FAB Airborne Molecular Contamination (AMC) monitoring and detection is typically performed by a single, stationary unit that attempts to stringently monitor contaminants within a defined radius around its fixed location on the FAB floor.
In order to cover all critical areas within the FAB, multiple stations must be tactically deployed to map the entirety of the desired clean area.
Cross-contamination can occur from various sources, including equipment, personnel, and airborne particles
However, do these immobile devices truly tell the entire story of what may be happening in an environment as sensitive and dynamic as a FAB?
In what follows, we introduce a novel technology that can be nested inside a FOUP (Front Open Unified Pod) and shuttled around the FAB that will revolutionise the current model of stationary sensors for FAB AMC monitoring.
The delicate FAB environment and cross-contamination?
Monitoring a FAB or semiconductor cleanroom is no easy feat. In an environment where the slightest imperfection can cost dearly in scrapped wafers and lost FAB time, fabrication facilities take the utmost precaution to ensure pristine manufacturing conditions.
Cross-contamination can occur from various sources, including equipment, personnel, and airborne particles. More specifically, the FAB environment’s intricate gas-phase molecular makeup may be easily compromised by airborne molecular contaminants, leading to costly declines in wafer quality and quantity.
AMCs include a variety of gasses, vapours, and particles that can cause defects in microelectronic devices
AMC can also pose an occupational hazard to personnel health within the FAB environment, which bears additional moral and economic implications.
AMCs include a variety of gasses, vapours, and particles that can cause defects in microelectronic devices. Fortunately, by utilising extremely fine air filtration, controlling the airflow within the FAB, and following strict cleanliness operating protocols, FAB managers can minimise AMCs so that silicon wafer yields stay high. But as technology nodes for more advanced chips shrink, their tolerance for contamination becomes even lower.
Consequently, the need for early detection and swift neutralisation of the contamination source(s) in the FAB cleanroom environment are the two prevailing missions that keep quality supervisors up at night. In other words, these are the two crucial cleanroom tenets to prevent contamination’s costly economic impact in time and material.
The advantages of an OHT-borne superway analyser
To minimise human presence and intervention within the delicate FAB ecosystem and to accelerate and streamline FAB operations at scale, the Overhead Hoist Transport (OHT) network is used to shuttle wafers and other materials between different processing stations via grid-like transit tracks lining the cleanroom roof (Figure 1).
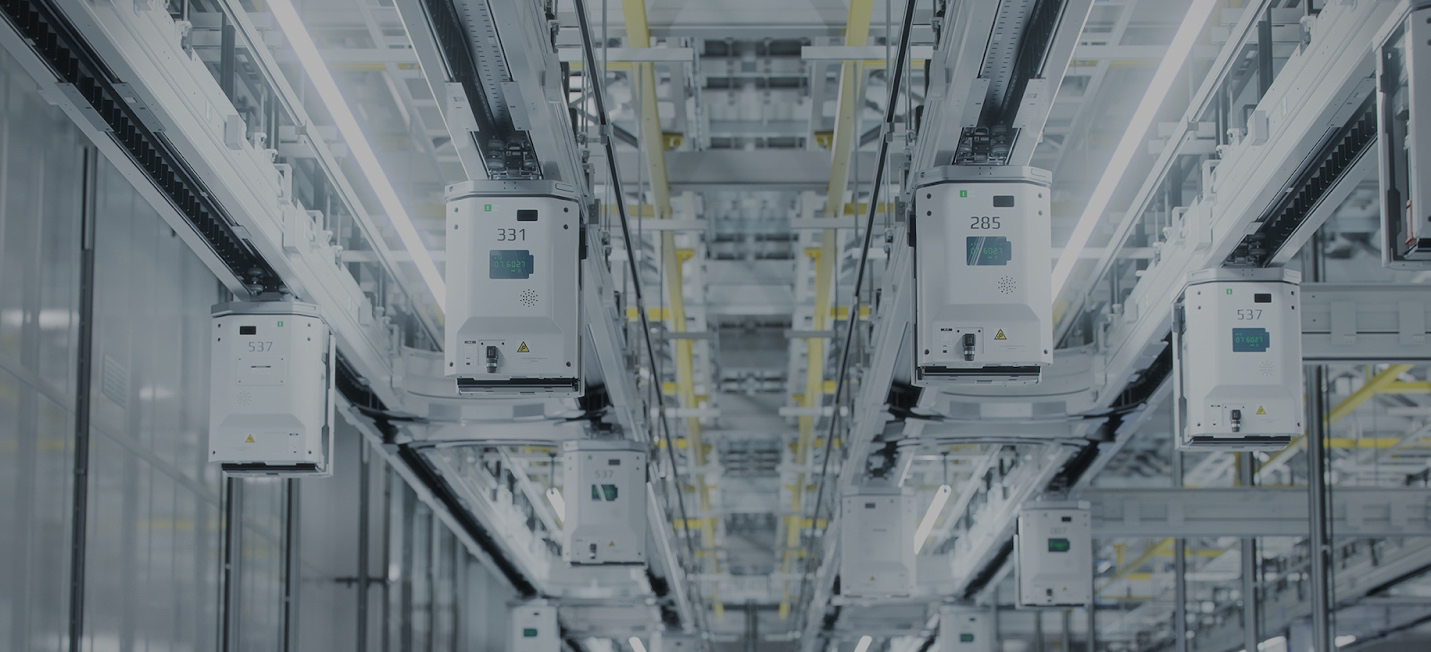
Figure 1: OHT cars in circulation via the overhead tracks’ extensive network covering the FAB area.
These grids are reminiscent of an impeccably time-coordinated subway transit system, which is effectively a “superway” transit network, by virtue of its overhead location. And here lies the new opportunity!
The Overhead Hoist Transport (OHT) network is used to shuttle wafers and other materials between different processing stations via grid-like transit tracks lining the cleanroom roof
By exploiting the mobility feature of the existing superway and using a nested sensor inside the OHT cars and its network of tracks to canvas the entirety of the FAB facility lies a towering opportunity to disrupt the existing stationary AMC monitoring status-quo.
The core of this concept is the availability of a compact analyser with high-sensitivity and fast response time that fits right inside a FOUP (Figure 2).
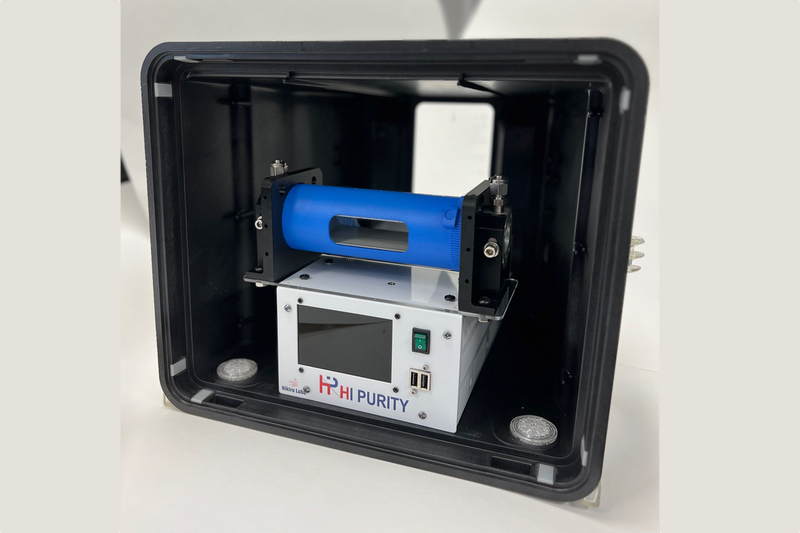
Figure 2: Nikira Labs FOUP Analyser
This analyser will then be able to monitor, detect, and report targeted gas-phase contaminants throughout the whole FAB facility.
This disruptive superway model will undoubtedly offer FAB quality supervisors the much-needed advance warning and actionable insight regarding the incipient AMC threat right when it occurs.
How does Nikira Labs’ technology fit into this superway model’s picture?
Nikira Labs’ OHT-borne analyser technology is based on Cavity Enhanced Absorption Spectroscopy (CEAS). CEAS is based on a closed or open path cavity with two opposing high-reflectivity mirrors (Figure 3).
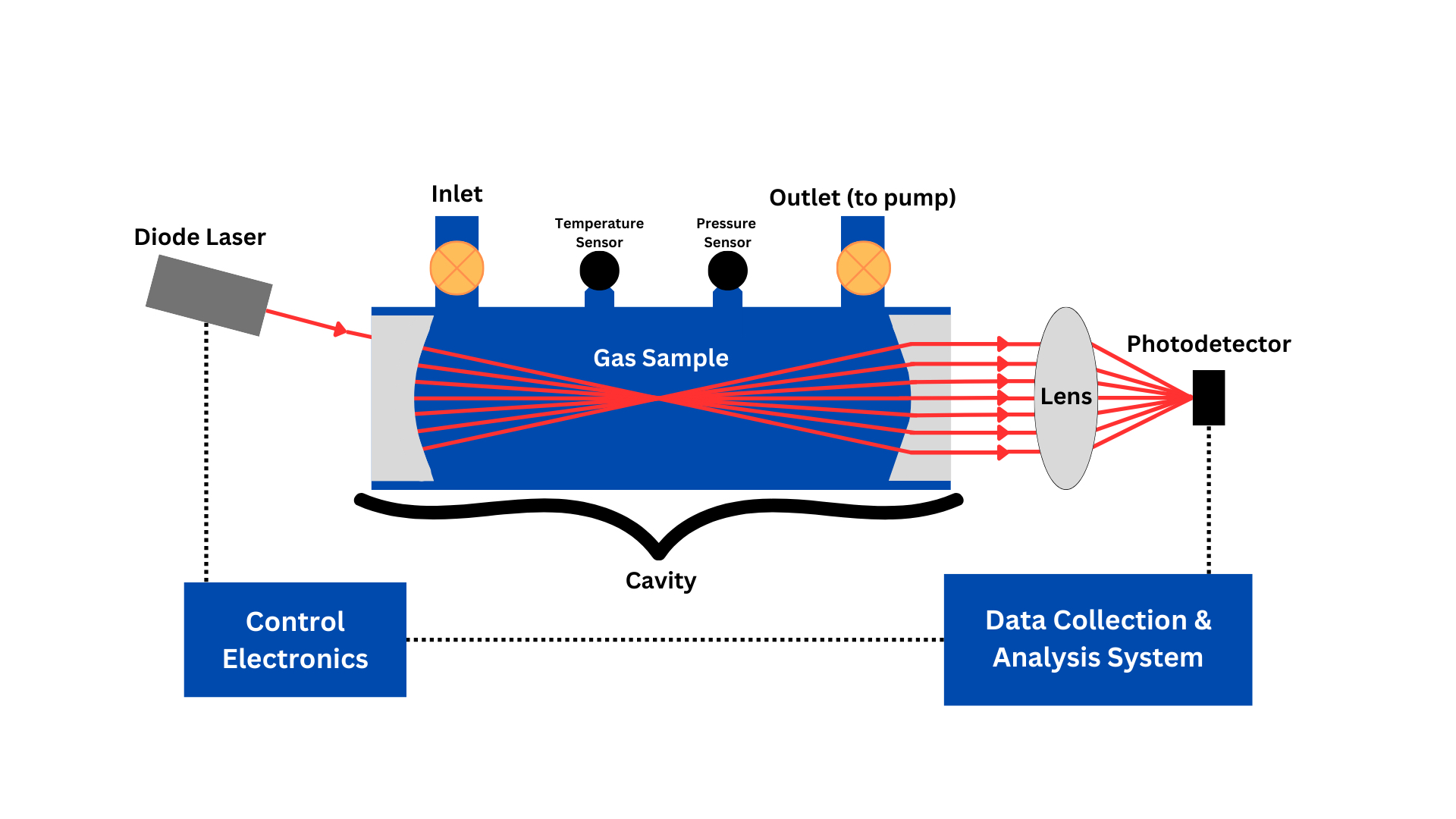
Figure 3: Schematic diagram of a closed-path CEAS-based analyser. The gas sample flows continuously through the cavity while the laser beam gets reflected ~10000 times between the two highly-reflective (~99.99%) mirrors before the laser light completely decays due to molecular absorption and leak through the mirrors.
The laser is located behind one of the two mirrors and the laser light is injected into the cavity through the front mirror. The leaked light from the cavity is measured by a photodetector positioned right behind the second mirror.
Advantage-wise, CEAS is less sensitive to internal alignment of components (e.g., mirrors) as well as variations in local temperature and pressure, and, most importantly, it is immune to vibration.
These grids are reminiscent of an impeccably time-coordinated subway transit system, which is effectively a “superway” transit network
As a result, CEAS is ideal for use in applications requiring mobility with its associated vibrations, such as OHT horizontal and vertical movements. It can also lend itself to an open-path cavity design option that minimises chemical species cross-contamination and increases the detection response time.
In the AMC monitoring case, these analysers utilise an open-path architecture and are designed to be ultra-lightweight with built-in WiFi and GPS. Their capabilities and performance achieve realtime mobile detection of contaminants such as ammonia (NH₃), hydrogen fluoride (HF), and hydrogen chloride (HCl), with high-sensitivity.
The open-path design minimises the use of wetted surfaces, hence, reducing the risk of sample carry-over (Figure 4).
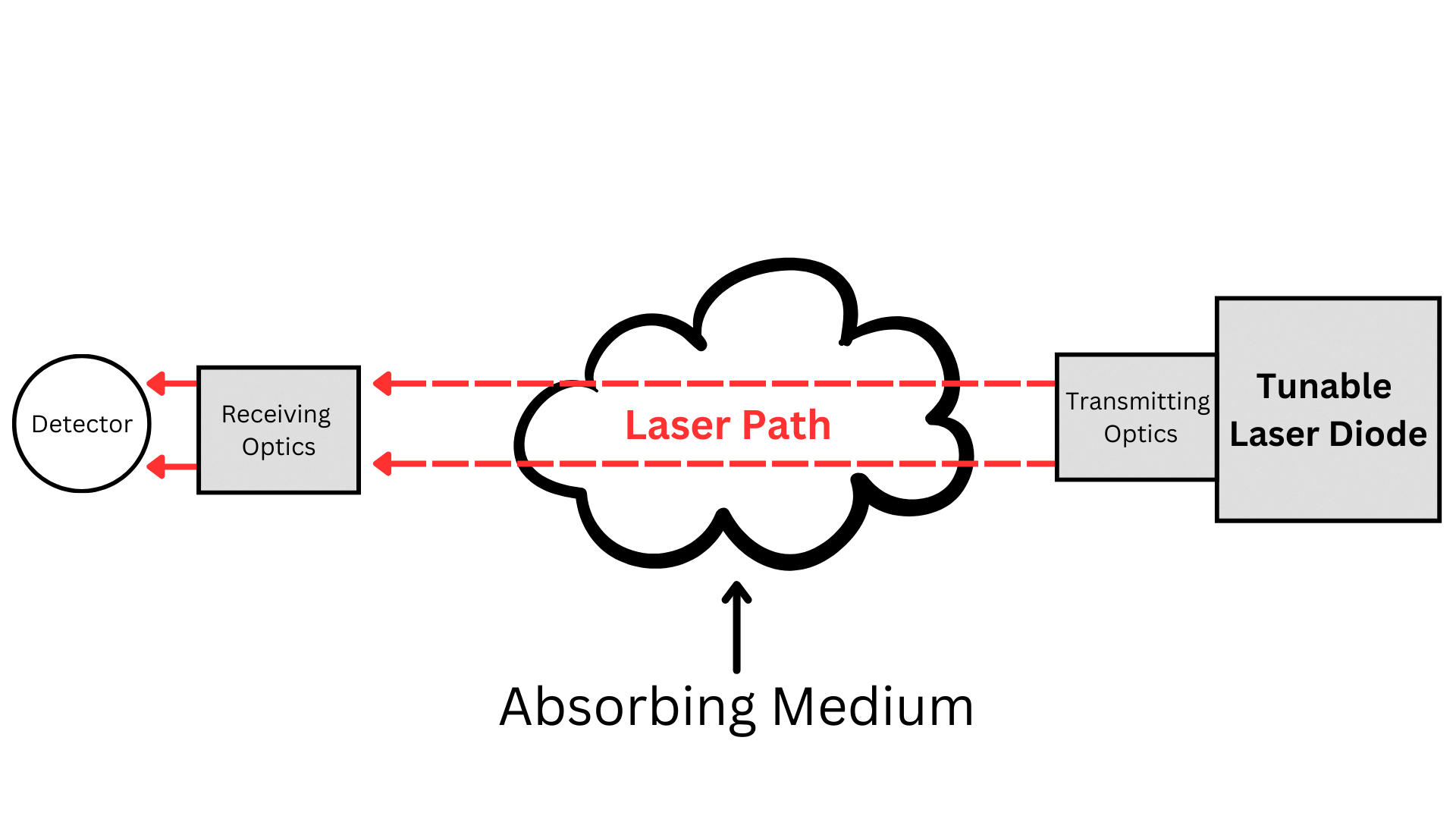
Figure 4: Stylistic open-path depiction of a laser spectroscopy-based analyser. In the CEAS case, the two highly-reflective mirrors (transmitting & receiving optics) reflect the laser beam between them ~10000 times.
This design is particularly effective against sticky contaminants adhering to the analyser surfaces. These analysers provide continuous, realtime monitoring with fast response time to instantaneously report detected contaminants as the analysers move throughout the fabrication facility.
These features (mobility, high-sensitivity, fast response time) ensure that any contamination can be promptly detected, reported, and addressed in order to maintain the FAB high-quality standards.
This disruptive superway model will undoubtedly offer FAB quality supervisors the much-needed advance warning and actionable insight
How do these advantages contribute to or do better than the existing AMC monitoring infrastructure? By integrating these laser-based open-path analysers and its mobility differentiator into the OHT system, the superway AMC monitoring model provides comprehensive high-sensitivity coverage throughout the whole OHT tracks network, in realtime.
It offers continuous data collection that allows for prompt identification and elimination of contaminants. Said data can then be integrated into the FAB’s collective monitoring system with implementation of the relevant informatics to generate predictive analytics.
Most importantly, these superway analysers are space and power efficient. They obviate the need for bulky and stationary stations with limited monitoring coverage across the cleanroom area. Most importantly, with fewer units, the laser-based open-path analysers scale up the AMC monitoring coverage of the cleanroom facility in its entirety without the costly redundancy of the current stationary systems.
Challenges and considerations
It should be no surprise that there is a wide variety of FAB AMCs to monitor for. As of now, the Nikira Labs OHT-borne AMC analysers are currently able to monitor for a targeted subgroup of these contaminants, as previously listed; however, this list is growing as engineering development progresses.
Moreover, with a variety of available customisations and adjustments, these OHT-borne analysers can be easily adapted to an individual FAB environment’s specific needs.
Technology is always evolving and advancing, and superway analysers are no exception to this
Of course, with all of the advantages offered by these OHT-borne analysers and their recency in the analyser market, there are challenges to face with the adoption of any new technology. As with all advanced technological hardware, these mobile analysers might need to be occasionally serviced.
As such, Nikira Labs knowingly built their analysers to be operator-friendly by design. This way, service can be conveniently performed onsite by the operator’s technical team. There also must be seamless integration with existing FAB operations and SCADA systems in order to make the superway implementation successful in every FAB.
Additionally, the high-density data collection rate necessitates the implementation of advanced data analytics to quickly process the massive amounts of data. Staying on top of this would allow FAB managers to predict contamination events, optimise monitoring, and execute intervention protocols to address any contamination.
Future trends
Technology is always evolving and advancing, and superway analysers are no exception to this. More compact analysers with an increasing list of targeted contaminants alongside the utilisation of AI/Machine Learning to predict contamination events and optimise FAB space monitoring are all goals within reach in the near future.
On-ground autonomous robotics hauling these analysers around the FAB floor in tandem with the overhead superway system are also set goals on the roadmap.
Conclusion
Overall, the superway analysers mobile AMC monitoring model is the future of FAB quality and yield enhancement. Compared to previous methodologies, the superway model is a disruptive advancement in contamination control technology given their mobility, fast response, and elimination of redundant fixed monitoring stations. With these superway model’s salient features, FAB quality managers will maintain the stringent quality standards required in semiconductor manufacturing, but with advance warning, use efficiency, and actionable insight.
Top image: The superway overhead transit line