For the last 15 years, Budweiser Budvar have chosen to partner with global leading, high-speed door manufacturer EFAFLEX, and here Darren Turrell, UK Managing Director, helps to explain why, "Consumers may give little thought to how beverages such as beer arrive on supermarket shelves, but for us at EFAFLEX we understand the various stages that bottle may have travelled from production, packaging, despatch, transportation and fulfilment. Time is of the essence in the beverage industry, but where people, robots to aid automation, and vehicles such as forklift trucks share the same workspace, then the risk of accidents can increase. Up to 120,000 bottles are processed here per hour; that’s filled and packed, which could be a logistical challenge. But we are well versed with such challenges, and typically if a customer has a 'problem,' then we can provide a bespoke solution."
A representative from Budweiser Brewery adds, "For us, the flawless operation of the doors is vital. Part of the brewing process relies on our products being cooled, meaning that any door malfunction or downtime would result in an enormous economic cost."
EFAFLEX are no strangers to innovation and have been pioneering high-speed industrial doors industry since 1974, with each of their spiral, folding and roll-up options engineered with safety and performance in mind.
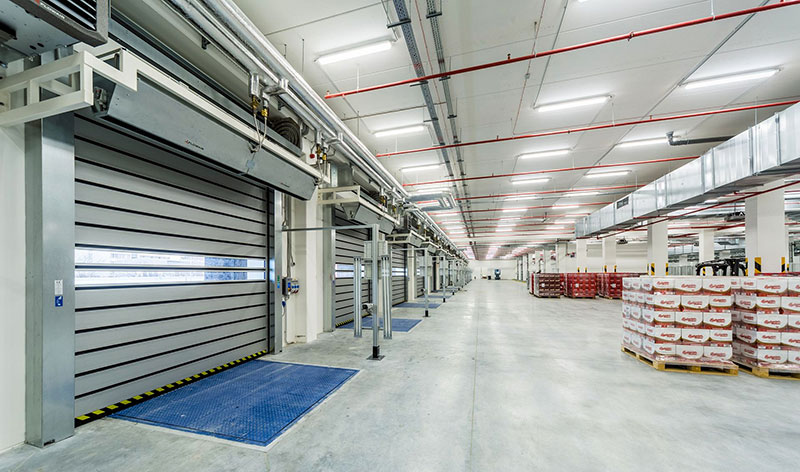
Above all, the doors recommended for this particular project had to be fast, robust, and reliable, as they are placed under huge performance pressure, completing over 250,000 opening cycles per year. They formed part of an extension with seven aisles added to the existing logistic centre, covering approximately 20,000 pallet locations with more than 440 pallet manoeuvres recorded each hour. Here the production flow and logistics need to work seamlessly. Utilising a 164-metre-long overhead bridge, and monorail transporting more than 2,000 bottles per minute, the new construction reduces traffic between buildings with the EFAFLEX doors acting to separate the production hall from the warehouse. Opening at speeds up to 3 metres per second, the turbo doors help ensure the temperatures remain constant in the production halls and storage areas.
Travelling onwards to the despatch area, and EFAFLEX doors are also located at the loading bays to speed up and improve safety. Using thermal laths, the doors provide heat insulation, and with their fast opening and closing action, minimise exposure to the elements and in turn reduce energy costs.
Back to Darren Turrell of EFAFLEX to summarise, "Track a single bottle of beer at this processing and logistics centre, and it will travel through a number of EFAFLEX doors. But regardless of door type, all of EFAFLEX's models will help speed up production and logistics, reduce energy costs and improve user safety. They are fast, efficient and built to last."
Check out the range of high-speed doors that have been specifically designed for the food and beverage industry. Visit www.efaflex.co.uk to download technical information, brochures and video links to see the product in action.