Contamination control is of great importance to healthcare facilities and to pharmaceutical cleanrooms.1 Specifically, the control of non-viable particulates and viable micro-organisms within pharmaceutical cleanrooms is necessary to minimise risk to product quality during routine manufacturing.
Typically 80–90% of normal micro flora identified within a cleanroom environment is affiliated to humans.2 Therefore, strictly controlled change procedures and the use of appropriate cleanroom quality garments, among other controls, are required to help reduce this route of contamination ingress.
Regulatory guidelines advising on the suitability of garments for the various cleanroom classifications include:
- EudraLex, Volume 43
- International Standard ISO 14644-4:2001(E) Annex A4
- Rules and Guidance for Pharmaceutical Manufacturers and Distributors, Annex 15
- 21 CFR 211 (b)6
When a cleanroom operator is due to start any aseptic gowning process, it is paramount that the correct size garment (coverall, hood and overboot) is available on each occasion. This removes any potential for the user to take a poorly fitting garment that could increase the risk of contaminating the clean environment. The management and control of all aseptic gowning inventories, therefore, must commence well before the operator dons a cleanroom garment. Among the aspects to be considered and managed are:
- The supply, storage and rotation of stock
- The availability of the correct size and type of gowns at all times, at all storage locations
- Effective and ‘in date’ operator training, i.e. operatives must be assessed regularly
- A defined process of how to handle damaged garments and a documented maximum number of washing cycles and repairs.
Gowning philosophy
Prior to commencing a new garment contract with a supplier, companies should generate and approve their own Garment Philosophy document. The recommendations for gowning contained in the document are based upon the following information:
- Regulatory guidelines
- The risk of microbial and/or particulate contamination from the process stream
- The classification of the cleanroom area
- The operations conducted within the cleanroom area
- The level of risk to personnel
As part of the philosophy, a detailed entry profile can be built up to calculate accurately the required number of garments needed to support routine processing. It is important not to overestimate the required amount and to focus on having lean inventory levels supported by frequent delivery/collections in place. This will ensure garments do not lie idle in used laundry bins post-use. A sizing exercise should also be performed at this stage to ensure the correct distribution of sizes is delivered.
Supplier relationship and support is key at the start and throughout the contract, so as to be able to manage and control inventory levels effectively. Individually coded garments can be trended in terms of usage. A number of suppliers offer ‘usage data’ in the form of over- and under-processing. With this data, garments that are being over-processed may indicate a shortage and companies may want to add more, whereas garments that are under-processed may indicate that there are more garments than required and some inventory could be removed. This data may be delivered as a formal report that can be reviewed routinely (quarterly) in conjunction with the supplier to adjust stock levels.
Routine analysis of the data is important to confirm garments are being utilised in accordance with procedure. Typically, overboots (if wrapped singly) should have double the usage of coveralls, whereas hoods and coveralls should be roughly comparable (see Figure 1).
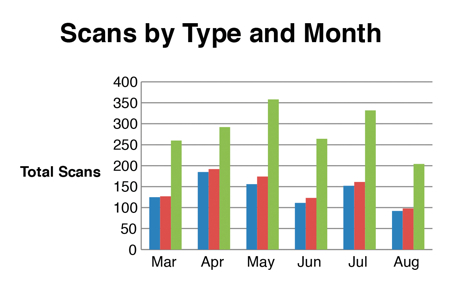
Figure 1: Vendor usage report showing scans by type and month
Instructions on aseptic gowning procedure benefit from being provided in visual form, ideally with step-by-step photographs on a single page, clearly demonstrating the requirements of the technique. A copy of this page, issued by the Document Control group, can be useful if displayed within the change area as a single point lesson. The use of photographs is of particular benefit when escorting visitors through the gowning process as well as providing a reminder of the technique requirements for routine personnel.
Where there are multiple manufacturing areas, consideration should be given to a single gowning procedure that covers the aseptic gowning requirements for all classified areas. Where this is not practical, it should be split per classification. Having an amalgamated SOP (i.e. gowning for the ISO 8 areas) can prevent variation spreading between areas.
Storage and stock management
It is recommended to make regular stock checks on an annual basis to ensure stock levels are consistent throughout the tenure of the contract. In addition to routine stock checks, further sizing exercises should be performed (preferably by the supplier) at specified intervals (e.g. 18 months) depending on the staff retention rates. This will ensure that any new starters and also any shift in the sizing requirements are accommodated.
Incoming garments may be stored in a Central Incoming Store that must have clearly defined areas. This storage area must offer the facility to store all garments off the floor and in a dry condition at all times. A First in First Out (FIFO) system should also be maintained, with the outer wrapper of all incoming garments being sanitised prior to storage.
The incoming storage area should be routinely cleaned and all incoming garments checked to confirm their sterility (if required), that the wrapping is integral, complete and all garments are within their expiry date (each garment has a maximum shelf time/expiry date of typically 12 months from the date of wrapping the garment).
Within the central storage area (and any satellite storage areas) it is imperative that incoming stock does not stagnate. There are practical ways to ensure that the stock can be rotated – for example, splitting the central storage area into two sections: Section 1 holds stock delivered in the first six months of the year and Section 2 stock delivered in the second part of the year. Any stock left in either section outside the specified time is returned to the supplier for reprocessing.
Second, a ‘drop box’ system may be operated with new garments placed into the top of the box and older garments taken from the bottom.
A procedure should control the transfer of all stock in and out of any production areas to satellite storage areas where it may be beneficial to run a Kanban system.
For secondary change areas positioned near the Aseptic Core simple visual aids, such as a ticket placed where the incoming operators can see it, can be used to notify them that certain garment sizes need re-stocking in advance of starting the gowning process. This can save operator downtime and frustration.
User training
Training should be provided using visual means, i.e. via video technology, as this not only demonstrates and standardises the correct aseptic gowning technique, but a recording of the operator’s gowning technique (particularly for higher classification areas) can also be used to offer particular feedback. Beer6 states that the use of video replay enables operators and the trainer to identify improper or subtle flaws in technique. This can have particular impact when used in conjunction with microbial monitoring – for example, when a trainee has their aseptic gowning technique assessed using contact plates. If a count on these plates comes back high it is useful to review this data in conjunction with the videotape to see if it corresponds to poor gowning technique, enabling the trainee to see exactly what aspects of the technique they need to work on.
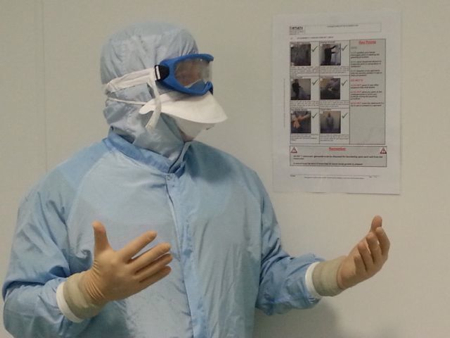
Photographs provide a quick reminder of procedure
Training should also incorporate hand washing/sanitising and other pre-requisite training courses, e.g. basic microbiology or aseptic technique, and should be completed in advance. After training, the trainee should have an opportunity to gown in a safe non-critical environment, allowing them to feel comfortable with all requirements. The trainer can then ensure the trainee is competent in the aseptic technique. This has the potential to reduce the microbial challenge upon the classified change areas when trainees are required to carry out simulated training runs in ‘live’ production areas.
UK-based pharmaceutical company, Ipsen Biopharm, has taken this approach one step further and has designed and built a purpose-built Aseptic Training Suite. The concept of this suite is similar to a trainee pilot using a flight simulator; it allows personnel to master critical techniques in a risk-free, off-line environment, while being exposed to the unique challenges a cleanroom may offer. The suite also offers the benefit of being able to assess the technique and capabilities of those applying to join the company. It is important that training is not a discrete event but an ongoing occurrence, within a culture where coaching and feedback is given routinely by experienced personnel.
Garment damage and washing
A Service Level/Technical Agreement between the garment supplier and the customer is recommended, which documents the specifics of the control of each garment: for example, maximum permissible numbers of washes, repairs (what and where damage or wear is allowable on the garment and also the maximum number of repairs), as well as transport and bagging requirements. Certain suppliers may also offer the ability to fold garments in a specific way to help aid the aseptic gowning process; again this detail would be documented in the Service Level/Technical Agreement.
Last, if any branding of the cleanroom garment stock is required, it should be ensured that this is achieved using a suitable grade print and that logos are not stitched onto garments, as this itself may damage the integrity of the fabric.
In summary, management of the aseptic garment process commences well before the operator dons a gown for cleanroom entry. The process must be lean, but practical in terms of the required availability of garments at all times and should be supported by strong, effective ongoing training. Following these protocols should also have a positive effect on product quality assurance.
References
1. Sandle, T (2012) A Guide to Cleaning and Disinfecting Cleanrooms, Grosvenor House Publishing, Surrey, UK.
2. J. Fredirick, J. Carleton & P. Agalloco, (1999) Validation of pharmaceutical processes: sterile products, 3rd Edition, Marcel Dekker, New York.
3. EudraLex, Volume 4 – The rules governing medicinal products in the European Union
4. Rules and Guidance for Pharmaceutical Manufacturers and Distributors (Revision to Annex 1 of Orange Guide, effective March 2014)
5. 21 CFR Part 211 – Current Good Manufac-turing Practice for Finished Pharmaceuticals - Subpart B – Organisation and Personnel
6. C. L. Beer, PDA J. Pharmaceutical Science and Technology May–June 1991 45:128–131
Brian Hayes is Chairman of the Cleanroom Action Group (CAG) of Pharmig and in charge of Aseptic Manufacturing at Ipsen Biopharm.
The author would like to acknowledge the input of CAG in the compilation of this article. Pharmig aims to publish these and other concepts in a ‘best practice’ guide on gowning in the future.