Cleanrooms in the Pharmaceutical industry are sanctuaries of precision, where the highest standards of cleanliness are not just expected but demanded. A key player in the sterilisation arsenal of these cleanrooms is Vaporised Hydrogen Peroxide (VHP), a potent chemical used to disinfect surfaces and equipment. However, the nature of VHP, while highly effective at sterilisation, presents unique challenges, including equipment deterioration. In this blog, we will explore the significance of VHP in Pharma cleanrooms, the potential impact on sensitive equipment like particle counters, and how Lighthouse’s Apex particle counters have been engineered to withstand VHP exposure.

Understanding VHP: A Sterilisation Powerhouse
Vapor Hydrogen Peroxide (VHP or H₂O₂) holds the esteemed title of a sterilant, a classification by the U.S. Environmental Protection Agency (EPA) for substances capable of eliminating all microbial life forms, including bacteria, spores, fungi, and viruses, in inanimate environments. This powerful compound played a pivotal role in decontaminating buildings during the 2001 anthrax attacks and has proven effective against various pathogens, including avian influenza and Newcastle disease. In the biopharmaceutical world, VHP is a trusted ally used in hospitals and pharmaceutical manufacturing facilities.
Why Pharma Cleanrooms Rely on VHP
Cleanrooms engaged in the production of drugs, biological products, and medical devices adhere to rigorous sterilisation protocols. Surface disinfection, with hydrogen peroxide as a disinfectant, is a cornerstone of these procedures. The quality and thoroughness of surface disinfection, including its in-situ execution, directly impact product safety, quality, and human health.
Some pharmaceutical manufacturing processes operate round-the-clock to meet the demand for critical healthcare products, minimising offline shutdowns. Consequently, most sterilisation processes occur while the cleanroom remains operational. This makes it paramount to select equipment capable of withstanding VHP exposure.
Potential Impacts on Particle Counters
VHP is generated through the vaporisation of liquid hydrogen peroxide, resulting in a mixture of VHP and water vapour. This “dry” process maintains VHP concentrations below the condensation point, a critical parameter influenced by room temperature. For room decontamination, VHP concentrations typically remain below saturation, ranging from 0.1 to 1.5 mg/L at 25°C. However, for medical device sterilisation, higher VHP concentrations may be utilised at elevated process temperatures, often reaching 60°C.
When VHP concentrations surpass the saturation point at a given temperature, hydrogen peroxide preferentially condenses out, forming concentrated peroxide on surfaces. While this condensed peroxide maintains antimicrobial properties, it may introduce variability into the sterilisation process and potentially damage surfaces—a concern that extends to all equipment within a cleanroom, including particle counters.
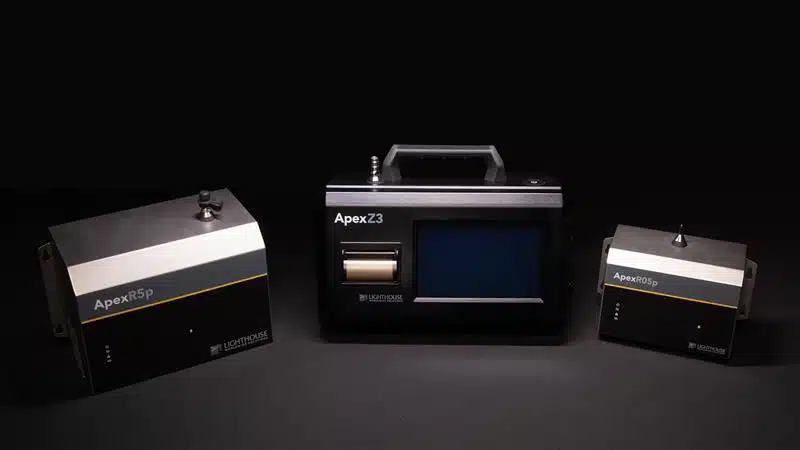
Lighthouse Apex Particle Counters and VHP Compatibility
Two decades ago, the compatibility of particle counters with VHP would have been a resounding “no.” However, Lighthouse has evolved its particle counter technology to withstand the effects of VHP. The Apex series of particle counters from Lighthouse are meticulously designed to prevent VHP from infiltrating the unit. This sealing of the housing and display effectively protects sensitive electronic components and pumps.
Furthermore, Lighthouse has engineered its sensors to be VHP-tolerant. Extensive testing confirms that VHP does not induce corrosion within the sensor. Moreover, Lighthouse’s Apex particle counters feature self-diagnostics that continuously monitor sensor health through eight diagnostic checks. Any deviations from tolerance trigger alerts, ensuring data integrity.
Real-World Significance of Lighthouse Apex Particle Counter Health Checks
The self-diagnostic capabilities of Apex particle counters are invaluable. They can detect the presence of contamination within the sensor, enabling immediate removal and investigation. In the absence of such diagnostics, users might only discover data inaccuracies during calibration, resulting in potential product quality issues and delays.
Particle counters rely on light scattering to convert particle size into an electric signal. When VHP residue coats mirrors and optics, it can distort light scattering, leading to sizing errors and inaccurate particle counts. Without self-diagnostics, users may remain unaware of these errors until it’s too late.
Using Lighthouse Apex Particle Counters with VHP Sterilisation
Lighthouse has conducted extensive studies to validate the compatibility of its Apex particle counters with VHP exposure. The tests involved subjecting ApexZ portable particle counters and ApexR remote particle counters to multiple VHP exposure cycles. These particle counters were pre-calibrated, exposed to VHP, and then recalibrated.
The results were conclusive: VHP exposure had no detrimental effects on the Apex particle counters. Neither external nor internal abnormalities were observed. The rigorous testing demonstrated that Lighthouse Apex models are compatible with VHP as long as the VHP process remains non-condensing, and room temperatures remain below 25°C.
Conclusion: Lighthouse Apex Particle Counters and VHP Compatibility
Lighthouse’s commitment to innovation and rigorous testing has produced Apex particle counters that can confidently withstand VHP exposure, both externally and internally. These particle counters have been designed to endure the challenges of harsh cleaning and disinfection programs, providing reliability and data integrity. With Lighthouse Apex particle counters, biopharmaceutical cleanrooms can ensure accurate data, product quality, and patient safety, even in the presence of a powerful sterilant like VHP.