Scientific modelling of fluid mechanics systems, dubbed computational fluid dynamics (CFD), is a well-established analytical method and used in many industries: from streamlining the flow of air over a car bonnet to investigating the bubble behaviour in membranes. Surprisingly, the application of these techniques to packaging validation has, until now, been neglected.
A team from Baltimore Innovations, working with a counterpart at the Oxford University, has now developed a series of CFD models that accurately predict the behaviour of desiccants (drying agents) within pharmaceutical packaging, with the aim of reducing the time spent performing validation trials in the lab. This means that SMEs and multinationals alike can reduce the time taken to get their product to market.
Desiccants play a vital role in the protection of moisture-sensitive drugs. By removing water vapour from the air, they prevent premature degradation and can enhance the shelf life and stability of formulations.
Limitations of current validation methods
Up until now, the practice of desiccant selection has considered the total moisture load for the required shelf-life of a packed product (a combination of initial water vapour included into sealed packaging, plus the vapour ingress through the boundary of the packaging, expressed in g/m2/day).
This total mass of moisture is then compared to the given desiccant's absorptive capacity to determine the total mass of desiccant required. Such a simplistic approach has then always required a great deal of lab trial verification work because what the initial theory has suggested had not always been what transpired.
The disconnect between simple paper-based calculation and observed real-world lab results is due to several kinetic factors within the packaging
The disconnect between simple paper-based calculation and observed real-world lab results is due to several kinetic factors within the packaging. For example, as the desiccant reaches saturation, the rate at which it pick-ups moisture decreases. Therefore, even though the desiccant is still "active", the humidity inside the package will increase. The increase in humidity places the packaged product at a greater risk of hydrolysis.
The new more advanced method developed by Baltimore Innovations accounts for changes to both the rate of ingress of moisture — which will decrease as the internal humidity increases — and the rate of moisture adsorption of the desiccant.
The balance between these factors is critical to the outcome, and the software has been rigorously and iteratively bench-tested versus real-world test data, so as to improve accuracy to the level where it can now reduce verification work by 50%.
Predictive approach to validation
The analysis carried out to develop this new predictive validation system for desiccants is based on sophisticated mathematical models and extensive research alongside experimental tests carried out to develop a comprehensive understanding of desiccant adsorption behaviour in a variety of storage environments and packaging.
The storage environment is defined by the temperature and relative humidity (RH) of the air, which will give the absolute humidity.
The software has been rigorously and iteratively bench-tested versus real-world test data
The packaging includes aluminium foils of different thickness and vials that might be employed for pharmaceutical applications.
The model can be applied to any desiccant-based packaging system used for applications such as the protection of pharmaceuticals, vitamins, diagnostics kits, medical devices and healthcare products, as well as large-scale "work in progress" containers.
Desiccant-CFD modelling
Once the desiccant behaviour is known, this can be coupled with existing fluid mechanics knowledge, creating a desiccant-CFD model that takes into account the advection and diffusion of water molecules, within a sealed environment.
The model is then related to the performance of the desiccant over time: as the desiccant absorbs moisture, the number of adsorption sites will decrease, hence the probability of a water molecule being adsorbed at any given time will decrease at a given relative humidity.
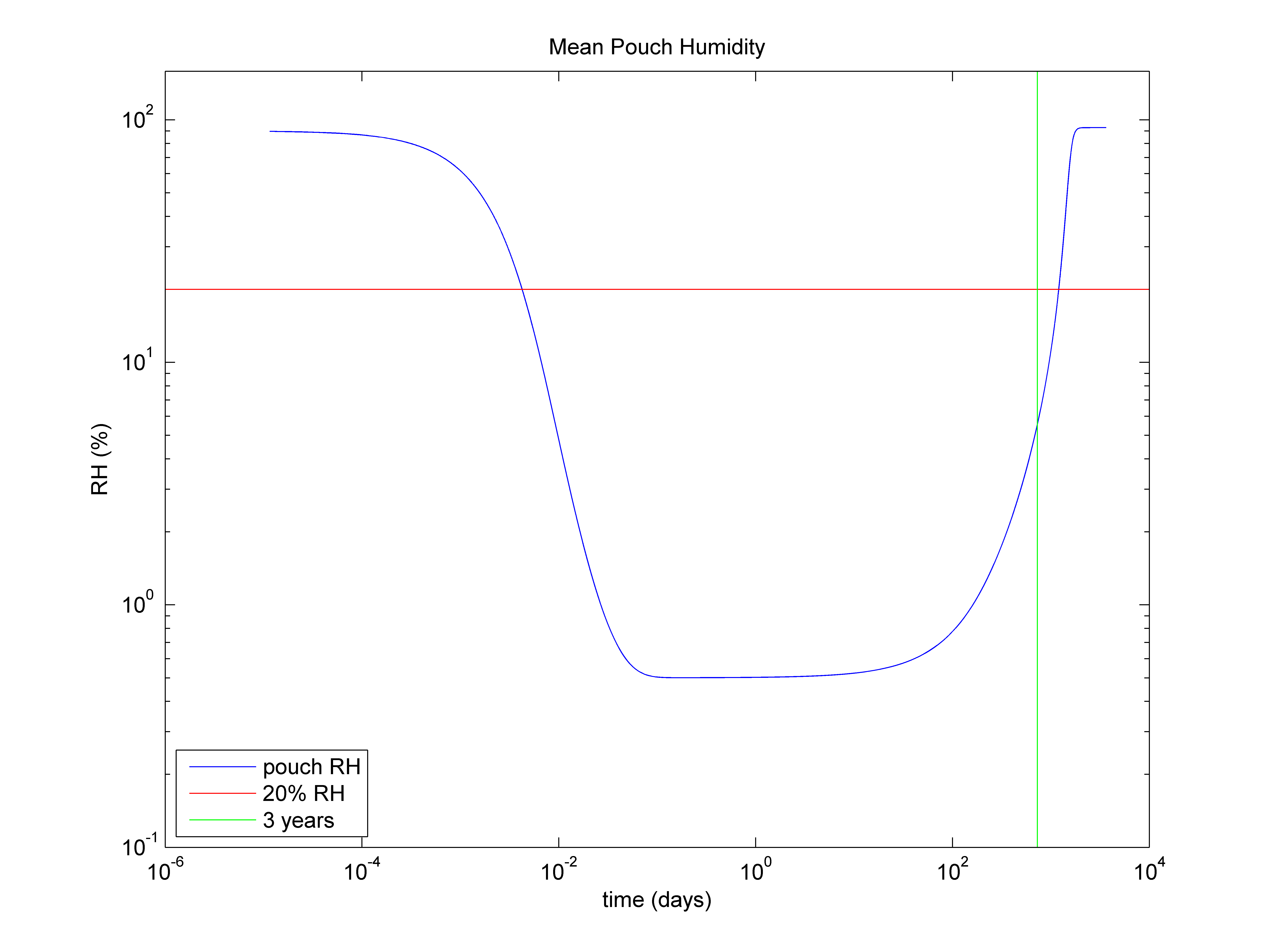
Figure 1 - Average humidity inside a foil pouch for the active lifetime of the desiccant
Understanding the performance over time is an important consideration as it determines the rate at which the desiccant picks up moisture. As the desiccant approaches saturation, the rate of moisture adsorption will become much slower. Eventually, a tipping point will be reached where the partially-saturated desiccant will not be able to keep up with the moisture entering the package. At this stage, the humidity will start to rise, even though the desiccant is still "active". See figure 1 for reference.
Mapping the humidity
The interior of the package in the desiccant-CFD model is represented as a Cartesian or cylindrical grid depending on its geometry. The ingress-diffusion-adsorption equations are solved over the grid points, giving a 2D or 3D view of the humidity inside the package. These are progressed over each time step for the required shelf-life of the product. Thus, the humidity for any given point inside the package can be determined for any time throughout its shelf-life.
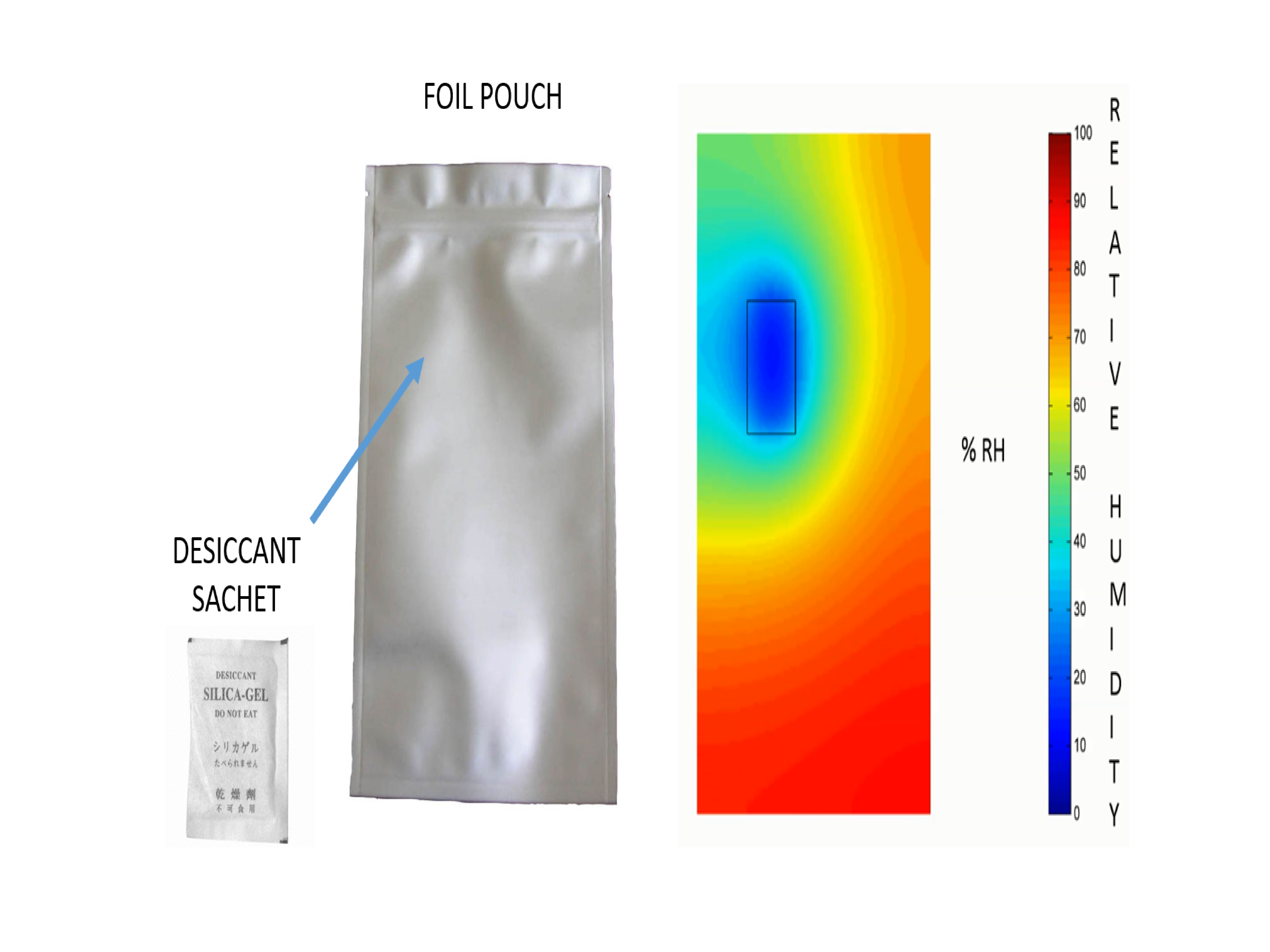
Figure 2 - Humidity map inside a foil pouch with desiccant
This knowledge is especially powerful when minimising the work and costs associated with getting a product to market, as shown in Figure 2.
Performance in practice
With this method, a snapshot of the result of modelling the humidity inside a typical effervescent tablet vial can be obtained (see Figure 3). Here, the desiccant is in the lid at the top of the vial. As such, the desiccant will remove moisture from the top first as illustrated in the graphic.
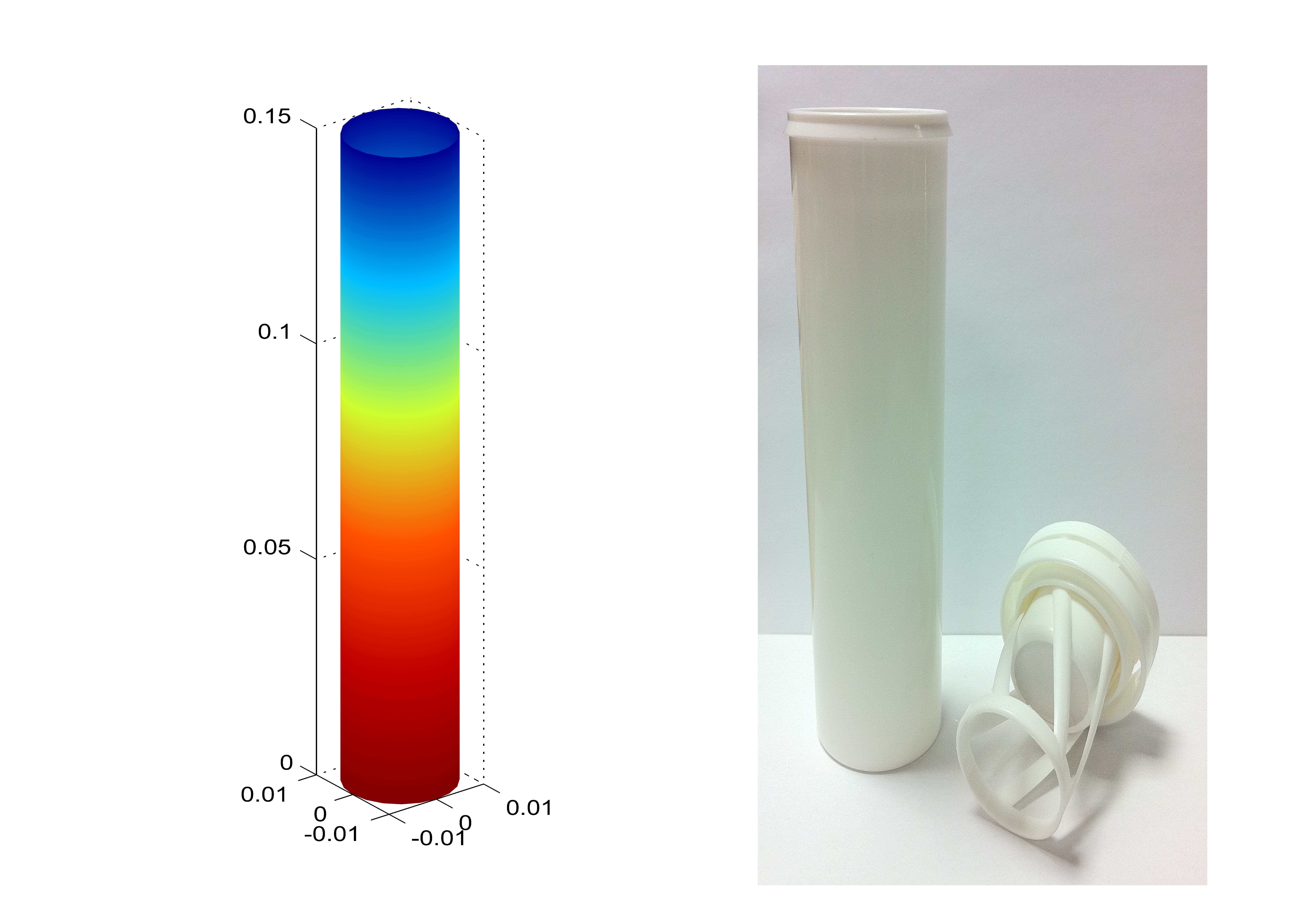
Figure 3 - Humidity gradient from top to bottom of tablet tube
In practice, vials can be repeatedly opened and closed over a significant amount of time as the consumer removes each tablet one at a time. And this raises the question: what effect will repeat opening and closing have on the actual product shelf-life?
A product may be designed to perform satisfactorily while closed in terms of shelf-life, but may fail if repeatedly opened in a humid bathroom: when opened, the desiccant in the lid will be exposed and the vial headspace filled with humid air.
The flexibility of the 3D model allows the effects of regular opening and closing of the package to be considered. This will ensure the quality of the product remains until the last tablet is removed.
Using the 3D validation software developed by Baltimore Innovations offers significant benefits to companies, especially SMEs who often don't have in-house packaging expertise. These benefits include lowering desiccant costs by eliminating excess usage; improving shelf-life and performance by better desiccant selection and placement; and reducing packaging bulk volume and weight for lower packing and transport costs.
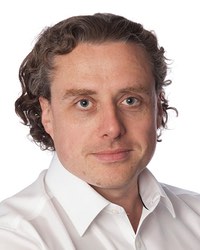
Dr Mark Valentine
About Dr Mark Valentine
Dr Mark Valentine joined Baltimore Innovations after completing his PhD at Oxford University, where he worked in the Chemical Engineering Group in the field of ‘Fluid Mechanics and Multiphase Flow’.
In his current role as R&D Director, he works closely with the in-house business development team, strategic manufacturers and key supply partners to develop new moisture control-related packaging products.
Valentine also provides desiccant consultancy advice and technical support to customers within the pharmaceutical, medical device and food packaging industries.
N.B. This article is featured in the February 2020 issue of Cleanroom Technology. Subscribe today and get your print copy!
The latest digital edition is available online.