Medical Air Technology (MAT) was appointed to replace Royal Devon and Exeter Hospital NHS Foundation Trust's containment level 3 (CL3) facilities in 2021, following a competitive tendering process.
This work was successfully completed and the Trust now has a brand-new state of the art laboratory that futureproofs its ability to safely process High-Risk specimens from hospital and community patients for years to come.
Zero cases of COVID-19 amongst the MAT personnel on site
All work was carried out and completed over the course of the pandemic. This presented some challenges with regards to material shortages and delays of vital components, but thanks to close cooperation between MAT, suppliers and the hospital, any delays were kept to an absolute minimum, illustrating one of the many benefits of working with a single total turnkey provider rather than multiple contractors. A safe working environment was maintained at all times, resulting in zero cases of COVID-19 amongst the MAT personnel on site.
The nesting birds were very aggressive towards anyone attempting to access the roof
One unusual problem encountered was due to seagulls, which had chosen to nest on the roof where the new mechanical plant was to be located. The nesting birds were very aggressive towards anyone attempting to access the roof, so works had to be postponed until the new fledglings had left the area. However, this did not hinder the success of the project, and the microbiology department was extremely happy with the work carried out by MAT.
Fabulous feedback from the microbiology department
“We are incredibly pleased with the work and the workmanship from the whole MAT team. Having a team who know what they are doing with regard to constructing CL3 laboratories proved critical in this type of project. Their knowledge of the building requirements, application of the build, and production of the finished product was seamless,” said Matthew Allen, Laboratory Manager.
“The MAT team were efficient, accurate and incredibly tidy. During the build, everything was orderly and the team were active in keeping all access and work areas neat and tidy. There was minimal disruption to the Pathology laboratory/offices/parking, and all major deliveries and use of the crane for siting of the AHU were carried out at weekends or out of regular office hours to minimise the impact.
“There were hiccups along the way - nesting seagulls, for example, which delayed the project, especially when installing the AHU. All delays were managed with minimal overall impact on the project.
“We would recommend this team for any laboratory development. They were brilliant - knowledgeable, accurate and efficient. We couldn’t be more pleased with how MAT managed the build, and ultimately delivered the finished product.”
The new CL3 lab
CL3 is the highest containment level in common use in the UK, and laboratories of this type require certain features to be incorporated into the design to ensure appropriate containment. The MAT design team, experts in critical ventilation, worked closely with the microbiology department to turn the plans for the new laboratory, to include rooftop mechanical plant, into reality.
Airflow plays a vital part in the design of CL3 facilities. Control of Substances Hazardous to Health (COSHH) regulations require that at CL3 the workplace must be maintained at an air pressure negative to atmosphere to stop the escape of hazardous pathogens. This is achieved by the specialist airflow created by the HVAC system, a critical part of the containment process, which establishes and maintains the negative pressure and thus ensures containment and operator safety.
External windows were replaced with new highly-efficient units containing solar reflective glass
With many successful CL3 projects to its name and a wealth of experience in critical ventilation, MAT delivered a technologically advanced laboratory that complies with all necessary HSE guidelines. Work started with a strip-out of the four existing laboratories, located on the third floor of the Pathology building. The total turnkey installation included a full electrical and mechanical package, a BMS control system to supply the extract air systems, three Class 1 microbiological safety cabinets, a new pass-through autoclave and specimen hatch, dedicated waste disposal options, and new furniture, as well as safety and security features for staff.
As part of the project, the external windows were replaced with new highly-efficient units containing solar reflective glass, which reduces the amount of heat entering the building. A full successful fumigation efficacy study of the facility was also carried out and the new laboratory was handed over following commission and validation.
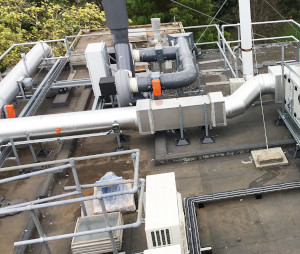
Why turnkey?
A total turnkey installation streamlines process and saves time and money. It eliminates the problem of having to deal with multiple suppliers and delivers a solution that is immediately ready to use on completion. Customers benefit from a more personalised service and a designated account contact. Issues are addressed as a whole, not in parts, avoiding the inconvenience of coordinating an array of often disparate trades and equipment. In short, working with a total turnkey provider like MAT makes everything easier for the customer, as well as being more cost-effective.