These batteries are the heart of EVs, providing the power needed to propel these vehicles. However, manufacturing lithium-ion batteries is a complex process that demands meticulous control over various factors, including particle contamination.
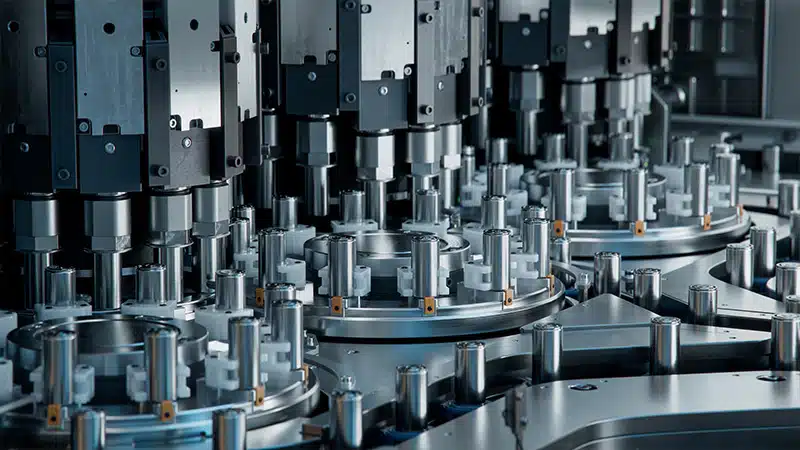
Particle Contamination: A Hidden Threat to Battery Safety
Particle contamination poses a significant threat to the safety and performance of EV batteries. Even the smallest particles, invisible to the naked eye, can have detrimental effects. Conductive particles, such as iron or nickel, can form needle-like structures called dendrites that bridge the gap between the battery’s anode and cathode, causing a short circuit. This can lead to sudden power loss, overheating, or even a fire.
The risk of particle contamination is particularly high during the manufacturing process when battery components are exposed to dust, debris, and airborne particles. As the battery ages, the mechanical stability of its components decreases, making them more susceptible to damage from particle contamination.
Detecting and Analysing Particle Contamination: Ensuring Safety and Quality
To safeguard the safety and quality of EV batteries, it is crucial to employ effective methods for detecting and analysing particle contamination. Various techniques are used to identify particles during the manufacturing process:
- Photo-optical systems: These systems use light to detect particles passing through a beam of light.
- Infrared thermography: This method utilises infrared cameras to detect particles based on their temperature difference compared to the surrounding environment.
- X-ray technology: X-rays can penetrate the battery and reveal the presence of particles.
- CT scans: CT scans provide a three-dimensional image of the battery, allowing for precise particle location and identification.
Particle Monitoring Environmental System: A Critical Safeguard
A robust particle monitoring environmental system is an indispensable component of any EV battery manufacturing facility. This system should encompass:
- Real-time particle counters: These devices continuously monitor the number and size of particles in the air. They ensure that the cleanroom environment adheres to permissible particle concentration levels.
- Surface particle detection: Techniques like wipe tests or adhesive sampling assess the cleanliness of surfaces where battery components are handled.
- Environmental monitoring: Continuous monitoring of temperature, humidity, and airflow, which can influence particle behaviour and contamination risks.
- Data analysis and reporting: Automated systems collect and analyse data from particle counters, providing insights into contamination trends and enabling timely decision-making.
Cleanroom Standards and Sterility Levels: Ensuring Pristine Conditions
The sterility level within an EV battery manufacturing cleanroom is critical for ensuring the safety and quality of the batteries. Standards like ISO 14644 define the classification of air cleanliness in cleanrooms and controlled environments. For EV battery manufacturing, achieving an ISO Class 5 or better is often necessary due to the sensitivity of battery components to contamination. This classification mandates maintaining a particle count of not more than 3,520 particles (≥0.5 µm) per cubic meter.
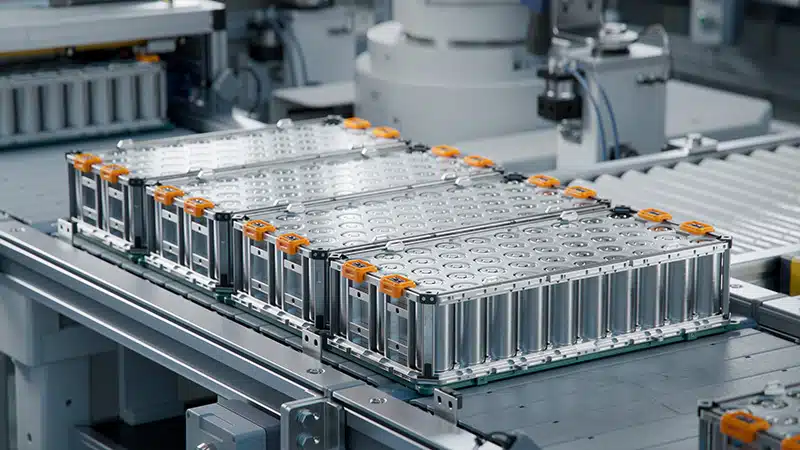
Cleanroom Environment’s Impact on EV Battery Safety and Quality
The cleanroom environment has a direct impact on the safety and quality of EV batteries. A well-maintained cleanroom with effective particle monitoring significantly reduces the risk of contamination, enhancing the reliability and performance of the batteries. It minimises incidents of internal short circuits (ISC), extends battery life, and reduces the risk of costly recalls.
Addressing Challenges through Technology and Standards: A Path to Safe and Sustainable EV Batteries
The demand for EVs has highlighted the importance of high-quality battery production, where particle contamination poses a significant challenge. An effective particle monitoring environmental system is essential for maintaining the required sterility levels in cleanrooms, thereby ensuring the safety and quality of EV batteries. Continual advancements in detection technology and adherence to stringent cleanroom standards are crucial in addressing these challenges.
By implementing effective particle monitoring and control measures, EV battery manufacturers can produce high-quality, safe batteries that will power the future of sustainable transportation.
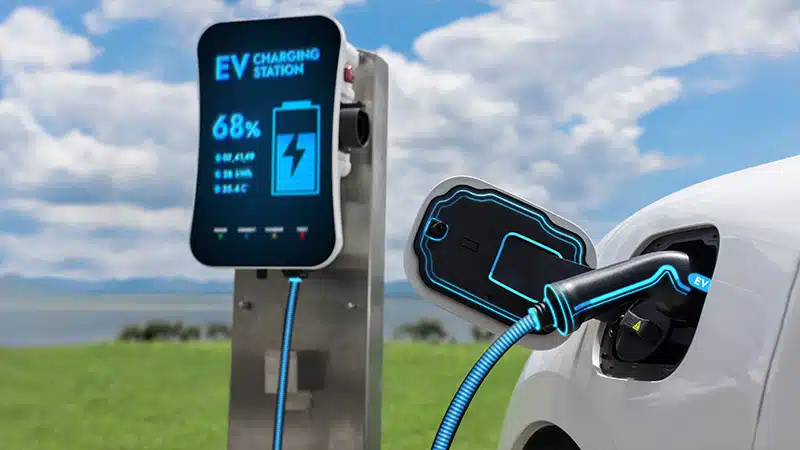
ApexRBp: An Advanced Solution for Particle Monitoring in EV Battery Manufacturing
ApexRBp is a revolutionary particle monitoring system, standing as a beacon of technological advancement in the realm of EV battery manufacturing. This cutting-edge system addresses the critical need for precise particle detection and control, ensuring the production of high-quality, safe batteries that power the future of sustainable transportation. Lighthouse's real-time particle counter provides continuous and accurate particle count data, enabling proactive identification and mitigation of contamination risks. It continuously monitors temperature, humidity, and airflow, factors that significantly influence particle behaviour and contamination risks.
ApexRBp’s data analysis and reporting capabilities transform raw particle data into actionable insights. This data-driven approach enables timely decision-making and proactive contamination prevention strategies.
ApexRBp helps you maintain stringent cleanroom standards, including ISO Class 5 or better, ensures the highest level of sterility in EV battery manufacturing facilities. Its advanced capabilities, coupled with its commitment to industry standards, make it an indispensable tool for ensuring the safety, quality, and sustainability of EV batteries.
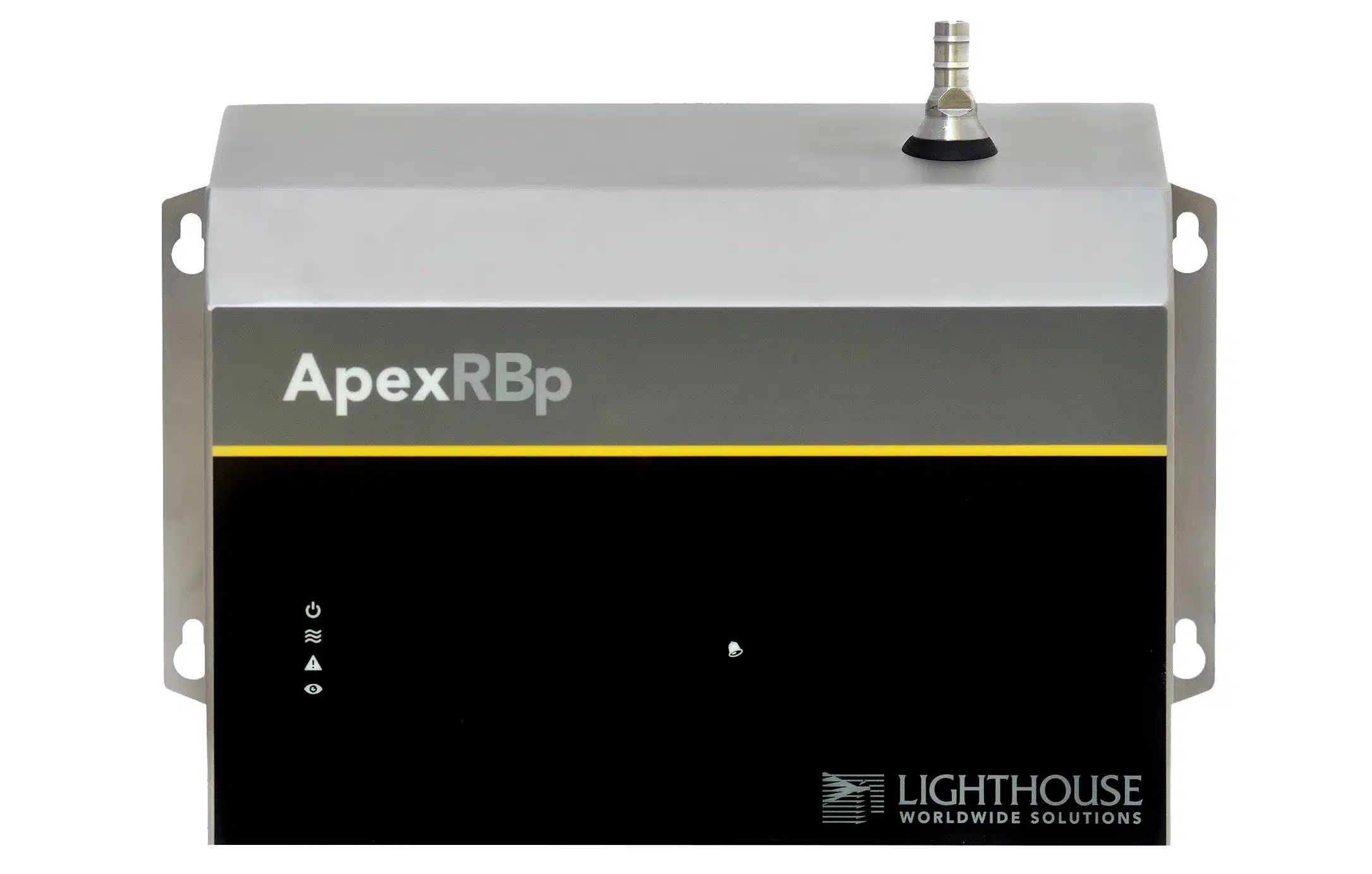
As the demand for EVs continues to soar, ApexRBp stands poised to play a pivotal role in shaping the future of clean and sustainable transportation. Contact us today for more information.