Steriline chosen as a guarantee of reliability
bess pro gmbh, a Berlin-based company part of the bess group, which manufactures and distributes “Made in Germany” high-quality devices and medical products, reached out to Steriline, a highly specialised manufacturer of complete lines for the aseptic processing of injectable drugs, to improve its volume of production and stabilising processes, with the aim of opening up further to international markets.
bess pro works on a range of packaging and Research & Development processes (including sterilisation, sterile packaging and secondary packaging) and on the innovation and further development of products in the fields of head & neck surgery, pneumology and gastroenterology, working on about 1,000 different types of medical devices and pharmaceutical products with very small batch sizes.
The client’s request included the replacement of manual and laboratory machines with more performing and reliable automatic solutions with an extremely small footprint. The choice fell on Steriline mainly because of the company’s specialisation in small output machine production for complete automatic lines, including washers and depyrogenation tunnels. The two companies started working successfully together with the aim of radically enhancing bess pro’s existing manufacturing processes, and they succeeded.
The request for an extremely accurate solution
bess pro’s brief to Steriline included a new complete line containing a Rotary Washing Machine (RA-V4), a Depyrogenation Tunnel (ST0), a new Powder Filling, Stoppering and Capping Machine (PVFCM50) under Laminar Flow, all equipped with customised specific adaptations.
The most meaningful challenge was accuracy: the client needed to manufacture small batch sizes at reasonable costs, considering the limited resources, always clearly meeting international regulation requirements for medical devices and pharmaceutical products (e.g. FDA and GMP).
The RA-V4 is designed to process vials & ampoules with a capacity of up to 7,200 pcs/h using intermittent motion. All fluid-processing elements in contact with container interiors are made of AISI 316L stainless steel. Other elements, such as the frame, shafts and bearings, are AISI 304 stainless steel. Glassware is loaded onto a rotating table, where each piece is automatically picked up by pincers and repositioned for optimal cleaning and draining effects during its passage through the washing and drying stations. These stations are equipped with lifting needles for glassware penetration where the appropriate washing fluids and compressed air are sprayed. After washing and drying, glassware is automatically discharged onto the sterilisation tunnel conveyor belt. The integrated control system, which includes PLC and HMI, automatically controls all the machine’s functional parameters, according to various glassware sizes and types. Parameter data are stored in different menus, password protected and accessible only by supervising and authorised personnel.
The ST0 is the smallest laminar flow depyrogenation tunnel currently on the market. It has been designed to depyrogenise vials, ampoules, cartridges and other glassware, with a continuous process maintaining an ISO5 environment throughout the length of the tunnel. It consists of three chambers. The inlet chamber, which has a laminar flow unit to ensure the clean transfer of glassware from the washing machine to the hot chamber, dries and preheats glassware, protecting it from the hot air back-flow coming from the hot chamber; the hot chamber sends glassware to the thermal cycle unit for depyrogenation; the cooling chamber cools glassware to a temperature suitable for discharging into the sterile room or isolator. ST0 is compact in design to fit into even the tightest production spaces, as specifically requested by bess pro, and it is particularly suitable for research and development laboratories.
Due to their compact design, the Rotary Washing Machine and the Depyrogenation Tunnel with Laminar Flow Hood have extremely small footprints (approximatively 1,500 x 2,900 cm), fully satisfying the client’s initial request.
The design of the PVFCM50 with Laminar Flow Hood takes into consideration the newest requirements of the filling process, including in-line transport and small width, reducing the volume to be monitored and sterilised, and making any point of the machine reachable, from the operator front, through gloves. Additionally, tight mechanisms, actuated from the mechanical volume, fulfil the closed RABS and isolator tightness requirements; the rotating table is designed to easily achieve the unidirectional and laminar air flow, reducing the presence of particles on the table. Continuous monitoring of the viable and non-viable particles is provided, together with a 100% IPC (In Process Control) of the weight and a weight-checking system with feedback to the powder filling station. The stoppering process is performed by a vacuum-assisted Pick & Place system and the capping is performed by a particleless rotary blade system. A sensor detects the presence of stopper and cap and consequently the machine rejects the un-stoppered vials and vials with nonconforming product weight. Steriline PVFM can handle up to 200ml vials with minimal format changes and production speeds of up to 200 vials/min, according to vial size and filling volume.
The product for which bess pro needed a highly accurate dosing process implied the extremely gentle handling and dosing of powder for vial filling. Steriline designed and built a special Auger Filling Head, equipped with a customised screw shape added to the PVFCM50, which allowed the extremely gentle handling of the product and the protection of its integrity. In this way, the extraordinary accuracy requested for this specific filling process could be achieved without compromising the very sensitive product in any way while handling it. Proving the Auger Dosing System was suitable for the client’s purposes and product processing was the main issue faced all along the project. Several trials at Steriline Lab were crucial to prove the proposed solution’s reliability and safety. Dosing tolerance checking consisted in finding the achieved level of accuracy given a specific dosing scale. As the requested accuracy and tolerance were very tight, the Powder Filling Machine was equipped with a 100% weight check system. During one week of trials, practically testing vial filling with Auger Filling Heads of several different sizes, hundreds of samples were produced to assess product stability. They were all in the dosing range for accuracy criteria and, in the end, the results unexpectedly showed that the new Auger Dosing Head was far more accurate than even the product currently running in the bess pro production line.
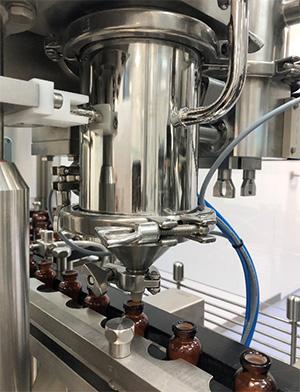
Fig. 2 – Steriline’s new Auger Dosing Head, specially made for bess pro
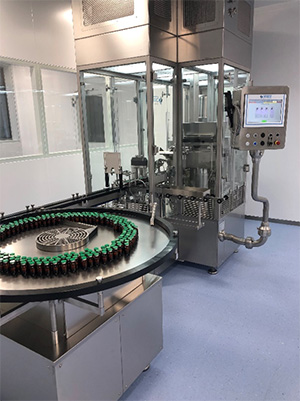
Fig. 3 – Steriline’s powder filling machine with outlet accumulation table
Thanks to this solution, the production of small batch sizes was possible while always keeping average consumption and purchase costs low. The previous semi-automatic filling process has been completely automated, and glass vials are washed and depyrogenated. The entire line cycle could run automatically, alone, without any human intervention. Furthermore, the process has been demonstrated to be GMP-compliant and the output, in terms of production, has been significantly increased.
The whole project, from the order to line installation, started with technical discussions, pre-testing and trials, until the order placement phase, lasting approximately 10 months.
A turnkey line, immediately fully operational
Several reasons led bess pro to choose Steriline as its supplier besides the need for very small equipment to fit into a limited number of available cleanrooms. The Italian company could meet this requirement (since it usually provides the smallest machines in the market) but, above all, it can provide a turnkey, fully operational line. The line was supplied ready to perform at full capacity, including training and validation assistance. This turnkey complete package, including the first year of maintenance, was the most important reason behind bess pro’s decision to purchase the Steriline project and development proposal.
Experience was another key element. Considerable experience is needed for the manufacture of performing powder-handling machines, and Steriline has been doing this for a long time. The Italian company also looked at the customer’s complete packaging process, connecting the entire line with secondary packaging equipment, thanks to a special belt system and rotating tables acting as a buffer system for vials.
Even if the entire process was slightly delayed by the COVID-19 emergency, Steriline provided two alternative solutions for Factory Acceptance Test (FAT) virtual procedures, available in live streaming mode or also recorded and released later for client revision and approval. Despite this, after lockdown and the first wave of coronavirus in Italy, bess pro customers felt confident in doing FAT tests in person, not virtually, for one week in Como.
Last but not least, language played a key role too. Having German- and English-speaking engineers, project managers and sales managers helped create a stronger relationship with clients from Germany, avoiding cultural barrier risks.
This complete package, ensuring extremely good quality, also came at a very affordable price.
“Without Steriline, we would never have been able to implement our optimal cleanroom production layout. No matter whether longer, shorter, rotated or mirrored, the engineers at Steriline were tireless in adapting their modules to tailor the line to our production layout without generating a cost driver. No competitor came close to showing such flexibility. The collaboration with the Steriline project team was incredibly motivating and always responsive and solution oriented. It is therefore hardly surprising that this project was completed without any significant delays, despite the pandemic,” said Sven Lange, Project Manager at bess pro gmbh.
“Steriline stood out from the crowd as early as the supplier selection phase, with its fast and binding communication, and during the entire project it never let us down in this sense. In particular, special customer-oriented solutions, such as a special receptacle for the powder hopper, in order to integrate specialised upstream manufacturing processes of the drug substance, were implemented excellently. I am already looking forward to future projects with Steriline!” said Martin Gördes, Chief Technical Officer at bess pro gmbh.
“The R&D area is very challenging with clients asking for support when there are new drugs to develop. And sometimes language can be an obstacle, above all when working with German clients who prefer to have a German-speaking point of contact. We usually work to customise our standard solutions or to develop new ones following specific requirements, and this was exactly the case with bess pro,” commented Mirko Ebeling, Managing Director at Ebetech GmbH, Steriline Sales and Service Organisation for German territory.
“Thanks to the close collaboration with bess pro’s team, we successfully developed tailor-made solutions, as happened for the Auger Filling Head. This experience in particular showed the key importance of trials in the pre-sale phase, proving Steriline Lab’s effective approach to ensure the most appropriate solution in terms of process reliability,” added Stefano Albusceri, Project Manager at Steriline.