For many years, bacterial extraction from within cleanrooms has relied on what has been the most advanced form of technology available – High Efficiency Particulate Air (HEPA) filters. Such filters have been the industry standard in cleanroom air purification and for the best part of 50 years have done a comparatively efficient job, within their obvious constraints. They capture dust and bioburden, including germs, down to 30 nanometres (nm) in size.
However, the germs are not killed. They remain as viable particles in the filters until the filters are removed and disposed of. As a result, the filters must be replaced frequently to maintain their expected performance. As soon as a new filter is put into action, it starts to collect particles and clog, thus the performance begins to decline. Filter replacement needs to be carried out with the utmost care to prevent any collected, still viable particles from being released back into the cleanroom, where they could re-pollute the air and compromise the results or work being carried out in the facilities.
The disposal of the used filters is highly regulated, complex and adds costs. An additional consequence of the filter replacement work is that sensitive work samples must be removed from the cleanroom, which means that not only are operations interrupted but after the filter replacement there is a waiting time before the air in the room is clean enough for operations to restart. This cleanroom downtime can cause disruption to operations and increases operational expense. Technology has moved on, however, and today new equipment is available, that has been independently tested since 2001, and proven to perform in 20 or more countries for various customers, including cleanrooms.
Genano technology enables all contaminating particles and gases to be removed from cleanrooms on a permanent basis – while killing any bacteria and viruses rather than simply capturing them. The term “all” alludes to the fact that the new machines will kill and remove all viable particles down to 3 nm, something that filters alone cannot do. Below 3 nm, the particles lose their molecular structure and therefore cease to exist.
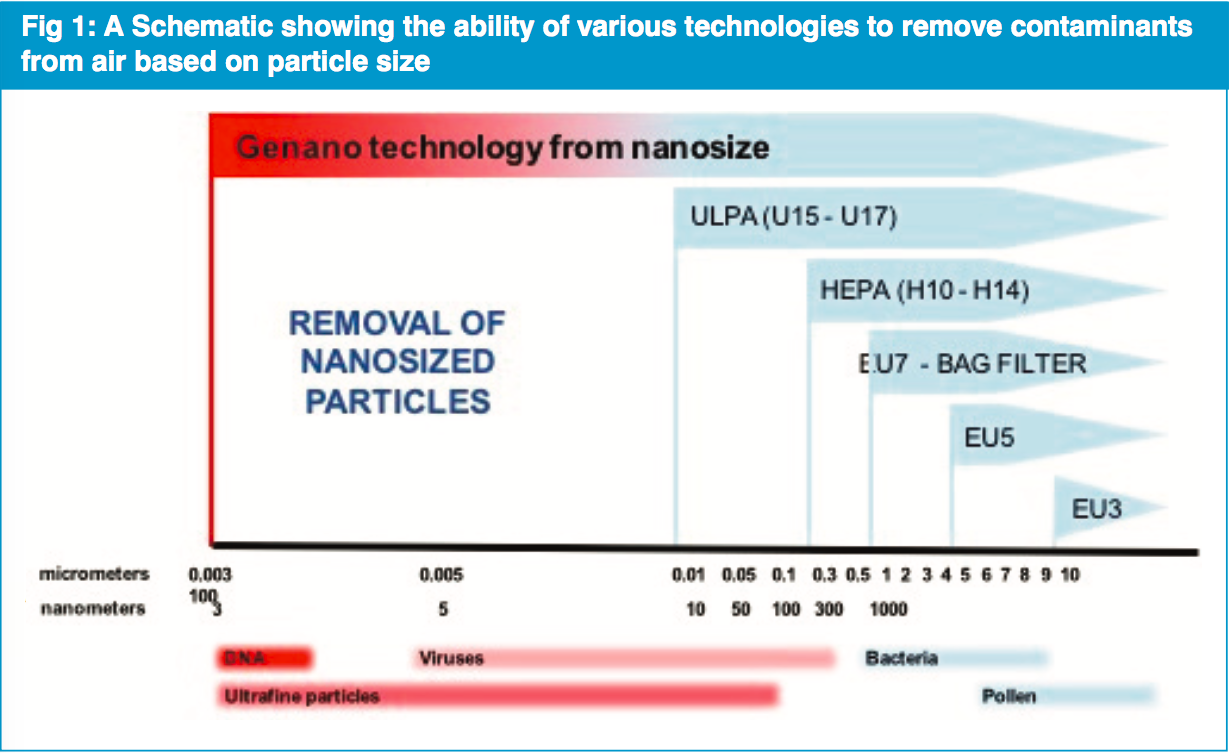
The process that kills those particles is ionisation. Inside the machine is a central core which emits negative ions into the incoming air, charging all the particles negatively and because the internal wall of the machine is infused with positive ions, it catches the particles and renders them lifeless.
There are a significant number of harmful particles at the lower end of the size spectrum – between 3 to 30 nm – that can be eliminated and removed, along with the larger-sized particles. As well as removing nano-sized particles from the cleanroom air, in comparison to the removal of filters, there is no risk of them escaping back into the cleanroom.
The technology was developed in Finland over 25 years ago, by the Finnish state technology research centre, university and occupational health authority. Since commercialising the completed invention, the machines have been operating globally and have seen application in many different types of laboratories, IVF clinics, hospitals (operating theatres, isolation rooms, intensive care units) as well as in the fast growing market of educational classrooms (see applications panel opposite).
Following the introduction of Genano machines into UK laboratories, figures showing up to an 80% reduction in bacterial contamination levels, in comparison with the existing methods, have been recorded.
There is no structural alteration needed to accommodate the machines and they make few demands on the environment.
The portable “plug and play” Genano machines are on wheels, enabling them to be wheeled into the facility. To fill the washing liquid container, they simply need to be plugged into the electrical socket and switched on. Using the same amount of electricity as a 90-watt light bulb, they have a very low impact on the facility’s carbon footprint.
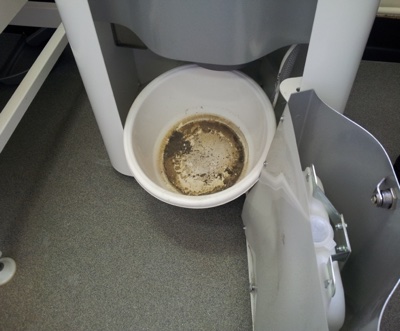
Maintenance for Genano technology comprises refilling the washing liquid container on average once a month or once a quarter, depending on the machine size selected
Maintenance and costs
Compared to the regular and elaborate requirements for filter replacement, the entire maintenance ritual for the Genano technology comprises refilling the washing liquid container on average once a month or once a quarter, depending on the machine size selected. The units automatically carryout a rinse on a weekly basis and leave no toxic waste.
The annual service required includes power cleaning the unit inside and replacing the carbon plate, which collects the gases (also removing smells from the room). No particles are stored in the carbon plate.
The annual service takes one person approximately two hours and the work leaves no toxic waste. For servicing, the unit can be rolled out from the cleanroom so there is no interruption of the operations.
With traditional filter-based solutions for cleanrooms, structural HVAC work needs to be implemented during the initial facility build. The HVAC systems are usually built into the fabric of the cleanroom structure and often are linked to the HVAC system of the entire building.
These indirect costs of building work are usually not included in the actual air purification costs and normally fall into another budget/expense line rather than the cleanroom operational budget. Therefore, the operation budgets for filter based air purification solutions often do not reflect the whole costs.
Size matters
One of the challenges that many cleanroom users currently face is the limited measurement technology available for recording the smallest, nano-sized particles contaminating the air. There are sophisticated devices on the market able to do the job but those devices are very expensive, and most investment budgets are tight.
Consequently, there is a gap in the market that can be filled by service providers able to help in dealing with such nano-size particles.
Examples of in-use applications
Removing contamination from within a research centre
Scottish Universities Environmental Research Centre (SUERC) had problems with air quality and contamination. With Genano, the total amount of VOCs in the air went down to one third, solving the contamination issue.
Air purification in a molecular diagnostics company
Mobidiag develops and manufactures molecular diagnostic kits for detecting human pathogens.
The challenge was removing PCR amplification products (DNA) from the air which could otherwise contaminate products, leading to false positives.
New cleanrooms were built with Genano and the laboratory has now two ISO 6 compliant areas.
Reducing contamination in a PCR production company
For Finnzymes, with laboratories involved in DNA research, analytics and diagnostics production, Genano prevents airborne particles from spreading to products and processes in open vials.
Protecting haematology patients in Polish regional hospitals
Genano has delivered a total of more than 150 air purifiers to Polish hospitals responsible for haematology and oncology.
They are used to protect immunosuppressed patients after bone marrow transplantation.
Protecting new life in fertility clinics
Oocytes (egg cells) and embryos are very sensitive to air contamination before implantation. Genano air purifiers are used at a top fertility clinic to further purify HEPA-filtered air in premises where in vitro fertilisation (IVF) is carried out.