Wipes are widely used in cleanrooms and play an instrumental role in safeguarding critical environments in a variety of industries such as pharmaceuticals, medical device manufacturing, biotechnology, compounding pharmacies, and electronics.
A cleanroom is a sensitive environment that must be monitored for contaminants and harmful airborne debris. Contaminants can be found naturally in the air and can also come in the form of dust, microorganisms, particles, and more.
In order for a cleanroom to sustain its appropriate cleanroom classification, employees not only have to follow stringent Standard Operating Procedures (SOPs) but also use the right products that are specifically designed for cleanrooms. Compared to ordinary wipes, cleanroom wipes have lower levels of lint or shedding to minimise the contaminants. In general, they are also engineered to have higher absorbency, better compatibility with chemicals and more effective cleaning capabilities.
Top: Nonwoven microfibre
Middle: Polyester knit
Bottom: Nonwoven polyester cellulose
Key performance metrics
When selecting the right wipes for your cleanroom, you should evaluate a few performance metrics and base your decision on manufacturers’ data and information on those metrics. These include the recommended ISO classification of the wipe, shedding or linting potential and the cleaning capability.
Recommended ISO classification – Each manufacture should provide recommended ISO classifications for their cleanroom wipes. Wipes with different ISO classifications should be used in corresponding cleanrooms.
Shedding or linting – Shedding or linting determines the cleanliness of the wipe. It is measured in particles and fibres released from the wipe. The cleaner the wipe is, the less deposition onto cortical surfaces during wiping. The ISO recommendation for each wipe is largely dependent on how clean the wipe is.
Cleaning capability – This measures each wipe’s ability to remove different kinds of contaminants such as dust, stain, microbes and particles etc. The wipes’ capability is determined by the material and construction of each wipe and has little to do with the chemicals that will be used when cleaning. There are multiple tests to evaluate the mechanical cleaning performance of cleanroom wipes and most of those tests are conducted with just water.
Absorbency – This has two aspects: rate of liquid absorption and total amount of liquid absorbed. This metric measures how effective each wipe is at picking up liquid or spills. Another metric that is related to absorbency is release. A well-engineered wipe can not only absorb a sufficient amount of liquid but can also release the liquid in a consistent manner onto the surface to maximise the coverage of each wipe.
Softness – if you have sensitive equipment in your cleanrooms, it is important to select wipes that will not cause damage to this equipment.
Common substrates
Cleanroom wipes can be made of different substrates and they each have their own unique performance characteristics and cost position. Understanding the pros and cons of each material is critical to selecting the most ideal wipe for the cleaning needs of your particular environment. Some of the most common cleanroom wipes are made of nonwoven polyester & cellulose blends, nonwoven polypropylene, knit polyester and microfibre (both nonwoven and knit).
Nonwoven polyester cellulose – This is one of the most widely used materials for cleanroom wipes. It is very cost effective and boasts great absorbency. One major downside to this material is that it comparing to other materials, it tends to release more particles and/or fibres to the environment so it is not as clean. Polyester cellulose is a great choice for cleanrooms with less restrictive air particulate requirements.
Nonwoven polypropylene – This material is not only cost effective but also very clean. However one major weakness of polypropylene is that it doesn’t absorb well. That is why most nonwoven polypropylene wipes are in the pre-saturated format and used as carriers for liquid application.
Polyester knit – Knit polyester cleanroom wipes are made with 100% continuous filament knit polyester and are sometimes called woven wipes because of how they are constructed. These wipes releases extremely low fibres or particles making them suitable for cleanrooms with higher classes. They are also ideal for cleaning sensitive equipment due to their exceptional softness. On the flip side, polyester knit wipes are more expensive than nonwoven wipes largely due to the manufacturing process.
Microfibre – This is a relatively new material and is gaining momentum as more and more people start to realise the superior cleaning performance it delivers. Thanks to its extra fine fibres, microfibre can remove various contaminants more effectively than other substrates. Some advanced microfibre wipes claim to remove 99.9% of particles down to 0.1 micron. The chart (figure 1) shows the particle size of different microorganisms in comparison to human skin cell. This is an innate mechanical removal capability of microfibre that has nothing to do with chemicals. Some chemicals have microbe kill claims but they don’t actually remove dead microbes from the surface. Dead microbes, if remaining on the surface, will become food for live pathogens and allow them to proliferate. That is why a microfibre wipe that can remove those microbes from the surface can provide additional insurance to safeguard the environment.
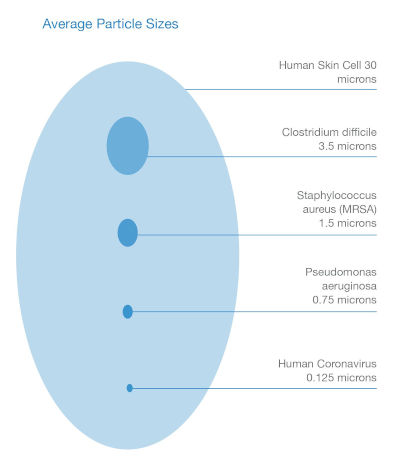
Microbe size chart
Microfibre’s superior cleaning performance is also manifested in its ability to effectively pick up stain and residuals. A recent test conducted by a third-party lab compares the stain removal ability for nonwoven polyester cellulose, polyester knit and nonwoven microfibre. The pictures comparison shows remnants of stain on the surface after 4 wiping strokes with each wipe.
Another reason that explains the increasing adoption of microfibre wipes in cleanroom is that it serves as a logical bridge between polyester cellulose and polyester knit. Compared to polyester cellulose, although there is a cost premium, it is a lot cleaner and softer. While on the other hand, compared to polyester knit, it has better absorbency and is more cost effective.
All in all
When choosing cleanroom wipes, it is important to establish key performance criteria for each cleaning environment and application. Select the right wipes that can deliver on those metrics. Each wipe substrate has its own advantages and deficiencies compared to others, and while there may not be a perfect wipe out there for everyone, you can sure pick the perfect wipe for your cleanroom.