As most readers will be aware, Annex 1 of EudraLex Volume 4 (GMPs) is being updated. The process has been somewhat protracted with multiple versions being reviewed, updated, and discarded. What has not changed throughout these numerous revisions is the requirement for a site to have a Contamination Control Strategy (CCS) in place. While there is plenty of literature out there to explain what a CCS is, there is minimal direction on the practicalities of implementation.
The Annex 1 CCS requirement will place sites in one of three broad categories; having a CCS already in place (possibly under a different name), having identified the elements that will form a CCS but may need a refresh to comply and finally, those that need to define and develop a complete CCS.
As anyone who has spent even a limited amount of time in the industry will know, changes to a site strategy and closing any gaps between existing practice and regulatory requirements can be like trying to turn the proverbial oil tanker – or perhaps steering one through the Suez Canal.
The use of a supplier as a fresh pair of eyes may prove invaluable
So what can you do to leverage existing data, people or processes to aid in the formulation of your CCS in the most efficient and least disruptive way possible? Our suggestion would be to break the process into four areas ‐ gathering expertise, performing the assessment, gathering supporting documentation and validating any mitigation actions.
First and foremost is to identify the people who can help. It isn’t likely that one individual has all the necessary knowledge or expertise to put together a site wide CCS on their own. A team approach is required with the relevant expertise available to help. The bulk of the heavy lifting will be provided by your in‐house Subject Matter Experts (SMEs) or those from corporate functions. However, don’t be afraid to reach out to your suppliers to help too. Good suppliers will have expertise on hand and should be happy to help a customer on a specific aspect of their CCS. In fact, the experts employed by a good supplier may well have a greater depth of knowledge on specific subjects than those that can be found on a manufacturing site. For example, Ecolab’s Technical Consultants are able to bring insights of regulatory requirements, updates and industry best practise related to a variety of areas of contamination control.
Once the team of relevant knowledgeable people has been assembled, a good next step would be to look at what a site already has in place that can contribute to the CCS, and what gaps there may be.
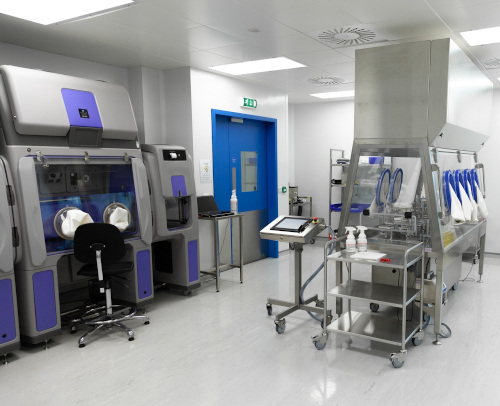
Regulator expectations
Annex 1 itself provides a comprehensive list of what a regulator would expect to form the backbone of your CCS. Once the requirements of a CCS are known, an assessment can be performed to identify foundations that are already in place and gaps that exist. Utilising the team of assembled experts should ensure that qualified people are looking at your processes to identify contamination control risks. Again, the use of a supplier as a fresh pair of eyes may prove invaluable here. Experts with specific, in‐depth knowledge in a particular area of contamination control may see what has previously been overlooked, offering information to help steer you to perform appropriate risk identification and assessment. For example, Ecolab offers on‐site and virtual technical support in assessing risks from personnel cleanroom behaviours, contamination control risks from cleaning and disinfection practices, risks from incoming goods through transfer disinfection steps and critical zone contamination risks through isolator loading and decontamination assessment.
A site’s CCS will become part of a regulator’s inspection agenda. This means hard evidence, and documentation, will be required by the site to demonstrate what they have put it in place. The vast majority of the documents required as part of this evidence will be live documents already in place, such as risk assessments, Quality Management System (QMS) metrics and Standard Operating Procedures (SOP’s). As with performing a gap assessment against the CCS requirements, these documents should be reviewed to ensure that they meet the identified CCS requirements.
Annex 1 itself provides a comprehensive list of what a regulator would expect
As most readers will be aware the tranche of documents created by a working site can be vast. Utilise your assembled team to perform an in‐depth analysis on your current documentation and identify gaps. Ensure your suppliers provide robust technical documentation to help close out the gaps in your CCS such as technical data, rationale documents and validation documents.
The final part of any approach to mitigating identified gaps is the potential task of performing additional or new validation. Validation should not be undertaken without good reason; it is costly and resource intensive.
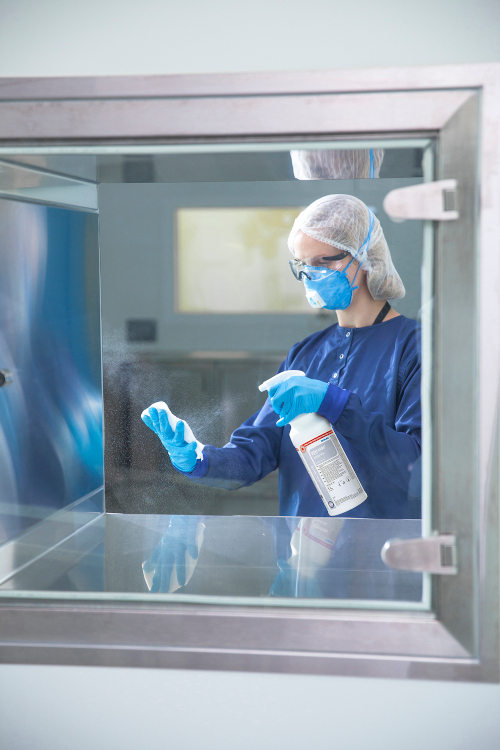
As a key part of any site’s contamination control strategy, cleaning and disinfection validation is a great example of where a customer should turn to suppliers for help. As an example, Ecolab experts routinely perform in‐depth analysis of current and planned validation strategies for disinfection and decontamination including ensuring compliance across different regulatory agencies. We optimise validation plans utilising our extensive Validex data package, through bespoke customer validation project management or by customers utilising our online validation portal to capture validation rationale, data and reporting.
On a final note, there is (as yet) no fixed template that a regulator would recognise as a CCS. A site’s CCS will and should be a living document and a process that changes with the site. The CCS will need revision when manufacturing changes or when a site stops a process. It should also be regularly revised, audited and inspected.
It is likely, there will be future citations in industry from CCS that are found lacking. Don’t let it be you! Ecolab are here to help, now is the time to start, not when the Annex is finally published.