systems designed to support larger volumes can be utilized.
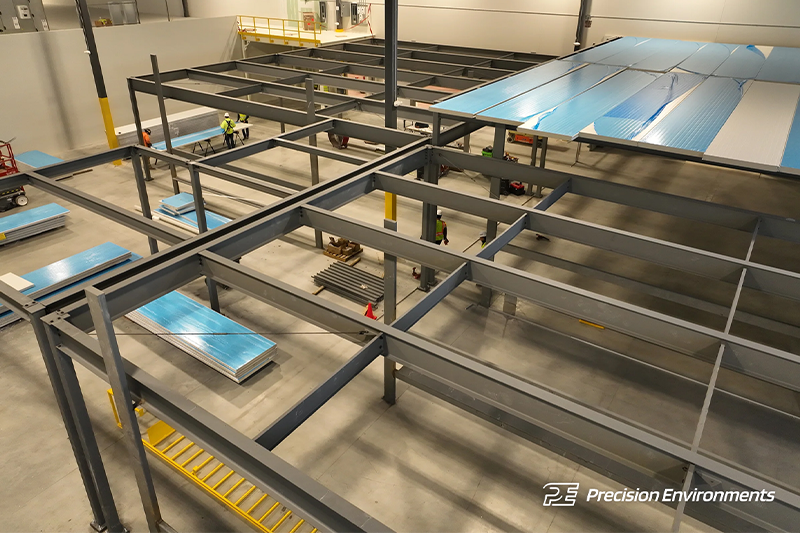
Steel framing: Steel framing is common in cleanroom construction to provide structural support for walls, ceilings, and equipment. Steel beams and columns are engineered to withstand the loads imposed by cleanroom components and machinery while maintaining the desired level of structural stability. Steel framing offers strength, durability, and precision in construction, ensuring the integrity of the cleanroom environment. These independent steel structures allow for cleanrooms to be built in areas where existing building steel may not be able to support the load of a cleanroom and its components.
Seismic support systems: In regions prone to seismic activity, cleanroom structures must be designed to withstand earthquakes and other natural disasters. Seismic support systems incorporate specialized engineering techniques and materials to mitigate the effects of seismic forces on cleanroom facilities.
The structural support systems employed in cleanroom construction play a crucial role in maintaining the integrity and functionality of these specialized environments. Whether utilizing modular wall systems, ceiling grids, raised flooring, or implementing an independent steel structure, careful consideration must be given to design, materials, and engineering to meet the stringent cleanliness and operational requirements of cleanroom facilities. By employing the appropriate structural support systems, industries can ensure the success of their cleanroom operations and uphold the highest standards of quality and safety.