In a cleaned cleanroom without running equipment, the cleanroom installation, which consists of the cleanroom envelope, air conditioning, filtration & circulation system and the cleanliness of the outside air, determine the resulting air cleanliness in the at rest state. There will be no particle deposition of macroparticles.
In the operational state, the airborne particle concentration increases by the ratio between total source strength and effective air supply volume.
The effective air supply is the air supply volume times the ventilation efficiency. The ventilation efficiency is the ratio between the local recovery and overall recovery. The air supply volume and room size will determine the removal efficiency of particles.
In most cleanrooms, the source strength is determined by personnel
In most cleanrooms, the source strength is determined by personnel. In general, the average cleanroom space per person, the selected garment and changing procedure determine the resulting source strength for the particle size range from 0.1 um to visible particles.
Then the clean air supply will determine the air cleanliness and particle deposition rate.
After some time due to particle deposition, the number of surface particles will increase and a small fraction can resuspend into the air and contribute to the deposition of particles. The cleaning programme should keep surface concentrations sufficiently low.
How to operate a cleanroom is described in ISO 14644-5. The present standard was published in 2004. A new version is in preparation. The Committee Draft has already been reviewed by the 24 participating member countries of the ISO Technical Committee 209.
Human contamination
A person sheds more than a billion particles per 24 hours. This does not happen evenly but in bursts depending on the lifestyle and activities of the person. The emission can vary from 100,000 to 10,000,000 particles ≥ 0.5 µm per minute.
The number of emitted particles is reciprocal proportional to the particle size, which means that the product of the number of particles and particle size is constant per observed period.
In addition, the level depends on the person and their activity. The number of shed particles can be reduced by wearing occlusive clothing with a proper barrier function.
Guidance for the selection of cleanroom clothing and other cleanroom consumables is described in a new standard that will be published shortly, ISO 14644-18.
A person sheds more than a billion particles per 24 hours
A person also picks up particles from various surfaces and from the surrounding air (outside the cleanroom) onto the street clothing. During changing into cleanroom clothing a fraction of these particles can be transferred to the outside of the garment by contact transfer and deposition.
The barrier function of cleanroom garments increases for larger particles, but still some nearly visible particles can be emitted.
The impact of the clothes that are worn under the cleanroom garments can be reduced by the use of cleaned cleanroom undergarments. Alternatively, regularly cleaned indoor work clothing of non-natural fibres can limit the cross contamination that is observed with street clothing.
For evaluation purposes, Table 1 could be used. An estimate is made for cleanroom coat (smock) with head and shoe cover (or cleanroom shoes), overall with hood and cleanroom shoes, overall with hood, boots, face mask and goggles (full cleanroom suit) and a combination with undergarments.
The expected real emission will be somewhere within a + 50% range of the given numbers.
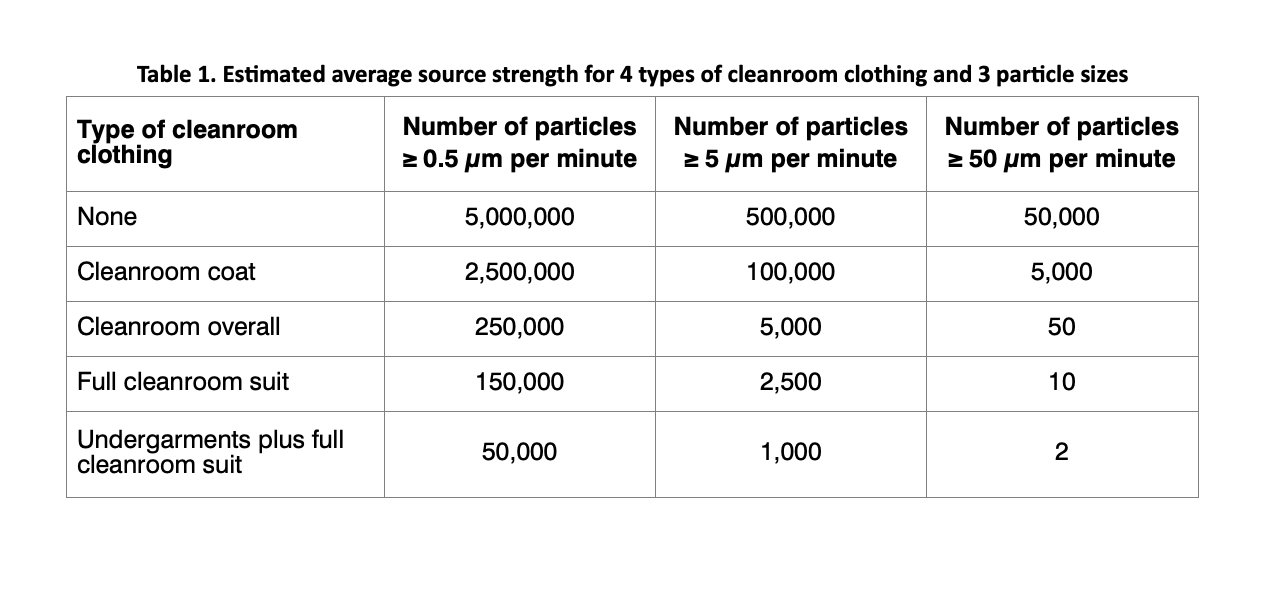
Personnel not only emit particles (and microbe-carrying particles) but also distribute particles on surfaces. By walking and arm movements surface particles can resuspend into the air.
If personnel do not understand the impact of their actions, they can also contribute to contamination by disturbing air flows and particle transfer by contacting unclean contact surfaces and critical surfaces.
The consequences of human activity with respect to contact transfer and resuspension can be reduced by keeping surfaces clean by frequent cleaning.
Operations control programme
Most activities are performed by personnel unless the requirements are such that people must be separated from the critical location. Separative devices are described in ISO 14644-7. This document is in revision.
The impact of human activity can be controlled by implementing the guidance provided by ISO 14644-5. The new version recommends setting up various operations control programmes.
The major activities executed by people are:
- Entering and leaving the cleanroom
- Cleaning
- Bringing in and taking out goods
- Executing work processes
- Maintenance
For design of an operations control programme, a risk assessment should be performed. For proper execution, personnel need to be trained. The effectiveness of the operations control programmes needs to be monitored. When necessary a programme needs to be improved.
For leaving and entry of the cleanroom, important aspects are the number of persons, number of shifts, lockers for personal goods, facility to wash hands, cleanroom clothing, frequency of use of cleanroom garments, storage space for cleanroom clothing, stages of changing etc.
The way the cleanroom will be exited is important too, as well as how entry and exit are separated, physically or in time.
To be able to execute the intended entry and exit the control programme should be drafted before the design of the cleanroom and therefore included in the requirements. For the design, construction and start up, last year a new standard ISO 14644-4 was published.
Cleaning of surfaces is very important in contamination control
Cleaning of surfaces is very important in contamination control. Cleaning can be divided into cleaning of large surfaces (floors, walls, doors, windows, and ceilings) which is mostly executed by professional cleaners, equipment, tools, work surfaces and incoming goods, which is mainly done by personnel.
In case of microbiological contamination disinfection processes can be added. Ideally, the intended cleaning processes and the required facilities should be determined before setting up a cleanroom. For the selection of cleaning processes guidance is given in ISO 14644-13:2017.
For the entry of goods into the cleanroom, what are the intended goods such as equipment, tools, parts and materials, their size, number and surface cleanliness is important.
Maybe space for unpacking, manual cleaning and cleanliness inspection is required. Sometimes a cleaning process will be part of the entry programme. The intended entry and exit of goods are important inputs for the design and construction of a cleanroom.
The barrier function of cleanroom garments increases for larger particles, but still some nearly visible particles can be emitted
Often during work processes, personnel are in close contact with critical areas near critical surfaces. Work processes should be designed in such a way that the distance between operator and critical surfaces is maximal without any movements above critical surfaces.
Contact should be avoided or proper tooling should be developed. Tools and parts should be shielded as long as possible etc. The operator should not disturb clean air flow that must protect the critical surfaces.
Preventive and corrective maintenance action should be described in such a way that the contamination is minimised.
This means that cleaning should be a part of the maintenance process. Preferably clean(ed) cleanroom tooling should be used. Otherwise, there must be a cleaning programme for tools and replacement parts.
Training of personnel
For the implementation and execution of the operations control programme, proper training of personnel must be organised.
Such training should not be limited to the teaching of procedures, but also the understanding of contamination mechanisms and the explanation of the need for procedures.
Entry and exit should be separated, physically or in time
Training should be done in small groups in a class room and practical training in a training cleanroom. During retraining, the training should not be repeated, but be refreshed by discussions and exercises on the awareness of the impact of human behaviour. Intermediate e-training can be useful.
Monitoring
All activities in a cleanroom should be described in procedures. The proper execution and the effectiveness of these procedures should be monitored.
Next to environmental monitoring, results of quality and yield of the executed processes should also be included in the evaluation of monitoring data. Acquired data can be used to determine cleaning efficiency and particle deposition rates.
Limiting the impact of human contamination
The layout, air conditioning, selected garments, garment use, changing procedure and its execution and cleaning all determine particle supplied. Particles carried into the cleanroom then become a part of the system that determines the air cleanliness and particle deposition rate.
Reduction of these particles makes a reduction of the supply air volume possible and this will reduce energy use.
It is recommended to determine the maximum required personnel in the cleanroom and associated procedures before setting up the cleanroom. Select the garments as occlusive as possible to limit the emission of particles.
In the changing room, the person changing into cleanroom garments could be considered a critical surface
Provide enough space for changing into cleanroom clothing to limit cross contamination by other people entering the cleanroom. In case the impact of personnel needs to be reduced, do not reuse the cleanroom clothing too many times.
Each use, the garments become more contaminated, which will increase cross contamination from the inside to the outside and the environment.
In the changing room, the person changing into cleanroom garments could be considered a critical surface. This will help in determining the required air supply and air circulation.
A person without cleanroom garments will have high particle emission and therefore the air cleanliness will reduce.
The changing room should be cleaned more frequently than the cleanroom
Air circulation determines the removal efficiency and it is recommended to make this the same or better than in the cleanroom depending on the number of persons passing the changing room. Further, the changing room should be cleaned more frequently than the cleanroom.
Using the data in table 1 and the actual or considered air supply over the area per person, the expected increase of airborne concentration of particles ≥ 5 µm C5 can be calculated.
As a start the following formula can be used: C5 = 2S5 /Q ,where S5 is the emitted number of particles ≥ 5 µm per minute and Q is the clean air supply over the area of the person in m3/min. With a good ventilation efficiency, this can be reduced by 20 to 40%.
ISO 14644-17:2021 describes a relationship between airborne concentration of particles ≥ 5 µm C5 and particle deposition rate of particles ≥ 5 µm R5 that can be removed by air flow by using: R5 = 81.2 C50.773.
Particles ≥ 50 µm cannot be removed by air flow and they will deposit on surrounding surfaces.
The expected particle deposition rate of particles ≥ 50 µm R50 can be determined by the emitted number of particles ≥ 50 µm per minute S50 divided by the area impacted by the person in m2 Ap. Ap will be about 4 to 8 m2 depending on the size of the changing room.
Personnel are important and difficult to replace with mechanisation
The total particle deposition will determine the surface particle concentration. This calculation can be used to determine the cleaning frequency, but also to estimate the pick by shoes and clothing that will walk into the cleanroom. Transfer via shoes can be reduced by using clean tacky mats.
When people leave the cleanroom and undress, there can be an explosion of particles. Therefore, entry and exit should be separated physically or in time.
Personnel should be trained and retrained to perform the changing and the entry and exit procedure regularly. Hand washing and use of gloves should be included in this training.
Real-time monitoring of air cleanliness and particle deposition rate show the impact of changing by personnel. With acquired data simple calculations will show how many particle will be carried into the cleanroom.
However, removal of surface particles is not easy, even an air shower will only remove a small fraction depending on the shower time and conditions. During activities in the cleanroom, a fraction of the surface particles will be released.
Personnel are important and difficult to replace with mechanisation. However, if killer particles are smaller than 5 µm there should be a separation between personnel and vulnerable product and process surfaces.
Conclusion
As long as some environmental contamination by macro particles is accepted, proper facilities, procedures and training can limit the negative impact of personnel sufficiently.
Improved operation control will reduce the particle deposition rate and through that, the likelihood of surface contamination. Improvement of cleanroom operation reduces the air supply volume that is necessary to reach the required air cleanliness level. This will reduce the required amount of energy.
Example: Air and surface cleanliness during changing
In this example the impact of emission of particles ≥ 5 µm an particles ≥ 50 µm by personnel is calculated. Particle emission by a person: S5 = 500.000 particles and S50 = 50.000 particles per minute; Changing area per person is 4 m2 and room height is 2.5 m and air supply Q is 30 m3/h per m2;
The air supply per person is 4 × 30/60 = 2 m3 per min. The air change rate of 30/2.5 = 12 per hour.
The airborne particle concentration increases with C5 = 2 × S5 /Q = 2 × 500.000 /2 = 500.000 particles ≥ 5 µm per m3.
The particle deposition rate particles ≥ 5 µm after entering until changing is completed will be R5 = 81.2 × C50.773 = 2,065,000 particles ≥ 5 µ per m2 per hour or 34,400 per m2 per minute per person.
Impact on surface cleanliness of the changing room floor during 5 minutes will be: 34,400 × 5/4 = 43,000 particles ≥ 5 µm per m2 per entry per person.
The particle deposition rate particles ≥ 50 µm after entering until changing is completed will be: R50 = S50/Ap = 50,000/4 = 12,500 particles ≥ 50 µ per m2 per min per person.
Impact on surface cleanliness of the changing room floor during 5 minutes will be: 12,500 × 5/4 = 15,600 particles ≥ 50 µm per m2 per entry per person.
The deposition of particles in the changing room will increase with the number of persons and number of entries. In case the same space is used for undressing the deposition will become much higher.
The impact can be reduced by increasing the cleaning frequency.