Advances in biopharmaceutical production and manufacturing techniques are driven by the need to reduce costs and hence the prices of pharmaceutical products. This is partly for commercial reasons: the pharmaceutical industry needs to make money to provide investment for further research and development.
However, it is also subject to additional pressures to reduce costs due to the ethical need to get treatments to patients. It is therefore essential to optimise all stages involved in bringing drugs to market, from early-stage research, through clinical trials, manufacturing and supply chain.
In pharmaceutical manufacturing, the pressure is therefore on to design innovative processes that reduce time spent and resources used. One such method to optimise manufacturing, which has been widely adopted across other industries, is continuous processing. It is a frequent topic of discussion in the biopharmaceutical sector and is now becoming increasingly common, although the industry has been relatively slow in adopting this approach.
It is essential to optimise all stages involved in bringing drugs to market, from early-stage research, through clinical trials, manufacturing and supply chain
Pharmaceutical processes require strict conditions to be met, both to successfully produce the required medicine and also to ensure its purity and regulatory compliance. This, therefore, requires more innovative processing design and places much higher demands on the equipment used.
Keeping the regulators onside
The FDA has stated its support for the implementation of continuous processing and the drive is on to design processes that satisfy regulators' cGMP requirements. In order to do this, manufacturers must be able to demonstrate that the process is aseptic throughout and each component has the required validation.
Single-use technologies are therefore becoming increasingly popular as they reduce the risk of contamination and can be efficiently integrated into many production lines. The onus is on suppliers to provide high-quality data on extractables, leachables and to validate sterility.
Choosing your tubing
Peristaltic pumps are often chosen in these systems as nothing but the pump tube touches the fluid, eliminating the risk of the pump contaminating the fluid, or the fluid contaminating the pump. As such, there is now a greater value placed on tubing and tubing assemblies within critical fluid paths, ensuring they maintain their integrity and do not risk contamination either from external sources or from degradation of the tube material itself.
There is added complexity because of the loads placed on the tubing by the pump and the resultant dynamic wear. A peristaltic tube must deliver confidence that it will not fail within the process cycle time and that it will deliver consistent flow rate over this time. Choice of tubing can, therefore, have a significant impact on the success of any fluid process.
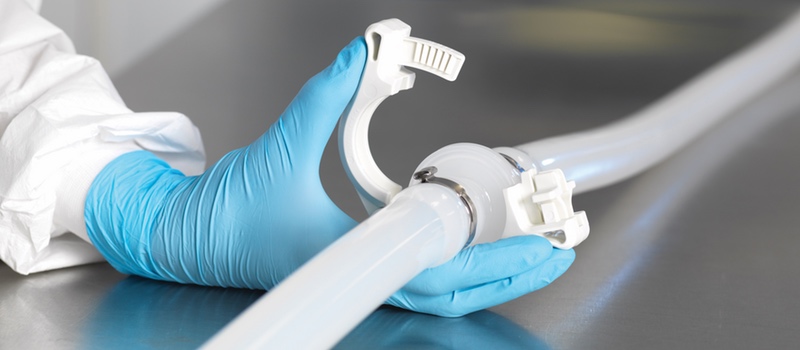
PureWeld XL tubing is manufactured in ISO 14644-1 Class 7 cleanrooms
Thermoplastic elastomer (TPE) is now frequently the tubing material of choice due to its compatibility with sterile welding and sealing technologies, performance and levels of purity that meet the expectations of the industry and regulators. In addition, the worldwide shortage of silicone raw materials has brought an additional focus to the implementation of TPEs.
Preparing for continuous processing
Single-use technology has solved many problems faced by biopharmaceutical manufacturers, but the increasing adoption of continuous processing brings additional challenges that this technology must withstand.
Continuous systems operate with much longer run times of up to 90 days, compared to two to 14 days for fed-batch processing. This means every component of the system must maintain its integrity for a significantly longer time.
Peristaltic tubing must provide the confidence that it will not rupture or degrade due to the extended periods of dynamic wear. The level of control required by continuous processes also means that the tubing should deliver a consistent flow rate over the duration of the production cycle to maximise product yields and minimise the damage to live cells.
How does your tubing compare?
The growth of continuous bioprocessing has driven the need for drug manufacturers to pay close attention to the functional life of single-use components. Flexible tubing suitable for continuous bioprocessing must demonstrate confidence that it will deliver long peristaltic life under typical process conditions.
Watson-Marlow Fluid Technology Group has undertaken a study comparing the peristaltic life and pumping performance of its PureWeld XL TPE tubing with two leading industry alternatives.
The test investigated flow stability, pumping performance and peristaltic life. The results showed that PureWeld XL maintained higher flow rates at stronger discharge pressures and over longer time scales than competing products. For the company, the study not only demonstrates that PureWeld XL stands up to the technical challenges presented by continuous bioprocessing by delivering extended peristaltic life and flow stability but also emphasises the need to carefully analyse the available data when choosing tubing. The full results of the study are available to download from the company website.
All TPE tubing is clearly not the same and it is therefore important to compare tube life and flow stability to ensure the tubing chosen stands up to the technical challenges presented by continuous bioprocessing.