Specialist cleaning cloths are used in many areas of industry to ensure surface cleanliness by mechanical removal of dust and biological contamination. Modern materials and the method of production make it possible to reduce the amount of disinfectants used, while obtaining the same effects of removing bioparticles. In cleanrooms, special-purpose cleaning cloths are used to effectively remove bacteria, fungi and viruses from the surface.
Dust and biological pollutants, identified in ISO8-ISO7 clean room classes, pose a serious risk of failure of the manufacturing process or experimental research. Environmental monitoring carried out in order to confirm the microbiological and dust cleanliness of the air and surfaces serves the early detection of potential threats as well as the development of effective methods of eliminating pollutants by mechanical removal from the surface and disinfection.
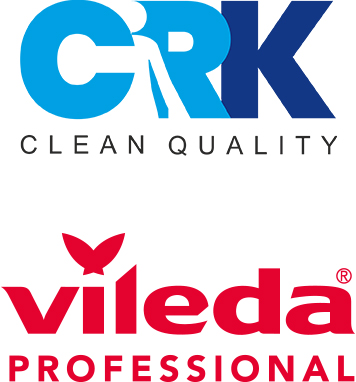
Among the biological factors that can really affect the experimental or production process, we can distinguish the so-called TAMC (Total Aerobic Microbial Count) and TYMC (Total Yeasts / Molds Count) - that is aerobic bacteria and fungi, which are determined on the basis of tests confirming their presence on surfaces or in the product after an incubation time between 48 and 72 hours. In addition, in the case of some ISO8-ISO7 laboratories classified in accordance with BSL 3-4 requirements, an important element in the selection of specialist cleaning cloths is the risk of surface contamination by hazardous biological agents, including viruses.
In the context of dust pollution, an important element of supervision is the prevention of contamination of the product and the environment with particles of 0,5 - 5,0 microns. Devices called particle counters are used to monitor the degree of air pollution with particles. Particles that fall to the surface can also transmit microbial contamination, so effective elimination of these particles greatly reduces the risk of cross-contamination. In areas where production activities are carried out, activities in the area of risk analysis and validation of the pollution removal process are carried out in order to confirm the effectiveness of activities. The validation activities also include the qualification processes for cleaning and disinfecting agents as well as cleaning cloths and mop covers. Parameters such as:
- structure and material composition of the cleaning cloth
- the degree of release of particles from the surface
- percentage of pollutants removed
- the effect of the cleaning cloth used on the reduction of bio-pollutants
- certificates confirming the possibility of using it in a cleanroom
- the possibility of waste sterilisation
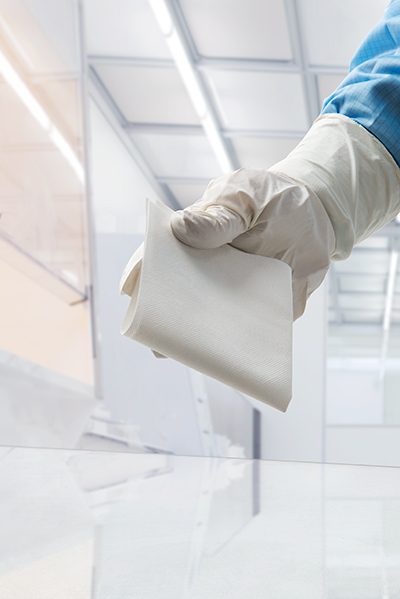
The disinfection process is designed to remove microorganisms and their spores. Disinfection destroys the vegetative forms of bacteria and fungi and shows a certain effectiveness against viruses. Optimising the selection of the appropriate cleaning cloths for ISO8 classes is also associated with the selection of appropriately absorbent cloths, characterised by the appropriate structure and type of fibres, while not generating the risk of contamination of the production environment.
The guides to Good Manufacturing Practice or Good Laboratory Practices not only deal with the disinfection and removal of microorganisms from the surface, but also indicate the need for maintain appropriate microbiological limits, regular monitoring of the environment and rotation of agents used for disinfection. At the same time, the Health Council of the Netherlands in December 2016 published a report called "Resistance due to disinfectants", which indicates that the incompetent, too frequent and abundant use of disinfectants is a direct cause of the mutation of environmental strains of microorganisms, including viruses, and becomes causes resistance to disinfectants, including strong oxidising agents such as chlorites. ANNEX 1 EU-GMP demands the effective remove of disinfectant residues as well as debris. It also stipulates that chemical contamination during the process of disinfection should be minimised.
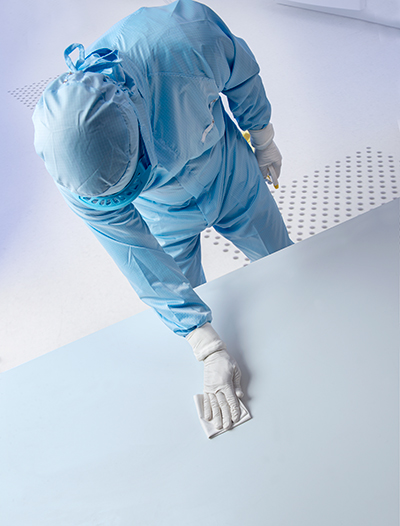
Subjecting the provisions of the report to a more in-depth analysis, the following conclusions should be drawn:
- Too frequent use of disinfectants, especially in the so-called critical, generates a high concentration of the agent on a given surface per unit time.
- It is not necessary to constantly use wipers with a disinfecting liquid, the so-called "Ready to use".
- Sufficient to maintain the proper level of microbiological purity is proper sanitisation of surfaces and devices, while reducing the frequency of using the disinfectant.
- Finally - washing the surface with a suitable quality cloth soaked in purified water or, in justified cases, sterile one, gives similar effects to the use of a disinfectant and has a real impact on the amount of disinfectants used.
Modern specialist cleaning cloths are designed and manufactured in a way that allows for the effective elimination of bio-contamination from the surface with minimum amount or without the use of a disinfectant.
The mechanism of the effectiveness of such action is strictly related to the mechanical removal of the microbiological film, and more precisely to the removal of bacterial, fungal and viral biomass. The water environment is just an element perfecting this process. The way in which the cloth is made is of key importance in this case. Specialist materials for wiping surfaces wet and dry are characterised by a structure that provides the thinnest split microfibres, the diameter of which is divided into several dozen segments, thus ensuring excellent, over 99.9% efficiency in removing bacteria from the surface and 99.51% efficacy in removal of viruses, including viruses belonging to the same family and generic group as SARS-CoV-2. The test method used to check the effectiveness of the highest class cleaning cloths is based on the EN 16615: 2015 standard. It is based on a quantitative assessment used to assess the bactericidal and yeasticidal activity on non-porous surfaces with mechanical action with the use of cloths in the medical area (the so-called four-field test). These wipes have different contents of polyester, polyamide and viscose in their structure, so as to ensure maximum absorption and collectability of microbial contamination with a minimum level of residual particles.
The technology of cleaning cloths for their safe use of wet and dry services with obtaining comparable results with the use of disinfectants.
Regular well planned disinfection is crucial for a quick response in the event of microbiological incidents. In the same time, well designed SOP’s for mechanical cleaning and high quality cloths will response in a optimum, economic and safe result for the processes and clean zones.